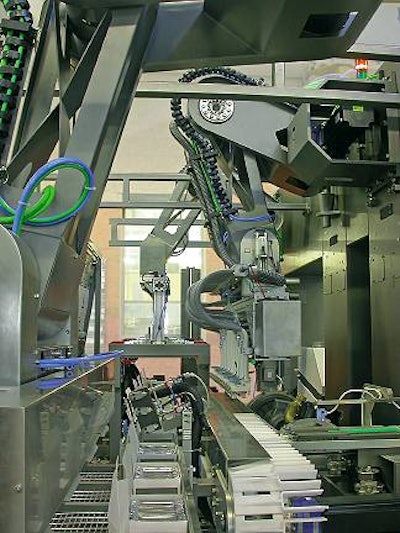
Cavanna introduces a new class of machine: Cartesio
With 45 years of flowpacking expertise Cavanna is moving downstream. They are using Interpack 2005 to launch a new range of robotic cartoning technologies with the support of packaging automation partner ELAU.
Cartesio is a new brand and a new system concept for using robotics in packaging developed by the Cavanna Robotics Division.
At Interpack Hall 14 Stand B30 Cartesio will be demonstrated in a fully automated and integrated line for the primary and secondary packaging of chocolate bars including a synchronized robotic island to form index and collate fill close and seal display cartons containing 18 bars each.
Innovative approach
Decidedly innovative the modular approach proposed by Cavanna integrates the forming filling and sealing operations formerly performed by independent machines into a single work unit. This integration has in fact reduced the overall footprint to 5000 x 2000 x 2000 mm with no compromise in functionality.
Fed by a 600 piece/minute flow wrapper upstream the system is configured with a first-in first-out (FIFO) vertical buffer system with up to 4 minutes of product storage. An input belt feeds a race track collator providing the Cartesio Model G35 robotic island with a continuous flow of oriented evenly space chocolate bars.
The first robotic arm picks and forms 4 cartons then inserts the in a chain conveyor controlled by two servo motors. Chocolate bars are fed from a circuit of buckets to a robotic transfer station. There the second robotic arm picks bars collates and packs bars vertically into 3 layers in each of 4 cartons simultaneously. The third arm is equipped with an interchangeable head for closing and hot gluing the cartons.
Each robot arm uses 3 servo axes and operates respectively at speeds up to 50 25 and 33.3 cycles/minute to synchronize operations between the stations.
Functionality and automation
The robotic island is automated by an ELAU PacDrive system consisting of 16 servo motors drives and a single integrated PacDrive C400 automation controller. The PacDrive system provides both technological and cost advantages over conventional PLCs motion controls and robotic controllers.
Traditionally robot suppliers require one proprietary robot controller per robot arm. ELAU enables Cavanna to perform robotic kinematics merely by adding an IEC 61131-3 conforming software object to the application program in the PacDrive automation controller – a breakthrough freeing packagers from proprietary software and hardware to learn and to support for each of their robot suppliers.
The robotic software object is part of ELAU’s extensive library of IEC software objects called Function Blocks. ELAU supports all of the IEC languages allowing them to be used together to their best advantage in the application program. For example ELAU Function Blocks (FBs) contain Structured Text (ST) code and sophisticated algorithms making them powerful and fast.
In ELAU’s programming framework Sequential Function Chart (SFC) provides a graphical easy to understand and diagnose state machine. Ladder Diagram (LD) and Function Block Diagram (FBD) are available for sequential PLC functions. As a result ELAU’s programming best practices allow Cavanna to provide highly functional easily visualized and validated automation software with extremely fast execution.
PacDrive’s hardware architecture plays a pivotal role in support of this software strategy. Unlike PLC-based control systems which are optimized for turning software bits on and off PacDrive is based on a ruggedized embedded Pentium M processor that can handle mathematical computations file handling and the sophisticated software structures that ELAU’s programming framework and software library make possible. PLCs are typically limited as to number of software objects that their proprietary processors can run.
Highlights of an automation system designed for packaging
High speed machines require highly dynamic servosystems. ELAU’s PacDrive automation system for example offer low-inertia brushless servo motors equipped with high-resolution encoders and electronic name plates – chips that communicate with the servo drives to simplify setup.
The PacDrive system actually offers several advantages. Here is a quick overview:
• Highly dynamic servo motors the absolute single- or multi-turn high resolution encoders
• Reduced software development time thanks to an extensive library of pre-tested reusable packaging automation software objects
• Integration of powerful motion and logic control capability on a single processor for maximum performance
• A programming framework enabling use of all IEC languages to their best advantage within a single application
• A single environment for software development parameterization and maintenance
• Standard field bus communications (Profibus DP Master/Slave 12MB CAN 2.0a or CanOpen)
• High performance rugged embedded Pentium processors
• 8 channel integrated oscilloscope with 1 ms resolution
• integrated data log for text mode display of diagnostic messages
• Connectivity through serial or Ethernet TCP/IP and Modbus RTU
• One or more PacDrive controllers can be connected via Ethernet to one or more HMI
• Electronic motor nameplates allow auto-recognition by drives for simplified motor replacement
• Detailed diagnostic information available via the SERCOS service channel
A family a company
“We are a family company with a strong entrepreneurial spirit” says Riccardo Cavanna Managing Director of Product Development and Customer Relations for Cavanna S.p.A. Mr. Cavanna and his sister Alessandra Cavanna Managing Director for the Company and for Marketing today run the company that was founded 45 years ago by Mario Cavanna.
