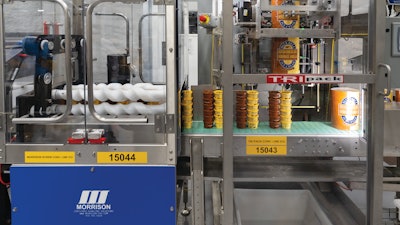
Brenham, Texas-based Blue Bell Creameries is one of the few ice cream manufacturers in the country that relies on its own direct store delivery system and personnel rather than sending its frozen treats through central distribution centers. Naturally, the many Blue Bell route sales representatives who stock supermarket freezer cases in parts of 23 states provide feedback on how packaging performs as they go about their duties. And for some time now they noted that there could be improvements made to the popular 12-count loose-fitting pre-made polyethylene bags that have been used historically. What’s more, the folks in sales and marketing were convinced that the on-shelf appearance of the product would be improved if the secondary packaging got an upgrade.
Route sales representatives and the sales/marketing team weren’t the only ones who found shortcomings in the bag format. Facilities project manager Russell Halfmann explains how the loose nature of the 12-count units presented challenges in automating the case packing operation.
“We’ve always felt that manual case packing was too labor intensive, but finding an automated case packer that would accept such irregular and inconsistently shaped units was challenging,” says Halfmann. “Still we kept looking, and eventually we came across a way of shrink sleeving the single-serve cups that lends itself to automated case packing and that lets our route sales representatives in the stores efficiently and attractively stock the freezer case.”Single-filed cups of vanilla and single-filed cups of chocolate are shown here entering the Morrison turning and grouping screws.
Blue Bell achieved the shrink sleeve format Halfmann refers to by installing a Tripack machine with custom tooling. It drops a shrink sleeve over 12 cups of ice cream in two six-high stacks, one stack of chocolate and one of vanilla, and shrinks the sleeve in a heat tunnel. The result? A 12-count multipack with a consistency and rigidity that facilitates automated case packing and is considered more attractive in the supermarket freezer.
But the shrink sleever is only half the story. Getting the cups of frozen ice cream to behave upstream in a manner that would permit automated shrink sleeve application was an even greater challenge. And that, says Tripack business development manager Marc Tredo, was where Morrison Container Handling came in. They came up with an integrated multipack system that turns, stacks, inspects/rejects, combines, and groups the single-serve containers so that the Tripack sleever can do its thing.After turning screws have turned cups onto their sides (photo above), grouping screws send groups of six cups into a chute and then onto a dividing plate (A) that carries the group down to the floor level and the shrink sleever.
“We’re good at what we do, but we also know what partners it pays to work with,” says Tredo. “Whenever we face a challenging timing-screw solution, we usually turn to Morrison. We knew we’d need a timing-screw assembly to receive two stacks of cups each six-high. But in very short order it became clear that a sizeable build-out ahead of shrink sleeving was going to be required.”
“Getting containers to the Tripak was definitely a challenge,” says Halfmann. “We really worked with Morrison for the concept, and they came up with a way to incorporate the change in elevation and increased production rate. All these criteria kind of folded into their solution. It boiled down to getting mass conveyed cups sitting lid-up and turning them on their sides so that we could create stacks of six and then getting those stacks of six down from an overhead level so that we could marry them in pairs to be conveyed into the shrink sleever.”Shown above, top and bottom turning screws (B is the top screw and C is the bottom one) reorient cups so they no longer sit on their bottoms but rather lie on their sides. Then a pair of grouping screws (D is the left grouping screw and E is the right one) forms cups into groups of six.
Two identical lines
Cups ride in groups of six down parallel elevators and are then pushed at a right angle onto two parallel flighted conveyors.
• a filler
• a blast freezer
• accumulation and single filing conveyor system
• Morrison container handling equipment
• an elevator to take stacked groups of six cups from mezzanine down to floor level
• more Morrison container handling equipment to merge and properly space pairs of stacked cups
• a Tripack shrink sleeve applicator and shrink tunnel
• an automatic case packer.
Since each line is a carbon copy of the other, we’ll look at just one here. Unlike the rotary filler used previously, the filler selected by Blue Bell is a Tetra Pak intermittent-motion cup filler. It denests paper cups and sends them into filling nozzles eight across. Four cups get vanilla and four get chocolate. Once filled, the cups have injection-molded LDPE lids that are singulated and applied by way of a friction fit.
Exiting the filling and lidding system the cups enter a DSI Dantech spiral blast freezer, which discharges frozen cups at an overhead level. The cups proceed en masse down a Shuttleworth accumulation table that uses gradually faster conveyor sections and angled guides to singulate the cups into two single-file rows, one chocolate and one vanilla. The Blue Bell team incorporated a Keyence machine vision system to monitor feed rates and inspect the cups.
As soon as the cups pass through a Mettler Toledo metal detector, they enter the first set of Morrison-designed timing screws—six for vanilla and six for chocolate. Since the same thing happens for each flavor, we’ll look at just one here. First are top and bottom turning screws. Cups reaching them are sitting on their bottoms but when they exit this pair of screws they have been smoothly turned on their sides. Immediately after is a pair of grouping screws that forms cups into groups of six and sends them into a chute leading to the elevator that will take them down from mezzanine to floor level. Each group of six rests on a dividing plate as it makes its descent.
