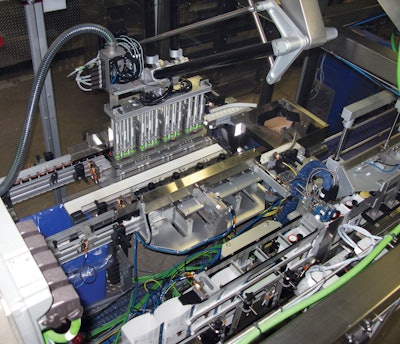
Launched in Brooklyn in 1934, coffee roaster Barrie House Coffee & Tea now occupies a 90,000-sq ft plant in Elmsford, NY, about 27 miles north of New York City. The third and fourth generation members of the Goldstein family who now own and operate the firm are about as advanced as anyone on the planet when it comes to one particular aspect of their full-line coffee and tea business: filling, inspecting, date coding, cartoning, case packing, and palletizing of single-serve coffee capsules.
The lineup of automated machinery they’ve assembled is quite remarkable, which we’ll see in a minute. But equally impressive is the Barrie House coffee capsule itself, that little container of ground coffee that goes into a Keurig Machine to produce a single serving of coffee. Its supplier is considered proprietary for the time being. But it’s thermoformed from a coextrusion of PP/EVOH/PP. That makes it notably different from the polystyrene K-Cup popularized by Keurig Green Mountain, which is the largest producer in the K-Cup category and, technically at least, the owner of the trademarked K-Cup® term. Keurig’s patent covering the design of K-Cups expired in 2012, at which point a number of others (Mother Parkers Coffee, Copper Moon, Treehouse Foods) began making single-serve coffee capsules that are compatible with either the Keurig-branded brewing machine or the Keurig-style brewing machines now made by the likes of Hamilton Beach, Faberware, and Proctor Silex.
Many marketers of single-serve coffee capsules today still rely on a cup that is thermoformed of polystyrene and includes a layer of EVOH for oxygen barrier purposes. A paper filter goes into the capsule to keep grounds from getting into one’s coffee cup. The third component, a foil lid, is heat sealed into the cup. In the brewing machine, one needle punctures the lid and another punctures the bottom of the cup. Hot water flows into the cup through the hole in the lid. Out through the bottom of the cup flows freshly brewed coffee.
The single-serve coffee capsule has been widely criticized because polystyrene is rarely if ever recycled. That’s why Green Mountain Keurig is in the middle of a transition out of polystyrene to an injection-molded PP/EVOH cup, a transition it hopes to have complete by 2020.
When Barrie House started thinking about getting into the coffee capsule business, which was as early as 2008, management made sustainable packaging a key objective from the get-go. Initially, biodegradable materials were explored. But according to Director of Sales and Marketing Shay Zohar, it was quickly determined that because commercial-scale composting is not widely available in the U.S., it made more sense to aim for recyclability than biodegradability.
Zohar goes on to say that the first fully recyclable capsule the firm developed was injection molded from a monolayer polypropylene. Included in the PP pellets from which the cup was molded was an oxygen scavenger to prolong shelf life. This format, which had to be designed in such a way that it would not infringe on the Keurig patent, made it successfully to the marketplace in late 2010. But Zohar and Barrie House CEO David Goldstein came to the conclusion that this injection-molded cup couldn’t be made efficiently in the kinds of volumes they had established as their goal. So back to the drawing board they went, and by 2013 the thermoformed coffee capsule currently in use began reaching the marketplace. One element of its predecessor that was retained is the pull tab on the foil lid that lets consumers easily remove lid from cup so that the foil can go into the aluminum waste stream while the PP goes into its own waste stream. More on the lids, which come from Israel and a firm named Tadbik Group, shortly.
Patented cup
According to Zohar, the coffee capsule now in use, which is patented by Barrie House, represents a dramatic improvement over the first one that Barrie House brought to market. Not only can it be thermoformed more efficiently and at higher throughput than its injection-molded predecessor, it weighs 2.6 g instead of 6.8. And the EVOH barrier layer keeps the coffee fresher than the oxygen absorber in the previous cup was able to. Shelf life is two years.
As successful as they were in developing a functional and recyclable capsule, Zohar and colleagues struggled mightily when it came to automated primary and secondary packaging equipment. The situation was so bad that it soon became clear that the firm had two choices. Either walk away from the single-serve coffee capsule market or double down and make a serious investment in all new equipment. “We decided as a company to double down,” says Zohar.