Over that time the company has never lost its entrepreneurial verve and now the second generation has continued to grow Cavanna into a mid-tier enterprise.
“We are proudly continuing the tradition of a successful family business” Riccardo Cavanna continues. “This is a sentiment shared by our 200 employees all skilled and motivated professionals. They’re ready to take on the global market and they’re equally proud of belonging to a company that enjoys a strong reputation worldwide.
“From the beginning we have exported our systems throughout the world” Cavanna explains “and we have earned ourselves a key role among the world’s food packaging companies. We do business with multinationals as well as small- to medium-sized confectionary makers. Both need skilled suppliers capable of quickly understanding and fulfilling their needs. Our success depends on maintaining a dialogue with our customers so that we can anticipate their needs and deliver the appropriate solutions. It also depends on our natural propensity toward innovation.”
Toward a more flexible industry:
Modular hardware software and mechanics
With the robotic island modularity becomes the latest tool in Cavanna’s packaging automation strategy. Each robot arm is a coordinated module within the island synchronized with infeed systems and the other packaging machines in the line.
In the broadest sense automation plays a fundamental role in today’s lean manufacturing initiatives to regain competitive advantage. To achieve increased equipment efficiency shorter machinery leadtimes and faster format changes the relationship between automation supplier packaging machine builder and consumer packaged goods producer is pivotal.
ELAU has commissioned a study on this subject tracking product package and packaging machine trends in various market segments. Based on a survey of over 100 companies in the consumer goods industries in Europe North America and Japan the study reveals a growing number of new and complex packages designed to reflect an innovative image for the products they contained.
In food and beverage the trend is ever more apparent as no one doubts packaging’s role as a prerequisite to commercial success. It is in fact packaging that serves as the link between manufacturer and consumer using portion size package shape quality and usability to differentiate products. This profusion of package designs in turn places more challenges on both the machine builders and users.
The ‘universal’ machine: almost a reality
Machine flexibility today can be more important than pure production speed. The users must be able to handle various package formats materials and products on a single machine while reducing changeover and reconfiguration times.
This is why ELAU has developed what it calls ‘technology packages’ integrating modular automation hardware and software capable of considerably reducing time to market and life cycle costs for machinery. With a scalable hardware range of controls drives and HMI the machine builder is provided with system components to meet a complete range of needs.
The software is the heart of the system. ELAU’s approach provides standardized software modules for the most basic functions keeping the machine builder from ‘reinventing the wheel’ and instead concentrating on value-added and customized capabilities. Machine development can not only be more rapid – software is more consistent from project to project.
Software quality is inherent
This use of off-the-shelf modular software components offers several advantages in software quality over programming from scratch.
For packagers in the regulated industries reusable and pre-tested software modules simplify FDA validation. Using the same modules from machine to machine reduces the learning curve for maintenance technicians and protects the user’s capital investment.
Having automated over 25 packaging machines worldwide ELAU has the packaging experience to understand and optimize the software building blocks for packaging. The company’s Interpack introductions include technology packages for case packing cartoning pick & place sealing and labeling.
The robotic technology package provides welcome commonality for users regardless of whether the mechanical design is articulated arm gantry delta SCARA or portal. This allows Cavanna’s customers to be confident that the robotic island’s unique functionality is built from industry standard software modules that will have a familiar look and feel when they appear on a palletizing robot for example.
Running robots and machines
The robotic management module is readily integrated in the machine’s application software thanks to ELAU’s structured development framework. Once the kinematic mechanism is selected the robot is parameterized and can be synchronize with conveyor belts or other external “master” axes. All the sophisticated kinematic algorithms are automatically calculated within the robotic software module.
A different kinematic profile is used for a delta robot than a Cartesian coordinate robot. For ELAU customers it’s a simple matter of replacing the robotic module without modifying the general machine software.
The robotic management module includes intelligent control of acceleration on the tool center point (TCP) to keep the centrifugal force under the limitations of the gripper’s ability to hold the product. The maximum allowable speed of each robot axis is automatically calculated so that TCP acceleration is not exceeded.
After a stoppage the robot’s motion remains synchronized so that when restarted it can pick up where it left off. Therefore even in the event of a breakdown or e-stop packaging line downtime is minimized. Diagnostic information is also logged and readily available if needed.
The integration of robots into packaging systems is increasing. The modular approach embraced by Cavanna and enabled by ELAU gives packagers greater access to robotic capabilities without the limitations imposed by third party robot suppliers.
For more information on Cartesio visit www.cavanna.com or email [email protected].
For more information on ELAU visit www.elau.com or email [email protected].