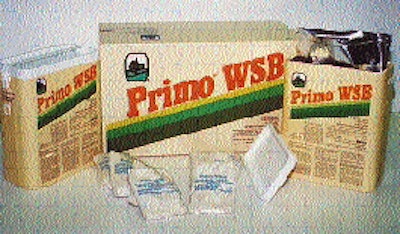
Secondary and tertiary packaging of the firm's Primo brand product contribute as well, bringing functionality, child resistance, moisture barrier, ease of use, and just plain good looks to the total package mix, in use since the first quarter of this year. Tim Cotter, packaging specialist at Ciba-Geigy, says competitive products are sold only in a liquid format. The key to Primo's pouch approach is that it practically eliminates any chance of workers being exposed to the chemicals. "With our dry formulation, there's no pouring or splashing or glugging," says Cotter. "Just take the pouch and toss it into the mixing tank." The 40-micron (1.57-mil) pouch material is supplied by Mitsui Plastics (White Plains, NY). Contract packager PM Resources (St. Louis, MO) produces the 4-oz pouches on a vertical form/fill/seal system and then inserts 16 of them into a zippered bag from LPS Industries (Newark, NJ). The bag lamination is a three-layer extrusion lamination of 48-ga polyester/low-density polyethylene/0.0003" foil/LDPE/1.5-mil linear LDPE. Equally innovative is the paperboard drum in which the pouches are packed. Supplied by Dorpak (Cincinnati, OH), it's made of 100% recycled paperboard on special "multiforming" equipment developed by Dorpak (see PW, October '94, p. 24). Ciba-Geigy chose it partly because management viewed it as an environmentally responsible alternative to plastic buckets. Graphics, printed offset in five colors, include all regulatory information required on the agricultural chemical product. The paperboard drum also incorporates a child-resistance feature that's new from Dorpak: a locking handle and lid injection molded of polypropylene. To remove the lid, the user depresses two tabs while pulling up on the strap. To close, the lid is replaced and the strap pulled down.