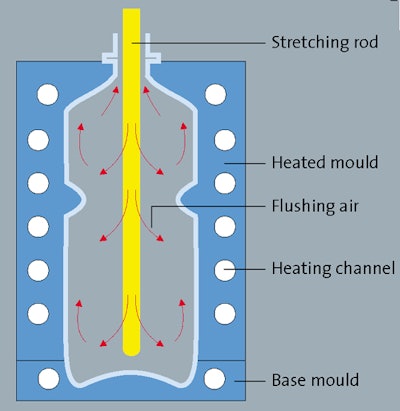
As a complete-system vendor for the PET packaging market Krones owed its customers a heatset technology capability e.g. for thermo-stable hot-fill PET bottles.
Even though more and more aseptic bottling lines are being encountered on the market hotfilling technology continues to be a highly regarded option.
This PET technology new as it was for Krones was made possible by the newly developed Contiform H stretch blow-molding machine.
The basics of heat-set technology
PET is a semi-crystalline thermoplastic which softens at approx. 76°C (what is called “glass transition”). Above this temperature the material becomes elastic and can be formed a property utilized effectively in the stretch blow-molding process.
Due to its glass transition at approx. 76°C PET is initially unsuitable as a bottle material for a hotfilling process above this temperature since deformations may occur: firstly the bottles shrink since they “remember” their previous shape (namely the preform) and secondly they collapse under internal pressure a typical phenomenon during the cool-down period after hot filling.
For this reason the hot-fill PET bottles feature what are called vacuum panels) which compensate for the underpressure produced during the cooldown period without the bottle collapsing. (Ill. 2 shows some examples for typical bottle designs.)
During the stretching part of the production process for PET bottles the material crystallises. We speak here of stretch-induced crystallisation. In the standard process the material is frozen in this state at the mould wall which is chilled. Inner stresses are then retained and lead to reshrinking particularly at heat-up. If however the material is heated still further after being stretched it undergoes aftercrystallisation (known as thermally induced crystallisation). The stresses in the material are also decreased thus reducing the tendency towards reshrinking. The increased crystallinity gives the material significantly enhanced thermal stability. The glass transition temperature and the rigidity increase. This process is referred to as “heat-setting.”
Producing hot-fill PET bottles on the Contiform H
This improvement in PET’s properties thanks to aftercrystallisation is utilised on the Contiform H in order to produce hot-fill PET bottles. The performs are here in contrast to the standard stretch blowmolding process not blown into a cold mould but into one heated up to as much as 160°C.
To enable the bottles thus obtained to be removed from the hot moulds however they have to be cooled. For this purpose compressed air is blown through bores in the tubular-shaped stretching rod which cools the bottle from the inside (known as a flushing-air process). Ill. 1 depicts this in diagrammatic form. These additional steps in the process (crystallisation and cooling) mean that significantly more time is needed in the blowmolding station under the heat-set process as can be seen from the chart in Ill. 2.
Differences between the standard and heat-set processes
The altered process engineering involved compared to the standard process entails some important differences in the machinery design and output required:
1. Since more process time is required the output per cavity and hour is significantly lower (800-1 bph compared to more than 1 bph on the standard model).
2. The heating time for the preforms is longer since hot-fill PET bottles are always manufactured from heavy preforms so as to obtain increased stability. See Ill. 3 for typical bottle weights.
3. An appropriate media manifold is installed for heating the moulds. (heat transfer oils at temperatures of up to 180°C).
4. Theoretical pressure curve during the heatset process.
5. Additional valves control the flushing air. The stretching rod moreover is hollow and provided with bores patterned to suit the particular bottle involved.
Bottle performance and machine output
In the heat-set process the bottle’s characteristics depend even more closely on the process settings and the choice of preform than is the case in the standard process. In particular the temperature of the product during filling and the time during which this temperature has to be maintained are crucial factors. The higher the thermal stress the higher the degree of crystallinity required. In order to obtain a very high degree of crystallinity a long crystallisation time in the blowing mold is needed. Consequently the more crystallinity is required the lower the station’s output will be.
With the new Contiform H and its associated heat-set technology Krones has lost no time in responsively expanding its product range in the field of PET stretch blow-molding.