At the end of their elevator ride, the six-high stacks are pushed at a right angle onto a flighted conveyor. Considering how tall the stacks are and how abruptly each one is pushed, it would seem that this is a golden opportunity for stacks to topple over. But two design features serve to prevent it. First, the tooling that does the pushing is just as tall as the stack, so it more or less cradles the stack from top to bottom to prevent toppling. And second, the stack gets pushed into a well-placed plexiglass backstop that prevents any chance of toppling and actually serves to square the stack up in case any cup takes a notion to wander even the least bit. Then, once the stacks are on their flighted conveyor, smooth and topple-free conveying is assured by independent servo drives that keep the conveyors in time.Tighter, more consistent, and easier to run through an automated case packer, the shrink sleeve multipack (right) has been a big win for Blue Bell Creameries, compared to the legacy format (left).
So now we have two parallel lanes of stacks heading to a V-shaped merging station designed by Morrison where the stacks leave their two separate flighted conveyors and merge onto one common conveyor in a chocolate/vanilla/chocolate/vanilla arrangement. A photocell verifies that each stack has six containers and that the stacks are indeed in the alternating chocolate/vanilla/chocolate pattern. Any incorrect stacks are automatically rejected.
Timing screws stacked three-high
One more set of Morrison timing screws remains. It’s a stacked screw system where three stacked screws on the left and three on the right guide stacks of cups forward with just the right spacing so that the roll-fed Tripack machine can cut and deposit a shrink sleeve—which gets date-coded by a Videojet heat-transfer unit before it’s cut from the continuous roll—over each stack. Then, after a short time spent in the shrink tunnel, the finished multipacks emerge onto an accumulation table that leads in short order to case packing. “It gives us about a minute or two of accumulation in case there’s a delay at the case packer,” says Halfmann.
Details on the material specs and supplier for the shrink sleeve are not available largely because there was a bit of development work involved in getting a material that would shrink effectively and perform well throughout the supply chain. Adding to the challenges is the fact that the packaging equipment and steam tunnel are located in a semi-refrigerated environment.Before cups reach the Morrison timing screws that upend them and group them into stacks of six, cups exit spiral blast freezers—one for chocolate, one for vanilla—at an overhead level and move through this accumulation table that singulates the cups into two single-file rows, one chocolate and one vanilla.
The Cama wraparound case packer brings a welcome measure of automation to the Blue Bell operation. “If you look at the overall upgrade from where we were to where we are now, we estimate a 28 percent increase in throughput and a 35 percent reduction in labor costs,” says Halfmann. “Much of that labor cost savings comes from going from manual to automated case packing.”
Multipacks are conveyed into the case packer single file and collated into groups of six. Then an overhead arm pulls the six onto a case formed from a corrugated blank that has been pulled from a magazine and erected. Case flaps are closed with an application of adhesive delivered by a Nordson unit. Next is case coding, another area where Blue Bell was able to shave costs by getting away from pre-printed corrugated cases and relying instead on a Videojet ink-jet coder for whatever information the cases need.A key goal in the new approach to multipacking was to make automated case packing a possibility. Shown here is the wraparound case packer now running on both lines.
“We were able to get away from a pre-printed box to a completely blank box that we print just downstream from the Cama case packer,” says Halfmann. “We print product ID and date code and line number and even some graphics. This case identification information is really important because our route sales representatives rely on visuals to pick cases from the truck. So having that clearly printed product code on the case is what they need.”
Once finished cases have passed the coding station, they enter a Ryson spiral conveyor that takes them to an overhead conveyor leading to an existing Motion Control Robotics palletizing system some distance away. “We upgraded the palletizer to accommodate a new case format,” says Halfmann. “We used to put four multipacks in a case and now we put six multipacks in a case. It was a good way to be able to keep the same palletizer without overwhelming it by the increased number of multipacks per minute we are now able to produce.”
Even under ideal conditions bringing an installation like this into commercial production would have been challenging enough. But Blue Bell had to do it in the teeth of the pandemic.Primary packaging also got a serious upgrade with the installation of Intermittent-motion filling machines that fill cups eight across—four chocolate, four vanilla.
“The spiral freezers were what I ordered first, just before the COVID-19 shutdown, because we thought they would have the longest lead time,” says Halfmann. “It turned out the freezers got here before everything else because of supply chain delays, especially where controls and automation components were concerned. But everybody had supply chain issues at that time. Fortunately, our machinery vendors worked with us with what parts they had on the shelf to do Factory Automation Tests as best they could. In some cases they’d ship us the equipment so we could do kind of a rough install and get past the majority of the installation ourselves, and then once that was accomplished and parts became available they were able to come out and recommission the machines for us. Suffice it to say it took a while to get all the bugs worked out, but with the help of our equipment partners and our capable and diligent in-house team we did. And we’re pleased to have an appealing multipack that can be case packed with automated equipment.” PW