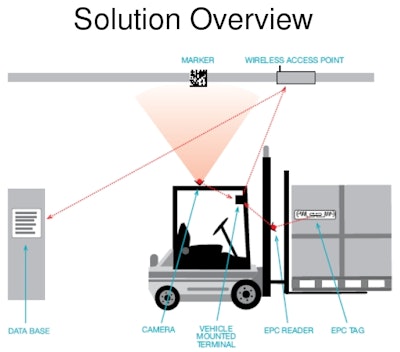
A unique and innovative RFID case study for pallets of kiwifruit was the final presentation at the EPC Connection gathering in October. For those who stayed, it was one of the highlights of the two-day event sponsored by RFID Journal magazine. The application involves RFID-tagged pallet loads of trayed kiwifruit and forklifts mounted with RFID readers as well as digital cameras. The upwards-pointed cameras read fixed 2-D bar codes from Sky-Trax Inc. (www.sky-trax.com) mounted in the ceilings of chilled warehouses, or coolstores. Applied in prefigured strips for ease of installation, the SkyMarkers provide precise real-time positioning—within 10 in. —when the forklift picks up or puts away an RFID-labeled pallet, according to presenter Erik Sundermann of GS1 New Zealand, and senior consultant for the project done for kiwifruit packer EastPack, Edgecumbe, NZ. Other vendors include RFID technology supplier Intermec (www.intermec.com). The project encompasses 6,600 stock-keeping units in 42 coolstores at three sites that can store about 600 pallets, yielding a throughput of eight million trays of Zespri brand kiwifruit yearly.
Penalties and rewards
Kiwifruit shipping orders are received 10 days in advance, but may be adjusted just two days in advance of shipment. Shipment penalties for the regulated industry are severe, up to $500 (all figures in NZ dollars) for wrong pallet on wrong truck at peak season. For example, four pallets switched on two trucks resulted in an eight-pallet fine in excess of $3000. Last season, before the RFID implementation, EastPack had such penalties of that totaled $280,000. EastPack can also earn up to $200 per pallet if flexible for impromptu shipments. The problems were finding specific pallets in the coolstores and eliminating supply chain mistakes, according to Sundemann. A bar code solution was found to be only 70% accurate.