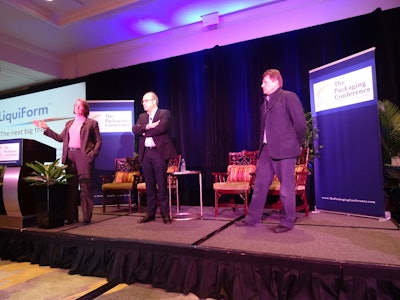
Ten years in development, LiquiForm™—which removes the “blowing” from blow molding and integrates forming and filling in one step—is “on the precipice of commercialization.” That’s according to Ann O’Hara, President of LiquiForm, who addressed attendees at the 2015 edition of The Packaging Conference, in Atlanta, along with her colleagues, Tod Eberle, Amcor Rigid Plastics Vice President, and Luc Desoutter, Sustainability Officer for Sidel, Inc.
In July 2014, Amcor announced a joint partnership with Sidel to develop LiquiForm, which Eberle says was inspired by Sidel’s Combi integrated blowing-filling-capping system. “We asked ourselves, is there an opportunity to go further and combine stretch blow molding and filling in one technology that is compatible with PET and other materials?” he said.
The resulting technology engineered by the partners—advertised as “a step change in efficiency and flexibility”—uses consumable, pressurized liquid instead of compressed air to form plastic containers, resulting in a significant decrease in energy costs. For standard blow molding, the air compression cycle is only 35% to 40% efficient and consumes approximately 70% of the total amount of electricity used in the blow-molding process. LiquiForm uses much less electricity to hydraulically drive incompressible fluid into the container while it’s forming at a much higher efficiency.
Among the other benefits of the technology cited during the presentation were:
- Reduced maintenance and labor costs versus operating two separate machines
- An optimized supply chain
- Lower capital costs and a smaller machine footprint
- Potentially sharper bottle definition
- Reduced waste with enhanced technology
- Greater filling accuracy
- Lower GHGs
- Reduced transportation costs
- Package damage associated with empty bottle transport eliminated
- Greater design window for polypropylene and high-density polyethylene applications
As O’Hara explained, Amcor and Sidel have recognized that the best way to bring the technology to market is by licensing it to equipment manufacturers. “Licensing is a good way to go, as there are so many different applications that are going to have to be worked through,” she said. Videos shared at the conference offered a glimpse of some of the product potential, including condiments, beverages, and personal care products—“although we may not get to high-viscosity products immediately,” O’Hara remarked.
When asked if Amcor was jeopardizing its own business by introducing a technology that will allow brand owners to form their own bottles, O’Hara responded: “Amcor feels that this transformation was coming anyway. It offers us an opportunity to expand into other [global] markets.”
Per Amcor/Sidel’s timeline, the predicted path forward for LiquiForm is to have the first commercial production application by 2018, with broader adoption and continuous development in three-plus years. Said O’Hara, “The things we think are constraints today are things that we just haven’t figured out yet.”