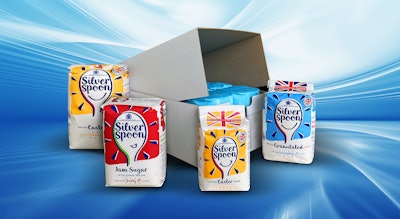
The leading producer of sugar for the British and Irish food and beverage markets, British Sugar processes around 8 million metric tons of U.K.-grown sugar beet each year to produce up to 1.2 million metric tons of sugar. The company’s core offering is granulated sugar, but it also manufactures a wide range of other specialty products, such as icing sugars, brown sugars, and liquid sugars and syrups, among others.
With increasing consumer demand for its products and escalating sugar sales, the company recently replaced its 38-year-old end-of-line packaging equipment with new machinery from Sidel. According Sidel Account Manager Bastien Carcenac, Sidel custom-designed the solution for British Sugar, identifying its challenges to deliver a full end-of-line turnkey solution from the sugar bagging outfeed through to delivery at warehousing.
![]() | Download this related content, “Researched List: Zero/Fast Changeover Case Packers,” updated regularly by Packaging World. |
“British Sugar required an extremely compact and flexible case-packing and palletizing solution to be implemented within a tight plant area that would be capable of handling multiple pallet and format types to accommodate single sugar bags to new shelf-ready secondary packaging,” explains Carcenac. “Case-packer and palletizer flexibility, reliability, and output speed were central to the desired end-of-line solution for British Sugar, with Sidel’s design and equipment focusing on achieving flexibility at a high speed using advanced robotics.”
The initial equipment installation included two Cermex BC46 tray and lid case packers and seven PalAccess palletizers with robotic layer preparation. Four stretch wrappers, conveyors, and elevators are scheduled to be installed at a later date.
Turnkey solution offers countless possibilities
As Carcenac confirms, flexibility was key in the selection of the new end-of-line equipment for British Sugar. “Flexibility is achieved through case-packing and palletizing systems that allow a large packaging range, from mini to maxi bags and also cases, as well as being easy to adjust when performing changeovers—either automatic or simple tool-less, when an operator is needed,” he says.
The Cermex BC46 combines tray forming, loading, and lidding into a single machine.
The Cermex BC46 combines tray forming, loading, and lidding into a single machine, making it suitable for shelf-ready or retail-ready packaging formats. The unit can handle a number of different lid styles, including U-shaped, cross, and others, with the lid and tray evenly pressed during operation, ensuring squaring of the package. The unit operates at 26 blanks/min, depending on the product and collation.
During operation of the Cermex BC46, lid blanks, which are stacked in an adjustable flat magazine with a 1,200-mm-long belt, are extracted and positioned by a rotating arm with suction cups in the lidding station. There, batched products are elevated onto the lid through a die, after which the lid is formed around the batch by the die, incorporated into the loading pusher. For products without counterpressure, blades are used to form the lid around the batch. Next comes tray loading of the lidded batch. Like the lids, the trays are stacked in another adjustable flat magazine. From there, they are extracted and positioned in a U-shape between brackets by a rotating arm with suction cups. The blank is held between the brackets by folding or guiding the long bottom flaps. A bridge and loading funnel then deflect the flaps and guide the lidded batch onto the tray blank. The lidded batch is then transferred into the blank with motorized front and rear guides. The lid can be fitted inside (sealed with hot-melt glue or simply inserted) or outside the tray.
To palletize cases and single bags of product, British Sugar installed seven PalAccess automatic layer-by-layer modular palletizers.
To palletize the finished trays, British Sugar added seven PalAccess palletizers. “The modular, layer-by-layer palletizing platform PalAccess, equipped with robotic layer preparation, was selected to guarantee high product integrity through sensitive and reliable handling of small and unstable packs,” says Carcenac. “This was a necessity for British Sugar, as it had many different format types that required sensitive handling.”
Before being palletized, cases—or single bags, depending on the pallet format—are grouped into layers using a robotic layer preparation system. It comprises a dosing conveyor that counts and separates packs, a transfer table made up of a mat of flat chains for channeling and conveying the packs at the right speed, gripper heads that transfer and turn the packs into the correct position, and a layer forming table for positioning the packs according to the chosen palletization pattern.
The system allows for rapid format and pallet pattern changeovers, which are managed completely by software with no manual adjustments required, and enables a potentially unlimited number of pallet patterns to be created.
“The robotic infeed system prepares the layers by orienting and positioning the bags and cases according to the pallet pattern,” says Carcenac. “The complete layer is then delivered to the palletizer and then a pusher transfers the complete layer to the pallet, layer after layer, until the pallet is completed and sent to outfeed via roller conveyors.”
![]() | Read this related column from Sterling Anthony, “The Importance of Pallet Patterns” |
Following installation of the new end-of-line equipment in 2023, James Warby, project integration manager at British Sugar, commented on the company’s experience with Sidel. “We needed a partner with strong engineering and design expertise as the challenge was more complex due to the building constraints combined with our high level of technical specifications,” he said. “Sidel’s collaborative approach from the beginning was excellent. They have been agile and transparent where we have had to work together to find solutions. Their shared vision of a packaging line with our engineering team strengthened the trust we had in their capacity for delivering a turnkey solution and led us to decide to partner with them for this project.” PW