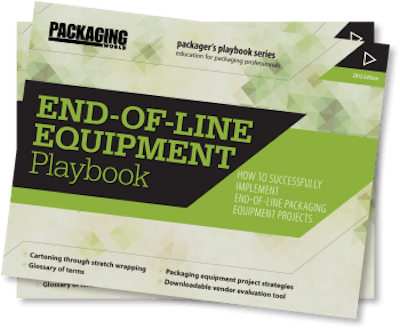
1. Look for more hybrid solutions and simultaneous operations. The effort to reduce secondary packaging is accelerating, which is having a significant impact on the design of palletizing equipment. The trend is driving hybrid palletizing solutions involving both conventional and robotics technology. Simultaneous operations are also becoming more prevalent, such as palletizing and stretch wrapping in a single integrated piece of equipment. Increasing numbers of package applications are better suited to fully automated equipment; thus, the need for package handling flexibility involving quick “tool-less” or fully automated technology.
2. Weigh total cost of ownership and future needs. ROI tends to favor conventional palletizers at very low and very high speeds. Despite varying opinions, proponents of robotics claim to handle a wider range of SKUs and package types, and cite applications involving more than 60 cases (or multipacks, etc.) per minute. Beyond speed and costs, consider your application. For example, when one bottler’s conventional palletizer was damaging lightweighted bottled-water multipacks, the company chose robotics for gentle handling and newfound sustainability cost savings.
3. Don’t forget about safety when updating palletizing technology. Safety systems are having a huge impact on the design of equipment today, with an ever-increasing importance placed on the use of safety-rated devices such as PLCs, VFDs, and automatic air dumps. Some palletizing equipment is pretty wide, and must be cordoned off. Adhere to all safety procedures. Establish strict protocols to make sure safety is not compromised.
4. Consumer-level developments and graphics technology may affect your machine decisions. Warehouse stores are driving more display-type pallet loads and cases. In turn, this drives the need for graphics-out palletizing, often requiring the placement of tier sheets between layers and corner boards to improve load integrity and warehouse stackability. It may also require you to think about hooding versus stretch wrapping—a single layer of hood film will show off graphics and bar codes more easily.