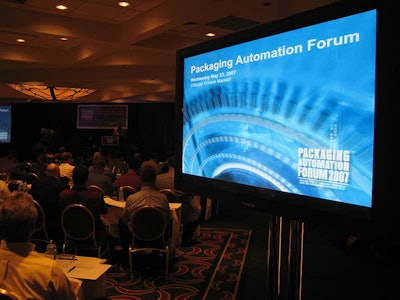
Can packaging automation reduce inventory carrying costs, streamline supply chains and enable marketing strategies?
Yes, according to Packaging Automation Forum speakers that included automation experts from General Mills, Eli Lilly, Procter & Gamble, Nestlé, Frito-Lay, Tropicana and the Make2Pack group.
And the trend was clear. Packagers are looking beyond incremental throughput improvements and faster changeovers – although important -- to strategically uncover hidden savings and new revenue generators.
Vision versus gaps
Gregg Stedronsky, vice president of engineering for General Mills, was the keynote speaker. And he nailed the topic of “between the vision and the plant floor,” identifying the gaps between innovation and standards, business imperatives and enabling technologies.
For example, with the acquisition of Pillsbury -- which doubled the company’s size overnight -- they inherited plants and learned that a “one size fits all” standard no longer fits.
The sixth largest food company in the world, General Mills has evolved into a $12 billion food company with an international footprint in over 100 countries -- rather than a cereal company with just a few plants.
Part of the vision is supply chain performance, critical to the company’s future in order to maintain margins, enable innovation and create flexibility
For food companies, supply chain is “field to fork,” or at General Mills “wheat to Wheatie.”
Now, packaging has become recognized as a supply chain solution with the flexibility to, for instance, run more than one product on a line.
And amid changing consumer habits, packaging has been a key driver for their product innovation, channel and international expansion, margin growth and brand building.
‘Can’t shrink to greatness’
But, “You can’t shrink to greatness,” Stedronsky reminded the audience, meaning that while cost cutting accounts for 20% of productivity increases, innovation is the other 80%.
Commodity prices, retailer power, new product complexity, rising health care costs and pricing pressure all point toward “growing a demand-driven supply chain network to accelerate the manufacturing process”. This requires agility in manufacturing, better inventory visibility, faster replenishment and in general running faster and better than their competitors.
The concept of “information everywhere” means that factories must be connected to suppliers and corporate offices. Other industries, such as UPS in the shipping business, understand this.
The vision is to reduce working capital with less inventory and faster replenishment, and to improve asset utilization with the right product manufactured at the right time and faster changeovers. That, according to Stedronsky, is a billion dollar equation.
It will mean direct customer ordering, flexibility to decrease inventory, better lot tracking and better diagnostic tools to speed repair.
From art to science
General Mills has made great progress. Production efficiency has exceeded expectations. Plant dashboards track which unit operation caused a problem. Electronic capture of information helps diagnose problems that can be elusive to determine: a problem at the cartoner may be caused by missing a bag upstream, and that can be difficult to track down.
He emphasized the need for a single plant database, not multiple databases. For a centralized corporate information system. And for standard technology. OEMs and contractors need access to the networks. Plants need to understand and take part in the process.
Their MES system turned process quality from “art to science.” This provided standardized recipes for products such as Cheerios, so that tweaking was not part of the solution. They also partnered with IT to make data handling a by-product of the control systems.
Packaging priorities
Stedronsky defined packaging priorities as innovation, performance, flexibility, capital cost and footprint.
To begin with, he noted that servos and PC technology have reduced packaging machinery footprint and cost while increasing efficiency.
He described innovation as equipment that can make a new consumer product or package that in turn increases incremental sales, revenues and profits.
The desired performance increases the efficiency of the entire system, reduces costs, and increases margins and therefore profits..
Flexibility equates to fast changeovers to be able to run lots of products on the same platform -- or more than one format on same line -- and reduce inventory, improve return on assets.
Capital efficiency means doing more projects with same capital budget.
Footprint means no need to make new investments in bricks and mortar. This is especially true for mitigating the risk of new product launches. Therefore, getting better asset utilization by shrinking equipment size is preferable to building. Smaller footprint reduces cost per case and increases margins.
The power of invention
While controls and information are enabling technologies, the competitive advantage doesn’t come from the controller itself, it comes from the motions performed.
“We may love what the inventor did even though the control scheme doesn’t fit our technology,” Stedronsky said. “Inventors should stay focused on innovation. System reliability should be so high that the choice of underlying control system should be transparent.”
The trend is to become less likely to demand a single controls platform. Instead, packagers are seeking connectivity with dissimilar platforms. Companies are unable to afford to ‘rebuild’ controls to meet their standards and end up with equipment that isn’t as good as it was before. There is a greater need for diagnostics and there is pressure for the plant floor to align with company information systems.