Through Tadbik, the Israel-based supplier of foil lids, Zohar was introduced to another Israeli firm named Pack Line Ltd., and in short order Pack Line’s PXM-6 filling and sealing machine was selected as the one that would meet Barrie House’s requirements. Nuspark, a Canadian OEM that had previous experience with capsule packaging on other installations, became the provider of the specialized secondary and tertiary packaging systems needed at Barrie House. A third key machine supplier that provided the all-important auger fillers integrated into the Pack Line system was All-Fill Inc.
“All of these guys were amazing,” says Zohar. “We were able to build the first line in less than five months, which is unheard of when you’re talking about a complete production line and much of it is custom. Don’t forget, too, that our unique capsule is not an easy one to handle. It takes a very deep filter, and we’re putting 18 g of coffee into it while most of the industry is averaging 10 g and maxing out at 12 g.”
By July of 2013 Line One was humming. But rather than resting on their laurels, says Zohar, “We decided to build another line that would be even better. By August of 2014, it was done, and as soon as we saw it in operation we immediately ordered two more just like it. The technology we’re taking advantage of now compared to Line One is like night and day, which is partly why we now run at 300 capsules per minute rather than the 240 that Line One topped out at. In fact, Line One is now shut down as we upgrade it with the advancements we developed after it got its start.”
Zohar once again emphasizes how essential it was that his firm was willing to view key machine suppliers as partners in a collaborative process. “We’ve given them 100% access to all the cameras in the production areas. They have full access into software, they see our workflow, our work volume, our efficiency, our alarms. Everything we have is fed live to them. By our sharing information this way they can really understand what’s happening on their machines. Only by seeing it in real time can they have this kind of deep understanding. It’s an approach that allowed all of us to do amazing things.”
A big part of the real-time visibility he speaks of is delivered by an industrial M2M router and data gateway from eWon called Flexy. All connections run through industry standard VPN protocols to guarantee a safe and secure connection that prevents network intrusions. OPC UA technology offers interoperability between platforms from multiple vendors and enables new machines as well as legacy PLCs for IoT integration. “We share and collect all data in and out of the production line via the eWON hardware with custom software written by Pack Line’s chief engineer and software genius, Eyal Dafna,” says Zohar.
Line Four
Of the three lines in operation on the day of our plant visit, we chose to focus on Line Four, which was producing 24-count cartons that were being case-packed four cartons per case. Immediately noticeable is the innovative method of feeding empty capsules into the Pack Line PXM-6. An operator removes a slug of 100 cups from the corrugated case in which they arrive and places it in a flighted incline conveyor. Up at the top of the machine, the slugs drop from the incline conveyor into a second flighted conveyor, this one being horizontally oriented. Its six flights position the six slugs in front of six capsule magazines from which capsules are denested and placed into the six-across filling machine. When these magazines require fresh slugs of capsules, the horizontal flighted conveyor holding the six fresh slugs pivots to a vertical position so that the slugs drop neatly into the six magazines. Then the cycle repeats itself. According to Zohar, an operator can fill this denesting system with enough capsules to last about an hour and 12 minutes before he needs to replenish it again.
Meanwhile, at the bottom of the six capsule magazines, capsules are picked by vacuum cups mounted on tooling driven by a Unidrive M700 servo motor from Emerson’s Control Techniques. The capsules are drawn down into the six-across pockets of the carrier mechanism that takes them through a number of operations. With each stroke of the servo-driven picking device, mechanical fingers separate the bottom cup to be picked from the nested ones above it so as to simplify the task of cleanly picking it and placing it into its assigned pocket.
Next comes insertion of filter paper, but first is a station where six Model GV-H45 laser inspection systems from Keyence make sure that each pocket in the carrier mechanism has a capsule in it. If a capsule is missing, or if a misshapen capsule or two capsules at once are detected, that pocket will be “remembered” during the rest of the process so that no filter paper is inserted, no coffee is deposited, and no foil lid is placed.
As for the filter paper, it’s drawn from a roll over a series of dancer bars that help keep the right tension. It’s cut into six circles so the circles can be pleated and pushed down into the capsules, again by way of tooling driven by a servo motor from Control Techniques. The filter paper is heat sealed to the top of the interior sidewall of each capsule, and then a second series of Keyence GV-H45 laser inspection units check to make sure the filter paper is properly inserted. If the filter paper is missing or misshapen in any way, that cup gets no coffee and no foil lid and is targeted for automatic rejection.
