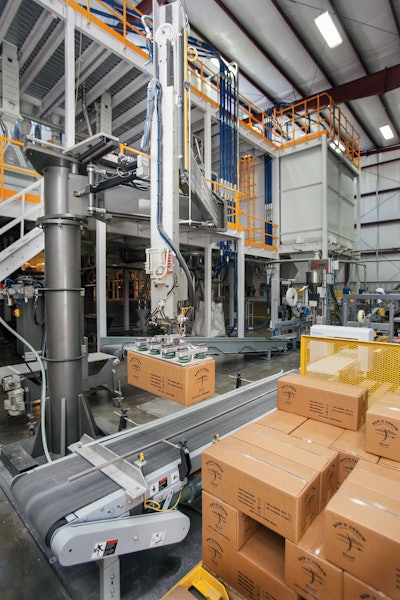
Simplicity, reliability, and value are packaging machinery characteristics that are universally appreciated. But they’re even more highly prized in remote locations like the one occupied by Ute Mountain Tribe Farm & Ranch Enterprise. This 7,700-acre agricultural enterprise nestled below the Sleeping Ute Mountain on Ute Tribe Land in the southwest corner of Colorado is tucked away—to say the least. This became an influential factor as the firm conducted its search for the packaging equipment it needed to launch its Bow & Arrow brand of corn meal. Product Development and Sales & Marketing Manager Mike Abeyta puts it this way.
“As I went to trade shows and conducted other forms of research, I was looking for simple, solid, reliable equipment that wouldn’t be excessively expensive. The simplicity factor was especially important because we’re located in a pretty remote part of the country, where you don’t want things going wrong if you can avoid it. Eventually I came to the conclusion that the Paxiom system was what I was looking for, and the fact that it all came from one source made it all the more appealing.”
Paxiom Group comprises packaging machinery manufacturers WeighPack Systems, Eagle Packaging, and CombiScale. WeighPack and Eagle figured prominently in the Ute Mountain installation, with WeighPack supplying the primary and Eagle the secondary packaging systems.
The product being packaged on the new line is corn meal in 24-oz, 1-lb, and 5-lb stand-up zippered pouches. Previously, Ute Mountain sold whole white corn kernels in 50-lb bags to taquerias and other small foodservice establishments that make tortillas. But with the introduction of Bow & Arrow brand corn meal, the firm enters the retail arena, an entirely new sales channel.
“We grow non-GMO food-grade corn and felt there would be a market for a line of corn meals and corn meal mixes—muffins, for example, or jalapeno corn bread—that played off the strength of our Native American underpinnings,” says Abeyta. “Especially in places like Whole Foods, which will likely be one of the first chains to carry the Bow & Arrow brand. Kroger and Walmart are also showing interest. I came on as a consultant to help get the Enterprise’s whole corn kernel business going. With this new product we’re adding more value to the corn and moving into retail sales.”
Screw conveyor
Product enters the packaging line by way of a WeighPack screw conveyor that draws corn meal from a floor-level hopper and brings it up to an overhead WeighPack Star Auger 200 filler. Product drops then into a WeighPack Swifty Bagger 1200. Designed with a heavy-duty sheet metal frame, its straight-flow design simplifies accessibility and cleanability. It’s designed to automatically open, fill, and seal pouches up to 12 in. wide x 18 inches long.
At the front end of this machine is a belt-feed mechanism that advances one pouch at a time from the pouch magazine and positions the pouch perfectly square. This allows the pick arm, which has two vacuum suction cups, to transfer it at a right angle into the opening station mounted on a reciprocating walking beam. Pouch opening is critical and is completed in a three-step process to ensure the highest performance. First the pouch is mechanically opened with a robust four-finger assembly. In the next step, a plunger with fiber optics is inserted into the bag to ensure the pouch has been opened to its full capability; also, air is blown in to help fully open the gusset. If it’s determined that the pouch has not been opened correctly, the pouch will not be filled or sealed, thus allowing for the pouch to be re-used. Once opened, the pouch travels via walking beam to the pouch filling station, where product is dispensed into the pouch. Next is the sealing station, where both a hot seal and a cold seal are applied. Finished pouches are then transferred to the discharge station.