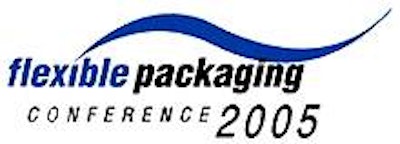
This material was presented by marketing manager John Kowal of Elau at last month’s Flexible Packaging Conference 2005.
It makes sense for package designers to collaborate with packaging engineers up front to make sure their new package design will run smoothly.
This is equally important whether the design objective is to cost-reduce the package or to add value, and whether existing or new machinery is planned.
To do so, it’s important for package designers to understand the capabilities in the marketplace and to help their engineering colleagues develop a sound business case if there is to be a capital project request.
Justify the investment
Factors to consider include lead time, footprint, startup time, changeover, mean time between failures and mean time to repair, throughput, material usage, reconfigurability, and regulatory compliance.
Footprint can be very important in an existing installation if it can prevent an additional investment in bricks and mortar. Likewise, a machine that is easier to reconfigure is less of a risk in the event the new product it was purchased for is discontinued.
Flexibility (fast changeover) and efficiency (factoring in speed, reliability, reduced scrap, etc.) are, of course, driving forces behind the move to servo machines, which enable capabilities such as on-the-fly “pushbutton” changeovers while they reduce the number of wear parts and change parts
Considerations
There is a direct relationship between speed and flexibility. Consider intermittent-motion machinery to handle multiple package formats at slower speeds, and continuous-motion machinery dedicated to a single format for sheer speed.
Traditionally, off-the-shelf machines have shorter lead-times than customized machines that may be needed to run an innovative package. But today, modular machinery with modular software is making it possible to offer customized capabilities from standard building blocks or modules.
In some applications, major strides in efficiency can be achieved by integrating manufacturing with packaging into one process. This is especially true when the product is converted from a web into a web-fed flexible packaging process, for example beverage and detergent powder “pods.”
A classic point of friction between designers and line engineers centers around the designer’s fondness for packages that, because they are unstable, are difficult to handle on a packaging line. If the package shape is critical to marketing, machinery requirements should be defined up front to avoid delays later in the project. If the package geometry is not critical, the package can be designed to run on existing machinery. Some companies now require these discussions on every project.
Since flexible packages flex by nature, machine designs that capture and maintain positive control of the package throughout the form/fill/seal process, often with grippers, are typically the fastest and most error-free. Strong seals and inspection systems to detect and prevent filling of any defective packages are also key considerations.
Interesting applications and machinery
Would some specialized machinery improve the process? For example, an equalization unit can even out the distribution of powdered product within a pouch, making for a better fit inside a carton.
Sometimes the package is the product, such as an intravenous bag, which is essentially a sachet-in-a-sachet that integrates inline aseptic filling, monitoring of sealing characteristics, and ultrasonic welding of a plastic closure to the external sachet, die cutting and hot stamping. The machine in this application is a custom design using 21 servos to automate the various steps.
Single portion packages are a hot topic. For example, Cardinal Healthcare’s patented DelPouch is a Flexible Packaging Association award winner. It includes a squeeze-to-open frangible seal and built-in applicator.
Another imaginative example is a laundry detergent pouch that dissolves in wash water at two different rates—first to release the soap and later to release fabric softener. The machine performs cold forming, vacuum forming, liquid filling, web lidding and web handling that accommodates film stretch.
Stick packs are a form/fill/seal application have become popular for portion-packaging of snack foods such as pudding because no spoon is needed. Features formed into the film include centered emptying geometry, contoured seals, and tear-open perforations. There are aseptic machines that feature clean- and sterilize-in-place designs.
More flexible packaging machinery innovations