Moving forward, each cup has nitrogen gas injected into it to displace residual oxygen, the mortal enemy of fresh ground coffee. Also, from this point until after the foil lid is applied, the enclosed environment through which the cups travel is flooded with a laminar flow of nitrogen.
Liquid flavorings
Now comes a station where liquid flavorings can be added. Adding flavorings is a common enough practice in the K-Cup sector, but typically it’s done by adding the flavoring directly into the ground coffee while it’s still in a bulk state, that is, before it is deposited into the capsule. Inherent in this approach is a certain amount of downtime spent cleaning out whatever vessel or hopper it’s mixed in to prevent cross-contamination of flavors. At Barrie House, the flavoring doesn’t go into the bulk coffee. Instead, Pack Line integrated peristaltic pumps to inject the liquid flavoring directly into the capsules just before coffee is deposited. “We can inject all the capsules with the same flavor six across or we can do six different flavors at a time, resulting in a variety pack. Once we’re done, we don’t have to clean out a bulk hopper to eliminate one flavor before going to a new flavor. We just flush out the flavor that’s finished and go to the next one. This gives us a phenomenal ability to change things on a dime. If we need to change a flavor, all we do is replace a jug of flavoring and select the purge function on the depositing system so there is no chance of cross-contamination of flavorings.”
As the flavor is being injected, another six Keyence sensors—this time it’s the Model VU-A10 fiber optic sensors—measure the amount of flavor going into each capsule. If anything is outside of pre-set tolerances, that capsule is marked for rejection. “The Keyence system reads the quantity of flavoring and displays it right on the HMI screen,” says Zohar. “If multiple injections in a row are flagged as inaccurate, the machine shuts down automatically and an alarm signals us that something needs to be addressed.”
Now the capsules are ready to be volumetrically filled with coffee, a task performed by an All-Fill Multi-Fill system that Pack Line integrated into the PXM-6. It uses six individually controlled servo-driven augers, a common product hopper, and one control system to separately control product infeed to the center of the common product hopper that disperses to each of the six fill positions. The servo motors and drives are from Kollmorgen, while the controller is an Allen Bradley Compact Logic L32E PLC from Rockwell. Typically with a stand-alone auger filler, the product hopper is conical in shape, and in the hopper is an agitator blade that constantly rotates in the opposite direction of the auger screw. This keeps the product from compacting, thus improving product flow to the flights of the auger. When Line One at Barrie House went into production, a fairly typical product agitator component was part of the picture.
But on the Pack Line system at Barrie House, because the capsules are on such close centers and because the common hopper from which all six augers are fed is not conical in shape, Zohar and All-Fill felt there had to be a better way to agitate the product so that filling accuracies could be optimized. “Every time we fed the hopper from the bulk coffee feed, we were changing the dynamics inside that hopper in terms of how much weight and pressure was pushing down on the auger screws,” says Zohar. “As a result, fill weights varied more than we wanted, depending on how much coffee was in the hopper.”
So the team removed the agitator blade and added a vibratory pan infeed system that completely eliminates the need for agitation. Coffee moves from a bulk feeder to the vibratory pre-hopper to the Multi-Fill’s common hopper to the six augers to the six funnels and finally to the six capsules. The coffee hardly spends any time at all in the Multi-Fill’s hopper. Also, the amount of coffee inside this hopper—and consequently the amount of weight and pressure pushing down on the auger screws—is far more constant. The result? Barrie House went from an accuracy of plus or minus 1.0 g to plus or minus 0.06 g.
“We owe the All-Fill guys for this,” says Zohar. “They went out on a limb and built something entirely new for us. The result has been phenomenal.”
Weigh cell
Immediately after the coffee has been deposited, each of the six capsules passes over a high-precision weigh cell from Wipotec so that any capsule outside a predetermined weight range can be identified for automatic rejection. The weigh cells, integrated into the overall system by Pack Line, also deliver constant feedback to the Multi-Fill’s Rockwell PLC so that trends in the weights of the filled containers can be closely monitored. If, for example, an upward trend in container weights is detected, the PLC will automatically signal an auger screw to modify its revolution so that less product is delivered, thus correcting the upward trend.
Lidding is next, but first the filled capsules pass through a vacuum station that removes from the capsule flanges any coffee that might interfere with the heat seal of lid to capsule. As soon as this is complete, the capsules receive a pre-cut lid from a pick-and-place unit whose Piab suction cups include a self-cleaning feature.
