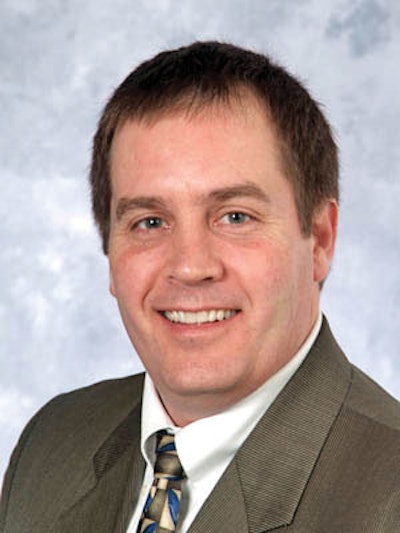
In todayβs environment of fuel surcharges and offshore manufacturing, itβs important to understand how carriers determine billable weight for shipping charges. Packaging professionals can play a direct role in minimizing logistics expenses for their company if they have a better understanding of Dim weight (Dimensional weight) and GAD weight (greater of actual or dimensional weight).
If you review the terms and conditions of carriage of your transportation provider, you may find they use simple math formulas to determine the billable weight they charge your shipment. Many carriers will use GAD weight. What this means is they are actually basing shipment charges on your packaged productβs volumetric density. Why, you ask? Because carriers have limited space in their vehicles and want to maximize the weight and cubic volume capacity of those transport vehicles every time they move the transport vehicle from origin to destination.
Here is how Dim weight works:
1. Weigh your package.
2. Determine cubic volume of your package by multiplying outside package/shipment length x width x height. Be sure to understand how your carrier treats fractions and how their rounding policy works.
3. Divide the cubic volume calculated by your carrierβs dimensional weight factor.
4. Be aware that the dimensional weight factor can vary by carrier, destination, mode of transport, and other factors.
5. Billable weight will be the greater of the actual weight or the dimensional weight.
Here are two examples to illustrate these points:
Single corrugated box
Actual weight: 43 pounds
Outside dimensions: 30.4β x 18.6β x 15.2β
Cubic size calculation: 30β x 19β x 15β = 8,550 cubic inches
Dimensional weight calculation: 8,550/ 133 = 65 pounds (rounded up from 64.3 pounds)
Billable weight will be 65 pounds, not the actual weight of 43 pounds
Palletized load
Actual weight: 485 pounds
Pallet dimensions: 42β x 48β x 6β
Load dimensions: 40β x 40β x 48β
Outside dimensions of shipment (load on pallet): 42β x 48β x 54β
Cubic size calculation: 42β x 48β x 54β = 108,864 cubic inches
Dimensional weight calculation: 108,864/194 = 562 pounds (rounded up from 561.1)
Billable weight will be 562 pounds, not the actual weight of 485 pounds
Here are a few things you can do to help get billable weights as close to optimal as possible:
β’ Review the terms and conditions of your transportation providers to determine their Dimensional weight policy.
β’ Calculate the Dimensional weight of your shipments and compare it to the actual weight to determine if you will be paying GAD. Pay special attention to your carrierβs rounding requirements and dimensional weight factors for different modes or destinations.
β’ Increase cubic volume density by minimizing voids in packages. This can be done by resizing boxes, reconfiguring the product, or by using higher performance cushioning material that protects to the necessary levels of shock at thinner thicknesses.
β’ If you are paying actual weight, then consider using lighter-weight materials to reduce your overall billable weight.
β’ Use pallets that are as close to the load dimensions as possible.
β’ Use tools such as palletization software or engineering software to help maximize pallet-use efficiency.
β’ Negotiate dimensional weight factors with your carrier. If your company is a large enough shipper, carriers may be willing to negotiate the dimensional weight factor they use in calculating your shipments.
Consider the total cost of getting the product to the end-user and not just the package unit cost. I have personally worked on projects where the package I designed and specified was more expensive per piece than previous packages. However, due to my understanding and application of GAD principles, I was able to spend less of my employerβs money to get the product to the end-user.
Bottom line: Look beyond actual package cost and weights for cost savings. Knowing your carrierβs terms and conditions of carriage is critical not only for determining your billable shipping cost but also understanding other packaging requirements and liability issues that can have a huge impact on your companyβs profitability.
About the Author: Robert Meisner, CPP, is assistant professor at the University of Wisconsin Stout and Executive Vice President Education on the IoPP Board of Directors. He has held various packaging positions at companies including 3M, Eastman Kodak Co. and United Parcel Service Supply Chain Solutions. For more information on IoPP, visit www.iopp.org.