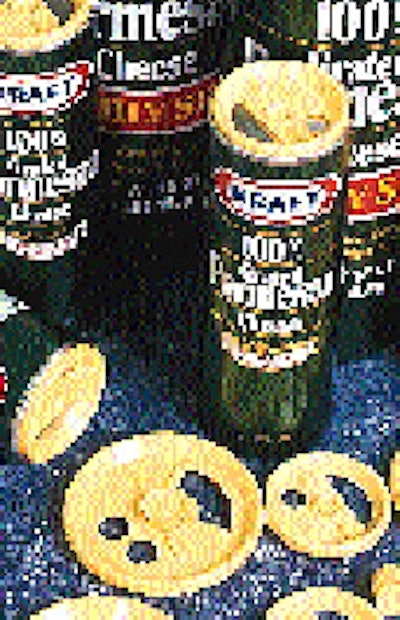
To reach the product, consumers positioned the rotor so that the breakaway opening in the aluminum was in view. Thumb pressure on the breakaway opening did the rest. Tamper evidence rested in an examination of the aluminum: If the breakaway opening was anything less than seamless, or if some other hole in the aluminum could be detected, it could be construed as evidence of tampering. The weak link in this arrangement was the rotor's center post, which protruded through the aluminum. There was nothing keeping a would-be tamperer from popping off the plastic rotor to expose the center hole in the aluminum and then returning the rotor to the canister. The new HDPE rotor--developed by Kraft's composite can and closure supplier, Specialty Packaging Group (Wausau, WI) and injection-molder CAPS, Inc. (Bridgeton, MO)--still rides atop the aluminum end. But the center post has been redesigned to remain permanently lodged in the aluminum end if someone removes the rotor. While plastic-to-plastic rotor closures already have this feature, this is believed to be the first such design for an aluminum-to-plastic closure. By retaining the aluminum/HDPE closure instead of switching to plastic/plastic, Kraft keeps the package's signature look while continuing to enjoy the economies of the high-speed seaming process that Specialty Packaging uses to adhere the aluminum end to the composite canister prior to rotor application. The new rotors were in national distribution by the end of '95.