In turn, technology partners need to provide more connectivity, downtime analysis and diagnostics across the system, not just the unit ops, and for free. They want to be able to buy the HMI that comes with the equipment and have an industrywide level of standardization to connect with the equipment -- for free.
Stedronsky said that packagers can no longer afford to limit invention by limiting their OEMs’ choice of technology. Packagers cannot accept the time and cost to force their absolute controller standardization on machinery inventors -- who are then pushed into developing “hidden prototypes.”
Forum sponsors, OEMs concur on innovation focus
For some of the sponsors and machine builders attending the forum, the keynote deftly summarized what ARC Advisory Group described in last summer’s analyst report “Packagers’ Automation Specifications Must be Aligned with Business Strategies and Foster Innovative Machine Design.”
The second annual forum was supported again by charter sponsor and packaging automation specialist ELAU, along with packaging performance analysis specialist Zarpac, plus a number of general purpose controls and HMI vendors.
Among the machine builders in the audience was Zoran Momich, president of Z Automation Company, who holds multiple patents on cartoning technologies that have resulted in higher speeds, with unstable package formats and gentler handling of products.
“Machines that fulfill the five packaging priorities – innovation, performance, flexibility, capital cost and footprint – are already here,” Momich reflects. “You have to seek out the innovators, but the equipment is on the market. You can find machines that are recipe driven, 100% faster, 50% smaller, with 10 minute changeovers instead of 4 to 8 hours, and with much higher efficiency.
“But innovative machine builders can go a step further. We must take more of the systems approach that Mr. Stedronsky is recommending of packagers. This is evident in the instant popularity of the PELS alliance – for Packaging End-of-Line Solutions – that we are spearheading along with Goodman Packaging Equipment, Packaging Machines International and ELAU for a common automation platform.
Also present was Paul Zurlinden, manager of technical systems for Pro Pack Systems, which is known for case erecting and packing systems among other packaging technologies.
"As an OEM, it was very beneficial to hear what the trendsetters in packaging operations want on their production floors, said Paul Zurlinden, Pro Pack's Manager of Technical Systems.
"It lets me know what I need to be doing from the controls end to provide them the information they're looking for. I realize that the control technologies to serve up that data are readily available, from ELAU and other vendors we're using.
"As far as capital cost goes, ELAU provides so much of the capability as standard in their equipment that 'information for free' is already part of the controller, it's just a matter of me bringing the data out where they can see it.
"We have a very small footprint case erector. We're actually performing product identification on the cases as well as case erecting in a footprint that many are exceeding with just one of the steps in the process."
All agreed that machines fulfilling the packagers’ priorities are available on the market. It’s often simply a matter of breaking with the status quo to accept innovation. The trick is getting innovation inside people’s comfort zones.
Maintenance should support, not limit, innovation
Packagers can also no longer let their familiarity with legacy technologies become the limiting factor in achieving technical progress. “If you follow the philosophy that we can only use what we already support in the plant,” he explained, that won't make the plant competitive.
He made an analogy with cars, asking the audience to remember when cars were unreliable and everyone was a shade tree mechanic. Even though technology has become more complex, the improved performance and reliability are “worth it.”
Automotive innovation wasn’t halted because the spare parts and maintenance strategy had to deal with increased complexity. The spare parts strategy didn’t drive the innovation strategy – it had to support innovation.
But he did not offer carte blanche to innovators. “To a consumer products company,” Stedronsky cautioned, “a machine that doesn’t perform significantly better or enable a new consumer offering is not innovative, even if the underlying technology is.”
Closing the gap
The vision is about future outputs, actionable information, standard and recipe based controls, building an information infrastructure, and connectivity.
Plant floor is about achieving today’s output, with the priority on cases produced, building packaging systems where multiple stand-alone controls platforms and custom code are okay.
Packagers will close the gap by taking a system and enterprise perspective. They will align company strategies to industry working groups. They will support industry initiatives and embrace a philosophy of “assembly” of software components vs. “custom code.”
Other industries, he noted, have discovered this. “We need a true north.”
The future: equipment that’s ‘worth it’
Stedronsky sees General Mills finding the solution by continuing to buy equipment based on packaging priorities and by supporting activities that help industry standards move forward.
“Controls companies should create connectivity, provide functionality, be open, and create tools for (software) assembly that are industry standards.”
Over time, General Mills will request equipment that is industry compliant. But they will also resist a proliferation of controls hardware – the equipment must be “worth it.” Stedronsky says “We don’t need one controls platform. We probably need two or three. But it would be insanity to have six.”