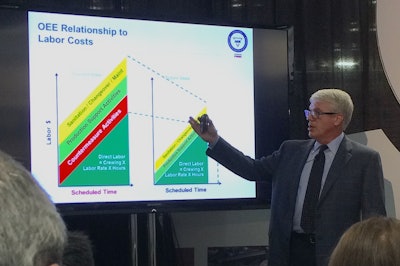
A new toolset for consumer goods companies pursuing overall equipment effectiveness (OEE) provides a way for companies to identify the savings and improvements as well as the ROI of OEE activities. Specifically, an OEE Opportunity Calculator and OEE Validation Calculator, help justify the operational benefits of quality and efficiency gains in dollars and cents. They are available as free downloads from the Alliance for Innovation and Operational Excellence (AIOE).
ConAgra Foods, in helping to develop these tools as a standard offering, has used them to improve operations for at least three ConAgra plants “for about eight years now, and it’s uncovered all kinds of opportunities for improvement,” said Peter Hock, senior director of continuous improvement with ConAgra Foods, in a presentation with Steve Schlegel, managing director for AIOE, at Pack Expo 2014. He says he's one of about a half dozen AIOE members who have used the tools at their food and consumer goods companies, in cases developing more advanced models.
The resulting OEE tools are offered as a free download by AIOE. Hock explained the value of the spreadsheet offering and demonstrated how it works.
Hock noted that the spreadsheet tools help track and optimize the relationship between interrelated factors that affect unit cost, such as production volume, raw material costs, labor expense, utilities and various overhead items. How these interrelationships play out became evident in examples of snack-pack lines where, for instance, multi-head carousel-type combination weighers are highly reliable high-speed machines, that, if not maintained correctly, can dispense the wrong amount of product. This results in downtime, waste and countermeasures and support activities such as rework of improperly filled bags.
To illustrate how OEE can improve such situation, Hock displayed before-and-after production states to illustrate reductions in raw material yield loss (cost) factors such as overfill and giveaway’ scrap, waste and quality rejects; and end-of-run purge/sanitation costs. (See Fig. 2) He did the same with labor cost-drains in terms of sanitation/changeover/maintenance; production support activities and countermeasure activities. (Fig. 1)
The effort to make OEE work is a benefit in itself, in some respects, because in order to gain improvements through OEE, a company has to have “much more skilled operators who are much more engaged,” which in turn increases their knowledge of production operations, and the likelihood those operators will be able to play a greater role in sanitation and other areas that can improve operating results.
"Some definite, immediate chunks' can be had through the effort it takes to train employees and embark on OEE. For instance, a plant can make the same mount of product shorter amount of time with OEE, Hock says, "so if I'm running five Sundays in a quarter, and I get a 10 percent improvement in OEE," I may be able to schedule fewer Sundays. I may be able to schedule fewer Saturdays. And get the work done in five-day weeks."
As with other areas served by AIOE, this effort is designed to reduce the inefficiency of industry-wide duplication of efforts by companies following processes that are largely the same for all companies.
The question arose in the Pack Expo session from an employee with the Kellogg's brand: "Do you ever get to the point of diminishing returns?" Hock replied that a plant with 90 percent efficiency might want to speed-up the line and see what happens before diving into additional methods to gain another two-percent OEE improvement. On the other hand, many lines are running at efficiency levels in the area of 65%, in which case, Hock says "I guarantee you won't even recognize how much money you're going to save when you can actually improve 10, 15, 20 points." He added that OEE and related continuous improvement methodologies have proven these kinds of improvements at plants around the world.