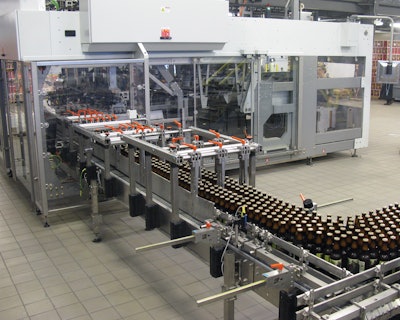
Launched in 1996 in Hammond, IN, and relocated four years later to its current location in nearby Munster, 3 Floyds Brewing grew steadily in its first decade. Great beer and word of mouth—combined with being located just 60 miles east of metropolitan Chicago and a population in the range of 7 million—fueled this early growth, so that by 2006 the firm was producing around 4,600 hectoliters annually. But right about that time was when the Internet came into its own. When sites like ratebeer.com and beeradvocate.com started singing the praises of 3 Floyds’ pale ales, wheat beers, and a Russian imperial ale that can only be bought on the last Saturday of April, sales really took off. In fact, the Munster brewery produced something like 60,000 hectoliters of beer in 2016, more than a 10-fold growth over 10 years.
In addition to a couple of seasonal beers here and there, 3 Floyds now produces six beers in 12-oz bottles and nine beers in 22-oz bottles. By 2012 it became pretty clear that the existing bottling line, which couldn’t exceed 70 bpm, was no longer able to keep pace with the brewery’s growth. So a new packaging hall was added to the existing space and into it went a turnkey line from Krones that has a rated speed of 250 bpm.
“Theoretically, this line would bottle 290,000 hectoliters a year in a three-shift mode,” says Head Brewer Chris Boggess. “So currently it’s overdimensioned. But we thought it important to look ahead a bit so we won’t have to install another line every few years, and in the meantime we’re using the best technology available.”
The turnkey Krones line begins with a Pressant Universal 1N bulk glass sweep-off depalletizer with low-level discharge onto a bulk-glass conveyor. The depalletizer is also equipped with a) vacuum cup pickup tooling that allows it to pick and stack the paperboard tier sheets that separate layers of glass and b) mechanical tooling for picking and stacking empty pallets.
A Krones Glideliner smoothly reduces the mass of bottles to a single-file lane of bottles that are conveyed into the rinser/filler/crowner block. Just ahead of this block the bottles pass a Domino ink-jet printer that puts a batch number and born-on date on the bottle shoulder.
The monoblock system consists of a 44-head Moduljet rinser using water as the rinsing medium and a Modufill filler with 44 filling valves. “The filler gives us excellent values for oxygen pick-up, in the range of 50 parts per billion, coupled with very consistent fill levels,” says Travis Fasano, Packaging Manager at the Brewery. The short-tube, level-controlled filler with vent tubes operates with double pre-evacuation and what Krones calls an “interpolated CO2-flushing feature”—i.e., between the two pre-evacuations there is a CO2 flush. The filling valves are electro-pneumatically controlled. A monoblocked turret receives bottles from the filler via a starwheel transfer. It sorts and applies the crowns and then releases bottles to a discharge conveyor.
Bottles are inspected for correct fill level by a Krones Checkmat FM-X, and immediately after that they enter a Krones Prontomatic cold glue labeler. Correct label placement is verified by a Checkmat E. Labels are supplied by Inland.
End-of-line packaging
At this point it’s time for the end-of-line packaging done on the Krones Varioline. According to Fasano, the conveyor connection between filler and labeler will hold about 1,000 bottles in accumulation. And between the labeler and the Varioline, the accumulation capacity is about 2,000. “So running as we are at about 250 bottles/min, we have about four minutes to address a jam before machines start to stop,” says Fasano.
The Varioline might be the most impressive machine in the plant. The components on a Varioline can vary considerably—which, of course, is how the machine got its name. It all depends on what the application calls for. But essentially each module consists of a steel base frame, a control cabinet, gantry robots to perform all the picking and placing, and servo-controlled cleated/flighted conveyors.
According to Krones’ Mark Forsberg, the Varioline is six machines in one: carrier erector, carrier stuffer, case erector, bottle inserter, partition inserter, case sealer. Because so many functions are executed within the frame of one machine, conveyor connections from one machine to another are eliminated. Consequently, 75% less floor space is required, says Forsberg. And efficiency, he says, is guaranteed at 97.5%.
Operating at 3 Floyds is a two-module system capable of almost 900 bottles/min when 24-count cases are being packed. Properly equipped, the system could handle 850 bottles/min.
