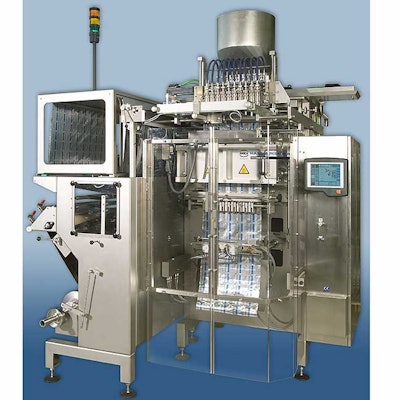
Hassia Redatron's Model Si500 ten-lane, four-sided sachet machine.
This content was written and submitted by the supplier. It has only been modified to comply with this publication’s space and style.
Bag forming, filling and sealing machines and four-sided sachet
machines by Hassia Redatron have been based on servo technology for
more than ten years. And yet, the company’s design engineers still find
opportunities for innovation. Now, they have introduced a new
multi-head dosing auger with single worm gear drive that provides a new
level of filling precision.
If it is about bags, four-sided pouch sachets or StickPacks of any shape and size, Hassia Redatron is a widely recognized solution provider. The company employs 60 people and recently joined the Packaging Division of the international Piltz Group.
Hassia Redatron can supply complete packaging lines, but its core competence is the bag, StickPack and four-sided sachet machinery itself. Constructed of stainless steel, the machines are primarily sold to the pharmaceutical, cosmetics, pet food and food industries. Niche market applications also play a role in the company’s business, such as lawn fertilizer bagging.
Intermittent or continuous motion operation
The portfolio ranges from simple machines to duplex and tandem machines, some of which provide a parallel filling and sealing process for ten to twelve webs. Maximum lateral sealing format widths are up to 600 mm for form, fill and seal machines, 500 mm for sachet machines and 300 mm for StickPack machines. This broad range enables production of comparatively large bags, even in multi-web configurations. And most of these machines can operate both intermittently and continuously.
One popular model, Hassia Redatron’s Si500 sachet machine, simultaneously forms, fills and seals ten bags. The film is slit into ten webs and then formed into tubes on parallel forming shoulders. Ten servo-driven augers fill materials from ten adjoining hoppers.
“Servo technology has been determining machine design across our product range for ten years,” says Matthias Becker, Sales Director Sachet- and StickPack Machines. “ELAU has long been our partner for automation technology. ELAU’s PacDrive system is our standard solution for all machine types. The PacDrive controllers not only provide the Profibus DP interface required for the sensor/actuator network, but also an Ethernet connection which is particularly interesting for product data acquisition and remote maintenance, for example.”
As early as 1996, servo technology was the basis for Hassia Redatron’s development of what it calls a pendular drive, a reciprocating mechanism for the sealing jaws which is state-of-the-art even today. Its dwell time is synchronized with the film transport servo drive to vary the lengths of bags produced.
Pushbutton changeovers
Over the course of many innovations, the current machine generation was provided with simplified and more reproducible product changeover capabilities, thanks to servo technology.
"This reproducibility is the prerequisite for simple and reliable parameter changes at the HMI," emphasizes Becker. “Hassia Redatron developed a user interface panel where the sealing time, sealing temperature and sealing pressure parameters can be precisely set. Each new product undergoes an individual optimization process. After that, new parameters can be selected with pushbutton ease.”
The latest flexibility improvement is quick-release clamps for the sealing tools. Changeover times are reduced while machine availability is increased.
The precision of the augers is another very important topic at Hassia Redatron. "Bottom line, packaging means dosing," says Heinrich-Stefan Möbs, Manager of Construction and Development. A precise dosing procedure reduces the so-called ‘giveaway’ which is otherwise frequently tolerated in exchange for assuring the minimum weight.
Precision dosing is of utmost importance in multi-web auger dosing. In conventional solutions with a centralized drive powering multiple augers, the outer auger fill weights inevitably differ from the inner augers because product flow from the hopper into the augers is not homogeneous.
