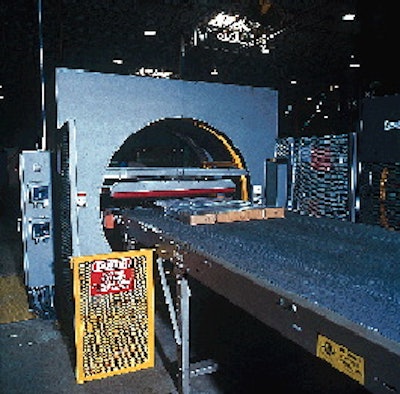
With a new breed of cast stretch wrap films made from metallocene resins offering greater puncture resistance, high elongation and low noise compared to conventional cast films, many packagers are beginning to take a closer look. Office furniture giant Steelcase, Inc., Grand Rapids, MI, is one of the first users of one of these films, Max Plus I, a linear low-density polyethylene film. It's part of the MaxTech(TM) series of metallocene cast films recently unveiled by Pactiv Inc. (Pittsford, NY), which the supplier claims is one of the first such breeds on the market. (Editor's note: Pactiv purchased the Mobilrap stretch film business from Mobil Chemical in November '95.) Steelcase's Athens, AL, plant uses the film to overwrap individual panels that are used in the construction of office cubicles. The panels are wrapped on two Lan-ringer® horizontal stretch wrapping systems from Lantech (Louisville, KY) after being fitted with corrugated end caps from Menasha's Sus-Rap Packaging Div. (Danville, VA). According to Phil Dortch, a Steelcase packaging engineer who was involved in the switch, it represented an opportunity to move from a LLDPE blown film, which the plant had been using, to a cast film. There are two benefits to this. First, cast films are generally quieter during wrapping than blown films, according to Greg Hardin of Dillard Packaging Systems (Greensboro, NC), which sold Steelcase the stretch wrapping equipment and distributes the film. Blown films require additives to create the cling that's inherent in cast films. Two stretch wrappers running simultaneously with blown film-especially the very high-end film Steelcase had been using-made a tremendous amount of noise in an otherwise quiet manufacturing environment, according to Dortch. The second benefit of switching from blown to cast film, according to Dillard's Hardin, is economics. Cast films are typically less expensive than blown films. But prior to metallocene cast films, no cast film would have been able to handle the Steelcase application, requiring the performance (and the expense) of a high-end blown film. Indeed, the metallocene film was so tough that it enabled Steelcase to downgauge from a 100-ga blown film to an 80-ga cast film, representing a slight savings for Steelcase. That's not to say that metallocene films are inexpensive. "[The metallocene cast film] is among the most expensive cast films," Hardin admits. But a traditional cast film wouldn't have been able to handle the requirements of this application, he says. Metallocene-based cast films have begun to blur the distinction between blown and cast films, both in performance and economics. According to Tenneco, this film is made from metallocene resins designed specifically for stretch film manufacturing. During the polymerization process, the resin manufacturer, Exxon Chemical Co. (Houston, TX), adds a catalyst based on a combination of metallic and organic compounds. This metallocene catalyst allows Exxon to incorporate the desired stretch film properties into the resin. Pactiv then uses a cast film manufacturing process it developed specifically for metallocene resins to produce the cast films.