“The lidding station is phenomenal,” says Zohar. “It’s servo driven and nonstop because of how we designed the magazines that hold the pre-cut foil lids.”
To understand what Zohar is describing, see Photo 1, where an operator is shown inserting six stacks of lids. As he does so, there’s no need to halt production because the six lid magazines on the Pack Line machine still have all the lids they need. The new stacks being inserted by the operator will drop out of the device he’s pushing in and replenish the six lid magazines. He then pulls the device back out of the machine, reloads the modular lid holders shown in the photo inset, and mounts the modular lid holders on the device so that he can once again replenish the six lid magazines on the Pack Line machine. On the lid magazines are laser sensors from SICK that alert operators when the supply of lids is getting low.
As for the lids, they originate at Amcor in Germany and come to Barrie House by way of Tadbik in Israel. Amcor coextrusion coats aluminum sheets with an A/B/C/D/E sealant layer designed to ensure bonding to the aluminum thanks to the A layer and bonding to the PP capsule flange thanks to the E layer. The middle layers—in addition to the pull tab--are what make it easy for the consumer to remove the foil lid and put it into the foil recycle stream while putting the PP capsule in its own recycle stream. The Barrie House mantra, so to speak, which is articulated on some of its cartons, is “Cool. Peel. Recycle.”
Tadbik’s contribution is as converter. It prints the lids flexographically and die cuts them from the aluminum sheets. Tadbik worked closely with Amcor to develop the coextruded sealant layer and to identify just the right aluminum for this application.
Shortly after lids are applied, the capsules pass beneath a pair of Videojet 7310 Fiber Laser Markers that mark lot and date code on the lids. Each Videojet marks three lids. Zohar says the Videojet units also help keep the cost of lids down because in some cases one universal lid can be used for multiple private label customers and then it can be differentiated according to customer by laser etching online rather than by ordering separate lids that are preprinted.
The Pack Line system comes to an end as finished capsules are discharged from their pockets six at a time and carried off at a right angle on a belt conveyor. Mounted on this conveyor is yet another Keyence inspection device, this time the LumiTrax™ image capture system, that checks every single capsule for six things: is seal integrity good; is there any foreign material between lid and capsule flange that might compromise seal integrity over time; is print color quality good; does the aluminum have any sharp edges that might harm consumers; is overall cleanliness satisfactory; is it the right lid per the work order generated by the NetSuite Enterprise Resource Planning (ERP) software.
“Here again is one of the amazing contributions made by Pack Line’s Eyal Dafna, who created all the programming and data base coordination for this image capture system,” says Zohar. “I believe it’s the first time the LumiTrax system has ever been deployed in such a manner.”
Speaking of the NetSuite ERP from Oracle, Zohar says it brings true recipe-driven manufacturing to the plant floor. “In the past an operator would have to go to the HMI of each major piece of packaging machinery and enter the work order information,” says Zohar. “Now our ERP system drives the whole business, from scheduling to production to inventory update and so on. We enter a work order and every piece of machinery gets its commands automatically from the ERP software.”
Before returning to hardware, one more bit of software magic should be mentioned, and once again it comes from Pack Line’s Eyal Dafna. Apparently, he developed a program that takes all of the alarm messaging—both audible alarms and those that show up on an HMI—and converts it to speech. So the operators, who wear wireless headphones, can hear over a Bluetooth connection such things as “Please remove a full pallet from Line Four” or “Fresh slugs of capsules need to be added in three minutes.” Says Zohar of programmer Dafna, “The guy is a genius. I’ve never seen anything like this.”
The next major piece of packaging equipment on the line is the Nuspark robotic cartoner. But Nuspark also integrated ahead of its cartoner a lengthy stretch of VarioFlow modular plastic chain conveyor from Bosch Rexroth that provides six minutes of accumulation time in case downstream equipment goes down. At the infeed of this line Nuspark has incorporated a capsule-cleaning system to eliminate coffee dust from the capsules to improve longevity of downstream devices, including vacuum systems. Knowing that the buildup of back pressure on this conveyor could damage the capsules, Nuspark included sensors and back-pressure control devices every four feet or so to detect for a backed-up condition and automatically bring the conveyor to a halt. To enable functionality of back-pressure control system, a top guide was installed along the entire length of the conveyor. It is designed to allow tool-less removal. Upon restart of the conveyor, the control devices release sections of product to optimize the reset process. The product is accumulated single file and in an upright orientation.
