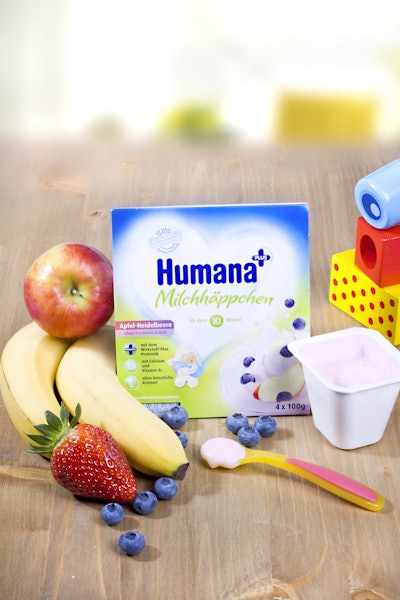
For 60 years, DMK Deutsches Milchkontor has developed and produced high-quality baby food and is a leading company in the German dairy sector. In 1950, DMK first introduced infant formula to the German market, similar to breast milk. The product portfolio has developed continuously since then, and today the company operates 12 manufacturing plants, which process a total of two billion kilograms of milk per year for a range of dairy products.
At DMK’s Erfurt plant, the company produces baby food, fresh milk, long-shelf life milk and fromage frais, as well as various desserts. In 2010, DMK began using a Bosch TFM 8030 PS aseptic thermoforming unit to DMK. This aseptic forming, filling, and sealing machine fills baby food into thermoformed cups. The machine allows product-friendly, energy-saving filling operations as part of an automated process.
As a result of its high hygiene level, and in conjunction with the upstream process technology, the TFM 8030 PS delivers product shelf lives of up to 12 months without refrigeration. Products filled with the unit include fruit yogurts and dairy-based desserts, as well as special baby food recipes.
High output and product safety
The TFM achieves output levels of 57,000 cups per hour, which amounts to a maximum daily production volume of 100 tons. The plastic cups are formed from reel material, which is much more cost-efficient in the production of baby food compared to prefabricated cups. A barrier of EVOH (ethylene vinyl alcohol) material is integrated within the film and protects the filled product against oxidation and water vapor diffusion, even over long storage periods and without refrigeration. The multilayer protective film also prevents mechanical damage to the product. Integrated gas flushing of the cup's headspace reduces the residual oxygen content, further increasing product safety.