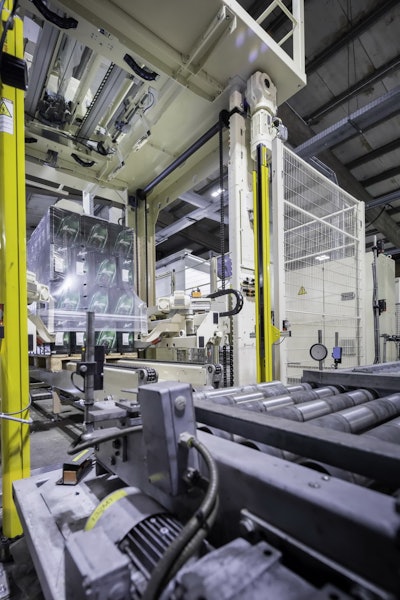
From Beumer, these systems package the palletized beverage cases quickly, flexibly and sustainably with a stretch hood film. In Eltville on the Rhine (Hesse), Beumer has adapted the packaging system so that the film size is changed with respect to the pallet size. These systems enable the Sektkellerei company to reduce shipping and complaint costs considerably in the medium term.
The Rotkäppchen-Mumm Sektkellereien GmbH headquartered in Freyburg at the Unstrut in Saxony-Anhalt is leading producer of sparkling wine in Germany. They are also one of the top producers of various spirits and wines. Owing to their production of exclusive wines, the Rotkäppchen-Mumm Sektkellereien hold a "Sparkling wine" market share of approx. 50 % in the food trade. The company group currently has around 550 employees and produces at five different locations in Saxona-Anhalt, Thuringia, Hesse and Baden-Württemberg. Production Manager Karl-Josef Lauzi describes the Hesse Sektkellerei: "In Eltville on the Rhine near Mainz, we have a very traditional location". Lauzi has been working for the Sektkellereien for over 30 years and is responsible for the entire Rotkäppchen-Mumm production operation. Lauzi explains, "the company was founded in 1811. The well-known sparkling wine brands are Mumm, MM Extra and Jules Mumm; all of which are produced at this location."
The various beverages are filled and bottled automatically, closed with cork, agraffe and capsule and provided with a corresponding label. Next, they are packed into different corrugated cases. The packaged bottles are picked up by a palletizer, which stacks them onto pallets. Prior to implementing Beumer technology, the upper surfaces of the corrugated cases were glued and transported to a binding machine where the palletized beverage cartons were tied up. Beverage cases would then be carried through the pallet transport system to the goods issue - where they can be prepared for the shuttle truck of the logistics service provider. Every year approximately 300,000 pallets leave this location. However, in the past, due to frequent hard braking, sudden steering moves and sharp curves, during transport, cases loosened themselves from the compound, falling onto the loading space. The result was broken bottles and lost product. "For a faster material flow in their central warehouses many customers rely on automatic loading and unloading systems," says Lauzi. This requires product to be sufficiently secured and protected.
In order to reduce damage during transport and to meet the increased logistics requirements, Sektkellerei searched for a packaging solution to ensure safer and more stable beverage stacks. "At the beginning of 2012, the Engineering and Logistics departments contacted us with a concrete request", recalls Klaus-Dieter Enzenbach, Sales Manager at Beumer Maschinenfabrik GmbH in Beckum. In order to demonstrate their innovative engineering, Beumer invited the Sektkellereien team to Beckum to carry out packaging testing of their products. "In the testing hall, the impressive Beumer stretch hood M, high-capacity packaging system, was presented", says Joachim Engler. After testing, the benefits of the stretch hood became clear and both the shrink wrapping and the stretch wrapping techniques were eliminated as packaging options, as they did not meet Sektkellereien's requirements due to high film consumption. "The Beumer high-capacity packaging system pulls a 40 micrometres thin film hood over the palletised beverage cartons. Optimally packaged, the cartons are protected against damage during transport and reach the customer in perfect order," says Engler. "Moreover, two different pallet sizes can be packaged with this multi-format system. The change is semiautomatic and it is not necessary to retrofit the system. Thus, we are well prepared for future requirements".
In order to demonstrate the conformity of the product and the increased stability of loads packed with the BEUMER stretch hood M, Beumer and Rotkäppchen together with DEKRA, the world's leading expert organisation for safety, quality and environmental protection, performed different driving tests under extreme conditions. The results were favourable and in March 2013, Beumer was awarded with a contract including supply, installation and commissioning of the high-capacity packaging systems.