Two-lane infeed
Near the end of this conveyor stretch, a starwheel divides capsules into the two lanes that lead into the Nuspark Model NTP-30 cartoner, a machine whose starwheel and feed screws were provided by Kinsley. This machine also erects cartons from flat blanks and feeds them into a station where a robot uses vacuum cups to pick capsules and place them into cartons. Among the features Zohar especially appreciates when it comes to the cartoner is that changing between formats only requires the press of a button at the HMI and placement of the new carton blanks into the magazine. Carton formats include 8-, 10-, 12-, 14-, 16-, 18-, 20-, 22-, and 24-count. This machine is also capable of packaging bulk format in the range of 40- to 100-count, and changeover to this format is fully automated. Each capsule is counted. Regardless of how many capsules are going into a carton, the carton-forming mandrel stays the same. A key design feature of the forming funnel is the flexibility to accommodate variability and imperfections in the blank, utilizing a unique compression section with flexible material. What changes is the height of the carton, while width and depth remain constant.
Another clever feature is notable on the cartoner, which uses Nordson units for adhesive application to close four cartons at a time. On one lane there is a feedscrew that inverts capsules as they enter the station where the robot picks them. This permits the capsules to “nest,” so to speak, inside the carton, with one capsule right side up beside a cup that’s upside down. Consequently, carton sizes can be minimized. Only product about to be loaded is collated into the pack pattern, so the upsteam product is unaffected. This improves cycle time and greatly reduces waste.
Nuspark says the robotic pick and place component in the cartoner is fabricated by Codian and is coupled with a Schneider Electric controls package that combines logic and motion control for the servo motors on which this innovative machine relies. Nuspark also indicates that depending on customer preference, automation and control solutions from other controls vendors could also be used. The robot functionality includes final collation prior to loading with an end-of-arm tool that is capable of accommodating all pack counts and also incorporates an automatic reject and recovery sequence when necessary. The various pack counts are achieved in combination with the collation devices and four independent vacuum chambers on the robotic end-of-arm tool.
Once the cartons are loaded they proceed to a sealing station that is completely servo controlled with automatic changeover. Automated elements include glue positioning and adjustment for carton geometry.
One final observation from Zohar where the cartoner is concerned: “It’s running at 98% efficiency, which is pretty amazing for secondary packaging.”
Exiting the cartoner, cartons pass over an Alpha checkweigher from All-Fill. Any carton whose weight is outside of predetermined parameters is automatically rejected. Next is a Videojet laser printer that applies date and lot code to the top of each carton as it passes. Immediately following is a Videojet print-and-apply labeler that is used in special circumstances, like when a specific distribution center requires something out of the ordinary. All these devices are controlled by and integrated with the Nuspark Cartoner, with recipe control for laser printing and labeling.
Next in the line is Nuspark’s NRCP-5 Robotic Case Packer, which uses a Fanuc M10 robot to accomplish an impressive number of tasks. First, it picks a flat case blank from a vertical magazine and brings it into a station where its bottom flaps are glued closed. Then it transfers the open-top case to a station where cartons—in this instance four cartons—can be loaded. Then it swings over to where incoming cartons sit and picks them up. Finally, it puts cartons in cases and discharges the cases to a Nuspark unit that uses hot melt adhesive to close them. Then it repeats the same cycle. A unique element to this case packing system is its vertical case magazine, allowing for a space-saving layout. The magazine can hold more than 100 cases. The robotic cell layout allows for integration of additional magazines that can hold different size cases, which can be erected on demand.
Also worth noting where the case packer is concerned is that sometimes Barrie House bypasses cartons and simply bulk packs filled capsules into corrugated cases. The Nuspark case packer happily handles either format. This functionality is combined via recipe with the cartoner to enable bulk counting and packaging.
Cases come out of the top sealer, pass over an Alpha checkweigher, and then are conveyed past a Videojet 2300 Series high-resolution ink-jet case coder before moving into a Nuspark NRP-10 Palletizer that uses an R1000 Fanuc robot to place cases on pallets. Line Four shares this robotic palletizer with Line Three, and the robot services both lines simultaneously, palletizing cases as they arrive at their corresponding pallet stations. Pallets can be exchanged without stopping the upstream equipment or palletizer.
So there it is—four high-output coffee capsule lines each producing 300 capsule/min yet occupying just 10,000 sq ft. We haven’t seen the last of this plant, either. Just being removed from a truck as we finished our tour was a coffee bagging and tin-tie application system, again from Nuspark, that Zohar says will be like nothing else in the category. Stay tuned. Also see page 7 for more on Barrie House.