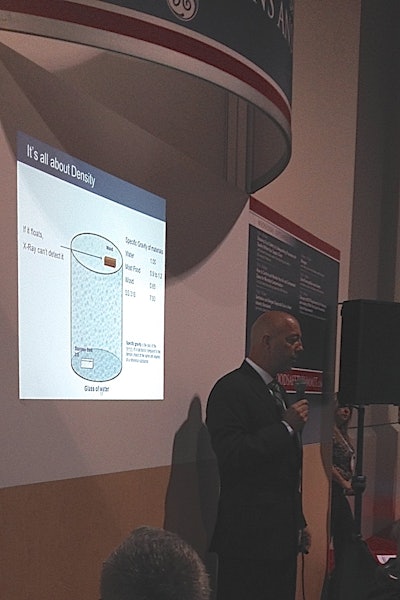
"If it floats, X-rays can't detect it," Mettler Toledo's Rogers said at Pack Expo.
Enhanced food safety regulations and standards are driving food processors and packagers to look more closely at how to arrive at an effective contaminant detection program. Robert Rogers, senior advisor for food safety and regulations at Mettler-Toledo Product Inspection, says that the question of which technology to use—metal or X-ray—isn't where the focus should be for a food processor, or even for a company that supplies inspection technology.
Rogers presented his thoughts on the topic in a presentation at the Food Safety Summit Resource Center presentation during Pack Expo 2013, and will again speak on the topic at the third annual Food Safety Exchange in Philadelphia June 17-18, 2014, which Mettler Toledo sponsors.
Metal detection has improved in accuracy and sensitivity over the years, but there remain some small or difficult-to-spot items that are difficult to detect. Some companies have found that multiple detectors on the line can catch contaminants, especially when a small stick-like object is oriented in different positions. Alongside metal detection, X-ray technology has come a long way to catch additional contaminants, depending upon the density (and specific gravity) of the contaminant. For instance, X-rays can detect heavier-density materials such as stainless steel, but not wood, wiith its light density. (See photo.)
"No technology does it all," Rogers said in an interview with Packaging World, adding that choosing between "isn't a matter of one typology being better than another; they both have things that they can and can’t do." Sometimes both forms of detection fit the bill. Companies assessing technologies must first "truly understand what the possible contamination sources are, and implement the best technology—or technologies—to mitigate that risk."
Once the detection program in in place with the proper sensitivity and reduction/elimination of false rejects, Rogers says the next step is "to have a plan for product to be rejected or alternately reworked," which must incorporate human processes so that only authorized personnel have access, and proper training, to handle that product stream. This is as true for single-machine installations as it is for fully integrated, automated lines that may include checkweighers, vision-based package inspection equipment, automatic rejection systems and software that incorporates tracking, documenting and statistical quality control/assurance functions.
Beyond machinery, the success of a product inspection program requires a strategy that's both systematic in its approach and affords the appropriate amount of training on details, down to how to maximize sensitivity, minimize false rejects and avoid electromechanical interference (i.e., cabling near high-voltage lines that can foul readings). For training to be effective, it must be part of the plant's larger food safety plan.
One of the earliest steps in a product inspection initiative is to examine the food process and identify the areas that have the highest risk. These areas can guide engineers' and food safety teams' decision-making when deciding where to locate equipment for the most reliable, efficient results, according to Rogers.
Companies in this article
Videos from Mettler-Toledo Product Inspection