Making chocolate candy faster
Adding a little automation to the mix makes a chocolate candy process machine happier while eliminating a very boring job.
Jun 16, 2010
Machinery Basics
Is your palletizing solution leaving money on the floor?
Discover which palletizing technology—robotic, conventional, or hybrid—will maximize your packaging line efficiency while minimizing long-term costs in this comprehensive analysis.
Read More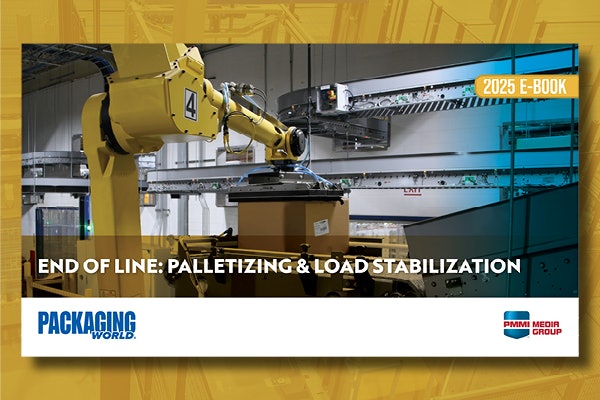
Coding, Marking, and Labeling Innovations Report
Explore our editor-curated report featuring cutting-edge coding, labeling, and RFID innovations from PACK EXPO 2024. Discover high-speed digital printing, sustainable label materials, automated labeling systems, and advanced traceability solutions that are transforming packaging operations across industries.
Access Report