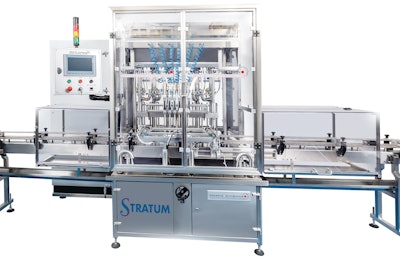
Yellowbird Foods has experienced rapid growth since it debuted at a local farmers’ market in 2013. Its rise to the top came as management built a reputation for quality, from their meticulous production methods to every flavorful ounce of the final product.
The Austin, Tex.-based sauce maker’s products are famous because they’re packed with fresh fruits and vegetables to create sauces that are smoother but also more viscous than standard sauces. The firm also prides itself on consistency of flavor, meaning every PET bottle of sauce packs a punch with signature bold and spicy flavours. All of which has made Yellowbird Foods a top 10 sauce supplier on Amazon as well as a seller through more conventional retail channels. The liquid filling system capably handles a wide range of product viscosities.
The dramatic increase in demand for Yellowbird Foods’ product recently necessitated an upgrade from the semi-automatic dual-head filler that the firm had in place. But with such meticulous standards in product quality, sourcing equipment capable of achieving production consistency at high throughput would be no easy task.
Eventually, the search led Yellowbird Foods’ COO Kevin Uplinger to equipment made by Shemesh Automation. The independent consulting firm Cougar Packaging played a key role in equipment selection. “I’ve worked with them for a number of years now, and they were the ones who got me going over to Israel and seeing some of the equipment made there,” says Uplinger. “In the case of Shemesh, the quality is impressive, and the cost makes them an even more attractive option.”
With more than 30 years’ experience delivering high-end turnkey packaging lines to manufacturers all over the world, Shemesh was able to deliver a sauce filling, capping, and labelling solution that offered Yellowbird Foods an enhanced throughput of up to 100 containers/min while also ensuring the highest standards in product consistency, hygiene, and efficiency.
Related content: OEMs Can Monetize Predictive Maintenance
The line includes Shemesh’s flagship equipment: STRATUM II and THORO II. The STRATUM II is an advanced in-line automatic filling system featuring servo-driven pistons and servo-driven diving nozzles that, coupled with special software features, allows a synchronized filling profile that reduces foaming and splashing in filling a variety of product viscosities. And the THORO II, a robust servo-driven double-station capper, is specifically designed to provide accurate, leak-free capping. The two machines were just what Yellowbird management was looking for.
The capacity and speed of each unit makes it possible to handle each product variety with minimal downtime between runs. By obviating the need for multiple production lines, Yellowbird Foods was able to avoid costly capital outlays. In addition, the equipment has a modest footprint This machine applies a wraparound, pressure-sensitive, paper-plus-matte finish label.
Three bottle sizes
Yellowbird Foods fills 2-, 8-, and 16-oz PET Boston Rounds on the new line. As new equipment was explored, says Uplinger, throughput was a key priority. “I needed at least 60 bottles per minute, and Shemesh definitely delivered,” says Uplinger. “We’re running our smallest size at 100, our medium at 80, and our largest at 60.”
Bottles are manually removed from corrugated shippers and placed on an infeed table leading to the filler. The STRATUM in-line filler has six nozzles, though Uplinger says it can easily be upgraded to 10. When asked if he considered a rotary, as opposed to in-line, filling system, he answers in the affirmative. But the nature of the product made in-line a better option. “I know rotary fillers tend to be faster, but a lot of them are gravity-fed,” he says. “Our product can’t be gravity-fed, it’s got to be a heavy piston-fill because of the viscosity.” As for filling accuracy, Shemesh pegs it at plus or minus 0.25% liquid volume.
A short distance down from the filler sits the double-station intermittent-motion capper. As bottles exit the filler, a swing gate moves back and forth to divert bottles into two lanes. Each lane leads directly into a large star wheel that captures bottles two at a time and brings them beneath a chute filled with “witch-hat “style dispensing caps that are injection-molded of polypropylene. Each time the star wheel advances, two caps get seated on two bottles and the two bottles ahead of them have their caps torqued down. In one final station, two analog sensors measure the height of each cap. If anything is outside of a predetermined spec, that bottle is rejected.
One other feature of the capper that Uplinger notes is that the caps are sorted and oriented on a disc sorter designed especially for this particular witch-hat cap. “With a vibrating sorter, which is more commonly seen in our industry, you barely hit them and they’re out of whack,” says Uplinger. “Then it could take you days to get them back into the right vibration.”The impressive range of flavors offered.
An ink-jet coder from Domino puts lot and date code information on the shoulder of each bottle. Then comes an induction sealing system from Enercon. At this point bottles are ready for a wraparound, pressure-sensitive, paper-plus-matte finish label that is applied by a Shemesh LWA Series Labeler. Shemesh has for some time used labelling heads made by Herma, and as of this year it has been integrating the new H-500 model. “It’s the most advanced servo-driven label applicator out there,” says Bob Green, Sales Director North America at Shemesh Automation.
Case packing currently is done manually, and the cases are taped closed. But Uplinger says that end-of-line automation is now being looked at, especially since the cost of end-of-line robotics is coming down the way it has been. “A robotic case packer I specified for a previous manufacturer back in 2013 was like $2.1 million,” he notes. “Today you can get something comparable for $60,000.”
An important decision
According to Uplinger, “Our significant growth in recent years made it essential for us to increase our production capabilities in order to address the demand for our sauces. Selecting the manufacturer for such a line is one of the most important decisions you can make. Of course, enhanced production capacity is important, but even more so is the integrity of our product. Ensuring that our selected manufacturer understood the importance of maintaining the quality of our sauces throughout the packaging process was absolutely paramount.
PACK EXPO Las Vegas and Healthcare Packaging EXPO (Sept. 27-29, Las Vegas Convention Center) will reunite the packaging and processing community, offering new products, technologies and solutions, while implementing up-to-date protocols for a safe and successful in-person event. Attendee registration opens in May.
“The experience Shemesh has demonstrated during their 30 years of serving premium food brands played a big role in our decision to work with them on the project. I’m delighted to say that we made the right choice, as Shemesh has delivered on all fronts. From the efficiency of the process to the quality of the final product, we couldn’t be happier. I wouldn’t hesitate to recommend Shemesh to any other manufacturer who wants to increase their production capacity without compromising on product quality.” This double-station capper is specifically designed to provide accurate, leak-free capping.
Shemesh’s Green says Yellowbird Foods and Shemesh have a number of things in common, “from experiencing rapid growth in a relatively short space of time to our mutual determination to never compromise on quality. I believe these shared experiences and values, together with our depth of experience in providing such high-quality machinery to some of the world’s biggest names, has helped to make this partnership the success it has been. I’m incredibly proud to see the impact Shemesh machines are already having at Yellowbird Foods—helping them to meet the demand for their amazing product while also reducing waste, utility consumption, and changeover time within an ergonomic production center footprint.”
As for the rapid growth of Yellowbird Foods that Green mentions, Uplinger puts it all in perspective. “Four years ago we were making product in 40-gallon kettles. Now we run 750-gallon kettles all day long.”