Precise 10-head dosing auger, thanks to individual auger drives
In practice, to achieve regulatory compliance for minimum product weight, all the augers continue to run until the auger delivering the lowest product weight is finished. This can cut significantly into profit margins in high volume production or high value products.
Therefore, Hassia Redatron designed a multiple-head dosing system with an individual servo drive and digital scale for each auger. Mounted on top of the new 10-lane dosing auger section are ten PacDrive Intelligent Servo Modules, which integrate motor and servo drive in a single, compact configuration.
"The electrical cabinet couldn’t have accommodated ten more servo drives," explains H.-S. Möbs.
An extra electrical cabinet would incur cost and space penalties without adding any benefit. Instead, H.-S. Möbs leveraged ELAU’s new servo modules, which only require a single power supply in the cabinet to run as many as 25 machine-mounted servo modules. Servo modules, the common power supply and the PacDrive controller are connected by a flexible system of quick-connect cables and distribution boxes permitting tree, star and line network topologies, in any combination.
Additional electrical cabinet eliminated
That was the solution for H.-S. Möbs. "Using servo modules, we didn’t have to build a second cabinet for our new dosing system, which means considerable cost savings."
And since the Intelligent Servo Modules are integral to the PacDrive automation system, they are fully compatible with ELAU’s conventional servo motor and drive configurations.
Single hybrid cables transmit communications and DC power from the cabinet through the distribution boxes to each servo module. The snap-fit connectors replace multiple wire terminations, reducing both engineering and installation costs.
"Normally, ten servos mean twenty individual cables," points out H.-S. Möbs. "Instead we can connect everything from the PacDrive controller in the electrical cabinet by means of distribution boxes and hybrid cables."
Open profile design promotes hygiene
Along with advanced technology, cost savings are a strong driver at Hassia Redatron. To reduce cost while increasing reliability, it’s important to simplify mechanical systems and utilize standardized components.
For this reason, Hassia Redatron started by replacing the conventional machine frame with an open profile design across its product range. Similar to today’s automotive unibody designs, welded sheet metal profiles provide rigidity and reduce vibration. This concept generates additional benefits. There are no closed spaces where liquids or product residue can collect. Fabrication is simplified because fewer metalworking steps are required.
Hassia Redatron successfully introduced component standardization across the product portfolio. Modularization and shared design elements for the StickPack, bag, and four-sided sachet machines help streamline manufacturing and logistics. Matthias Becker explains that "modularization, of course, has its limits due to different application requirements. But we intend to extend modularity as far as possible."
If it is about bags, four-sided pouch sachets or StickPacks of any shape and size, Hassia Redatron is a widely recognized solution provider. The company employs 60 people and recently joined the Packaging Division of the international Piltz Group.
Hassia Redatron can supply complete packaging lines, but its core competence is the bag, StickPack and four-sided sachet machinery itself. Constructed of stainless steel, the machines are primarily sold to the pharmaceutical, cosmetics, pet food and food industries. Niche market applications also play a role in the company’s business, such as lawn fertilizer bagging.
Intermittent or continuous motion operation
The portfolio ranges from simple machines to duplex and tandem machines, some of which provide a parallel filling and sealing process for ten to twelve webs. Maximum lateral sealing format widths are up to 600 mm for form, fill and seal machines, 500 mm for sachet machines and 300 mm for StickPack machines. This broad range enables production of comparatively large bags, even in multi-web configurations. And most of these machines can operate both intermittently and continuously.
One popular model, Hassia Redatron’s Si500 sachet machine, simultaneously forms, fills and seals ten bags. The film is slit into ten webs and then formed into tubes on parallel forming shoulders. Ten servo-driven augers fill materials from ten adjoining hoppers.
“Servo technology has been determining machine design across our product range for ten years,” says Matthias Becker, Sales Director Sachet- and StickPack Machines. “ELAU has long been our partner for automation technology. ELAU’s PacDrive system is our standard solution for all machine types. The PacDrive controllers not only provide the Profibus DP interface required for the sensor/actuator network, but also an Ethernet connection which is particularly interesting for product data acquisition and remote maintenance, for example.”
