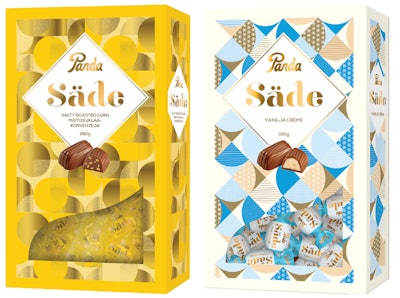
Founded in 1654 as a Norwegian mining company, Orkla is now one of the leading brand manufacturers in the Nordic and Baltic states, with product distribution in 100 countries and 114 factories around the world. The conglomerate has changed its focus over the decades and now operates in a range of Consumer Packaged Goods markets, including hygiene and personal care, baking, food, and confectionery. Around 15% of Orkla’s total operating income is generated by its Confectionery & Snacks business. Among its popular confectionery brands are Göteborgs Kex, Kalev, Laima, Nidar, and Panda.
It is at its plant in Vaajakoski, Finland, that Orkla produces its line of Panda chocolate products. Several years ago, the plant was experiencing challenges with the two packaging machines it was using to wrap its chocolate pralines. The machines had long since reached the limits of their performance and could no longer keep up with the high output of the chocolate molding line that fed them. The equipment was only able to wrap one third of the products coming off the production line. Two thirds were placed in temporary storage due to the lack of packaging capacity and were only transferred to the packaging process after production of the first batch was complete. Since 2015, Orkla had been in discussions with equipment supplier Theegarten-Pactec about acquiring new equipment; in 2018, it was time to make a move.
Initially, Orkla planned to replace its two lower-performing packaging machines with two of Theegarten-Pactec’s MCC wrapping machines for molded chocolates. The MCC can handle double-twist and foil-wrap packs at 1,200 products/min. The machines would be able to accommodate the entire output of Orkla’s molding line, thus the confectioner would no longer require intermediate storage, and delayed packing would become a thing of the past. However, a lucky coincidence—and a leap of faith on Orkla’s part—resulted in a change of plans.
Orkla becomes test site for new wrapper
Not long after Orkla made the decision to acquire the two MCC wrappers, Theegarten-Pactec told the company about its latest customized solution for the confectionery industry: the CHS packaging machine, designed specifically to handle chocolate products with various wrapping styles at speeds to 1,800 products/min. The machine had already been through intensive tests at Theegarten-Pactec’s Dresden, Germany, headquarters in a development process that lasted several years.
The modular CHS packaging machine, developed specifically to wrap chocolate products gently at high speeds, was installed and commissioned at Orkla’s Vaajokoski plant in early 2021.
Adds Daniel Schibur, head of sales at Theegarten-Pactec, “This was the perfect opportunity for us to test the CHS under real-life conditions in confectionery production. A continuous product flow, continuous operation, different packaging materials and product qualities, cleaning and maintenance work during operation or even difficulties such as process equipment downtimes—there are lots of things that cannot be simulated. Ultimately, tests like these are essential to put the finishing touch to a new development and get it ready for the market.”
![]() | Watch this video, “Innovations in Sustainable Packaging for Confectionery & Ice Cream.” |
Steffen Hamelmann, marketing/public relations at Theegarten-Pactec, explains the differences between the MCC and the CHS: “The MCC is also a high-performance packaging machine that can be converted to other types of packaging. To be honest, however, it must be said that certain combinations of packaging styles are excluded on the machine due to its design. In other words, when buying the machine, one must already consider which types of packaging might also run on the machine in a few years’ time. This is different with the CHS. Regardless of how the machine was originally configured at the time of delivery, further packaging styles can be easily retrofit later in any combination.”
In addition to the improvement in flexibility, the CHS also increases the maximum output rate of the machine by 600 products/min. According to Hamelmann, the CHS can reach 1,800 products/min, while at the same time gently handling the delicate chocolate products, using continuous motion. With other machines, the product is slowed down before each packaging step and then accelerated again. With each of these multiple acceleration and braking processes, the products are subjected to forces that limit the possible output per minute. “On the other hand, the continuous principle means that the products pass through the packaging process at almost the same speed,” he explains. “This means that there are almost no acceleration forces acting on the products, and a higher number of units can be packaged.”
Two-lane infeed assists in high-speed operation
The modular CHS was installed and commissioned at Orkla in early 2021. In addition to the general functional tests, the machine’s two-lane infeed—a unique feature of the CHS—was tested in depth. One of the main challenges was the separation of products from the continuous product flow on the main belt into the CHS’s two-lane infeed while ensuring a constant balance between the two lanes. Each of the two infeed lanes has to be supplied continuously with 900 products/min. In the wrapping process, both lanes are merged into a single-lane flow of 1,800 products/min.
According to Orkla Technical Manager Arto Liinatainen, the new MCC and CHS wrapping machines at the company’s Vaajokoski plant in have helped Orkla increase its packaging speeds.
After the products are fed into the machine on two lanes, a gripper head takes the chocolates from the infeed belt and transfers them to the packing head. During this step, the two-lane infeed process is converted into a single-lane packing process. Meanwhile, the machine unwinds the film rollstock, and pieces are cut from the roll and fed into the packaging process. In the next step, within the rotating packing head, the cut-to-size film wrap is fed to the product. The product is then wrapped with the packaging material, and the two ends are twisted in by the rotary grippers, creating the typical double twist wrap. Finally, the products are discharged from the machine via a chute or belt and transported automatically to the secondary packaging process to be loaded into cartons or pouches.
Machine adapts to market requirements
Although double-twist wrapping is currently the only packaging style being used to wrap chocolate products at Orkla in Vaajakoski, as Hamelmann explains, the CHS can be adjusted to handle a number of different packaging types, nine in fact: double twist, protected twist, top twist, side twist, foil wrap, bottom fold, side fold, Vienna fruit fold, and envelope fold. The machine allows the fold type and format to be changed in four hours, with most of these changes requiring only one person. Also, as Hamelmann shares, the machine can be easily retrofit to handle new package types, regardless of how the CHS was originally configured at the time of delivery.
Since customers have to respond quickly to new market requirements, such as resized chocolate products, Theegarten-Pactec has also increased the range of product sizes that the CHS can handle. Whereas existing machines could wrap products 16 to 45 mm long, the new system offers a range of lengths between 16 and 60 mm. The company has also made adjustments to the width; previously it was 12 to 25 mm, now it’s 12 to 35 mm.
According to Liimatainen, Orkla is very happy with its new wrapping equipment. “The packaging machines have given us outstanding results all along the line,” he says. “We’ve finally been able to increase our packaging capacities. It was this that prompted us to purchase the whole packaging system, comprising the CHS, the MCC, and the feeding system, in October 2021.”