Module 1 is responsible for erecting either four- or six-pack paperboard carriers, stuffing carriers into a corrugated case, and picking and placing bottles into that case. The other module erects corrugated shippers and closes them with hot melt adhesive. Just one operator is required, and the operator’s only real responsibility is feeding the magazines with paperboard carriers and corrugated cases. The paperboard carriers are from Graphic Packaging, while cases come from International Paper.
“It’s so much better than what we used to have, which was largely a manual operation,” says Fasano. “Right now we’re only doing 12- and 22-oz bottles, but it can handle cans, too.” Space for a Krones can filler was designed into the new line, so as soon as a bigger brewhouse is added, cans will be multipacked on the Varioline, too. They’ll be packed in a 12-count wraparound paperboard and then two 12-packs will be placed in a corrugated tray.
Case erecting in Module 2 is done in several steps. First vacuum cups mounted on an overhead gantry robot pick two flat case blanks from twin magazines; as the cases are pulled into a bottom sealing station, they’re both opened; once in the bottom-sealing station, the bottom minor flaps are hot melt glued by a Nordson unit.
A second gantry robot now uses its vacuum cups to grab the two cases by the folded and sealed minor flaps, lift them, and place them into a station where the major flaps are folded and glued. The same gantry robot then lifts the two cases, rotates them 45 degrees, and places them on a flighted conveyor that takes them off at a right angle in a direction we’ll call south so that they can have paperboard basket-style carriers inserted into them on nearby Module 1.
Meanwhile, on Module 1, vacuum cups on a gantry robot pick eight flat paperboard basket-style carriers from a magazine feed. The blanks are carried a short distance to a series of plates riddled with their own vaccum cups. So as the gantry robots retract in an upward motion, the bottom sides of the eight paperboard carriers are held securely by vacuum cups while the tops are held equally secure. As a result, the eight carriers are all popped open. Once they are open, the vacuum cups on the overhead gantry robot release and the plates holding the now erected carriers rotate 45 degrees so that the carrier handles all face upward. At this point, a second gantry robot mechanically picks all eight erected paperboard carriers and stuffs them into the corrugated cases that have been erected over on Module 2.
Once cases have their requisite number of paperboard basket-style carriers inside, they are pushed ahead into a flighted conveyor that runs in a direction we’ll call north—in other words, the direction opposite that in which they entered. Another gantry robot picks 24 bottles from the continuous-motion infeed conveyor and places them into the carrier-stuffed corrugated cases. The cases are then indexed in a northerly direction to a station where yet another overhead gantry robot comes down with tooling that closes the top flaps, both minor and major, with hot melt adhesive.
First of its kind
The Varioline at 3 Floyds represents the first commercial installation of the Pro Series, which simplifies case handling by replacing a system of reciprocating shuttle carts for movement of cases in favor of a flighted conveyor whose flights are each individually controlled by its own servo motor. In the past, if case size changed, the appropriate reciprocating shuttle cart had to be put in place and the old one removed. Now it’s just a matter of going to the touch screen controller and picking from a menu the case size involved. The servo motors automatically move the flights to where they need to be.
Like the servo motors that drive the many overhead gantry robots on the Varioline, the servos on the flighted conveyor are from SEW and the drives are from B&R, while the PLC is from Rockwell. Another supplier of automation technology playing a big role in the Varioline system is Festo, whose pneumatic valves, actuators, and vacuum technology is represented in abundance.
Another improvement in the Pro Series is that bottle infeed is now a smooth, continuous motion rather than intermittent. A drawback to most intermittent-motion infeeds is that as back pressure builds, bottle handling can be compromised.
What hasn’t changed in the Varioline is the feature that made it such a standout machine when it first appeared, namely its versatility. As was mentioned earlier, 3 Floyds will soon be multipacking cans on this machine. And already the machine is being used for the following:
• 12-oz bottles in two six-count paperboard carriers or four six-count paperboard carriers per case
• 12-oz bottles in four-count paperboard carriers that are case packed three carriers or six carriers per case
• 22-oz bottles separated by paperboard dividers in 12-count cases
The Varioline will also handle wraparound cases, though 3 Floyds doesn’t produce any currently.
One key to all of this versatility are the quick-change heads that can be easily removed from the end of an overhead gantry robot and mounted on a wheeled rack so that the quick-change head for the next container format can be mounted on the robot. Also helpful is that the magazines that hold paperboard carriers and corrugated cases are modular. To go from a 12- to a 24-bottle case, a forklift is used to lift the entire magazine module out of the Varioline and put the new one in place.
Things should get even more interesting at 3 Floyds once the canning equipment—also from Krones—enters the picture. “We’ll have to add some conveyor connections, and we also plan to automate palletizing,” says Boggess.
Also on the drawing board are a new kegging line, an expanded brew house, and a brand new distillery for whiskey and gin. Ambitious? Maybe so. But what else can be expected from a brewery whose motto has always been “It’s not normal.”