As early as 1996, servo technology was the basis for Hassia Redatron’s development of what it calls a pendular drive, a reciprocating mechanism for the sealing jaws which is state-of-the-art even today. Its dwell time is synchronized with the film transport servo drive to vary the lengths of bags produced.
Pushbutton changeovers
Over the course of many innovations, the current machine generation was provided with simplified and more reproducible product changeover capabilities, thanks to servo technology.
"This reproducibility is the prerequisite for simple and reliable parameter changes at the HMI," emphasizes Becker. “Hassia Redatron developed a user interface panel where the sealing time, sealing temperature and sealing pressure parameters can be precisely set. Each new product undergoes an individual optimization process. After that, new parameters can be selected with pushbutton ease.”
The latest flexibility improvement is quick-release clamps for the sealing tools. Changeover times are reduced while machine availability is increased.
The precision of the augers is another very important topic at Hassia Redatron. "Bottom line, packaging means dosing," says Heinrich-Stefan Möbs, Manager of Construction and Development. A precise dosing procedure reduces the so-called ‘giveaway’ which is otherwise frequently tolerated in exchange for assuring the minimum weight.
Precision dosing is of utmost importance in multi-web auger dosing. In conventional solutions with a centralized drive powering multiple augers, the outer auger fill weights inevitably differ from the inner augers because product flow from the hopper into the augers is not homogeneous.
Precise 10-head dosing auger, thanks to individual auger drives
In practice, to achieve regulatory compliance for minimum product weight, all the augers continue to run until the auger delivering the lowest product weight is finished. This can cut significantly into profit margins in high volume production or high value products.
Therefore, Hassia Redatron designed a multiple-head dosing system with an individual servo drive and digital scale for each auger. Mounted on top of the new 10-lane dosing auger section are ten PacDrive Intelligent Servo Modules, which integrate motor and servo drive in a single, compact configuration.
"The electrical cabinet couldn’t have accommodated ten more servo drives," explains H.-S. Möbs.
An extra electrical cabinet would incur cost and space penalties without adding any benefit. Instead, H.-S. Möbs leveraged ELAU’s new servo modules, which only require a single power supply in the cabinet to run as many as 25 machine-mounted servo modules. Servo modules, the common power supply and the PacDrive controller are connected by a flexible system of quick-connect cables and distribution boxes permitting tree, star and line network topologies, in any combination.
Additional electrical cabinet eliminated
That was the solution for H.-S. Möbs. "Using servo modules, we didn’t have to build a second cabinet for our new dosing system, which means considerable cost savings."
And since the Intelligent Servo Modules are integral to the PacDrive automation system, they are fully compatible with ELAU’s conventional servo motor and drive configurations.
Single hybrid cables transmit communications and DC power from the cabinet through the distribution boxes to each servo module. The snap-fit connectors replace multiple wire terminations, reducing both engineering and installation costs.
"Normally, ten servos mean twenty individual cables," points out H.-S. Möbs. "Instead we can connect everything from the PacDrive controller in the electrical cabinet by means of distribution boxes and hybrid cables."
Open profile design promotes hygiene
Along with advanced technology, cost savings are a strong driver at Hassia Redatron. To reduce cost while increasing reliability, it’s important to simplify mechanical systems and utilize standardized components.
For this reason, Hassia Redatron started by replacing the conventional machine frame with an open profile design across its product range. Similar to today’s automotive unibody designs, welded sheet metal profiles provide rigidity and reduce vibration. This concept generates additional benefits. There are no closed spaces where liquids or product residue can collect. Fabrication is simplified because fewer metalworking steps are required.
Hassia Redatron successfully introduced component standardization across the product portfolio. Modularization and shared design elements for the StickPack, bag, and four-sided sachet machines help streamline manufacturing and logistics. Matthias Becker explains that "modularization, of course, has its limits due to different application requirements. But we intend to extend modularity as far as possible."
Companies in this article