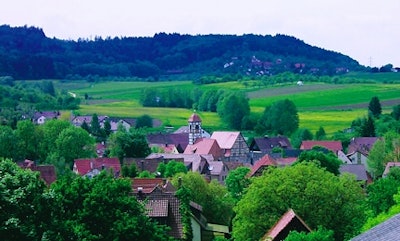
Facing business challenges with innovation
We’re driving through a pastoral setting in the south of Germany nestled in forested hills favored by outdoor sports enthusiasts. Into the village we turn right at the church. It is a most unusual location for a factory complex. But the juxtaposition is most fitting for this innovative enterprise named after its equally innovative founder Harro Höfliger.
This is a company that has survived and thrived by constantly adapting to the marketplace through a combination of skill and the sheer will to turn on a dime…or a pfennig if you prefer.
Fact: when economic and geopolitical changes resulting from the end of the Cold War threatened its very existence as a leading producer of standard packaging machinery the company turned its business model 180 degrees. It now produces some of the most specialized machines in the world.
Fact: while technology companies around the world have sacrificed engineering head count to please financial analysts this company has accelerated its investment in engineering. In fact 35% of the employees are MEs and EEs in the development center. And the region’s top tech students vie to be accepted in the company’s CNC apprenticeship program.
Fact: while the strategic advantages of modular machinery design are still often misunderstood this company interprets customer specifications intuitively integrating requirements into clever modules of functionality on three conceptual planes: control supply and production.
So this is the true meaning of ‘corporate culture’
You can think of this company Harro Höfliger as the world’s leading designer and manufacturer of wound dressing and transdermal medical patch machines. Which is true.
But the company has also become adept at the critical tasks of dosing everything from powders to gels of encapsulating 3-dimensional objects such as eyecups and pads onto a range of substrates and integrating assembly testing and packaging systems into production machinery for everything from parenterals to inhalers to complete drug delivery kits.
And since the 1980’s the company has held core competencies in pouching cartoning turnkey lines and blister forming fundamentals the latter of which has very nearly disappeared from the domestic US supplier base.
This company did not originally set out to be in pharmaceutical packaging or converting or medical device manufacturing. It simply answered the call and excelled. And now medical patch technology is also yielding non-medical market opportunities such as the production of flexible lithium-ion batteries.
This culture of making things work perfectly was evident throughout our visit. It began with the restored steam engine in the immaculate lobby and the enthusiastic welcome of our host Markus Höfliger the engineer-turned-marketing director.
We discussed needle-less syringes and iontopheresis dosage systems that use an electrical current to ionize the medication. We learned that oral film strips are very humidity sensitive in manufacturing while production of diagnostic strips requires great flexibility.
It was fascinating to see video of these and many other applications. It was also heartening to hear Markus Höfliger refer to my company ELAU not as a supplier but as a vital development partner in the application of automation technology. This relationship stretching back a decade to the first continuous transdermal patch machines has contributed a modular approach to automation software which enables modular mechanical design.
The intrinsic value of modularity becomes evident
Modularity would be a recurring theme in our conversations because this culture of modular thinking translates to exceptional speed to market for specialized machines. Base module designs are adapted to the characteristics of new materials whether these be gel reservoir patches or batteries.
Using our servo technology Harro Höfliger engineers may integrate web infeed modules of 4 5 6 or more materials into a process. Product changes on the multifunctional machine may involve switching from infeed modules 1 2 and 4 to the materials coming from infeeds 1 5 and 6.
Servo-driven production units such as rotary die stations are programmable for a wide range of lengths and speeds. A flying knife for patches for example may need to accommodate cut-off lengths from 3 cm up to 50 cm. The combination of ELAU software and Harro Höfliger engineering allows this flexibility with minimal change parts mostly by setting new parameters at the HMI.
An eye on customer requirements another on the road ahead
This built-in flexibility is important to customers because they can maximize machinery utilization through frequent format changes only if low volume runs are cost efficient. It’s important to Harro Höfliger’s business model because it is faster and more productive to build specialized functions if you can start with standardized modular mechanical and software building blocks.
Although the company is obliged not to divulge customer specifics it is clear that Harro Höfliger supplies a Who’s Who of pharmaceutical contract packaging and consumer goods producers. Their customer base is around the world but with a concentration in the U.S. In part that is because there are many innovative companies in the U.S. funded by risk capital whose success depends on new products delivery systems and the machinery to produce these unique designs.
After a plant tour we talked shop over lunch with electrical & electronics division manager Volker Scheub. The dining room afforded a panoramic view of the village of Allmersbach and treetops extending to the horizon. From Volker we learned how a combination of the company’s reputation for challenging assignments and the quality of life in this charming valley attracted some of the areas’s best engineering talent.
Scheub the technologist spoke passionately of customer needs half a world away. He was encouraged by our positive experiences in the OMAC Plug-and-Pack Workgroup. He was excited about innovative leasing arrangements that include staffing and maintenance to meet U.S. business trends.
Our time in Almersbach was over much too soon. Over an espresso we made plans to meet again at Pack Expo and then we were soon back on the autobahn. At the speed we were traveling it was important to concentrate on the road and not stare out the window pondering the speed at which this company called Harro Höfliger is changing the nature of Gen3 packaging machinery.