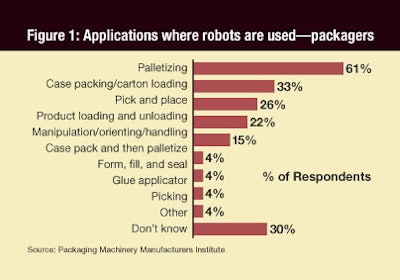
The use of robotics in packaging is picking up speed, nearly doubling from 9.5% to 17.4% in the last five years, according to a new study, “Robotics: Usage Trends and Packaging Applications 2008,” from the Packaging Machinery Manufacturers Institute (www.pmmi.org). The packaging functions for which robots are being used run the gamut (see Figure 1), but palletizing, case-packing/carton-loading, and pick-and-place applications are still the most prevalent.
The following five case histories detail robotic installations at food and beverage packaging plants, as well as at a prominent battery producer’s facility.
A new vision for case-packing candy
A robotic packaging line has replaced manual picking and packing for Italian confectionery company Zaini. An ABB Robotics (www.abb.com) FlexPicker® IRB 340 robot now handles and identifies a large variety of product formats and iterations, while its integrated vision system plays an important part in quality control.
Established in 1913, Zaini produces a large variety of chocolates, confectionery, sugar-free sweets, and seasonal items such as Christmas confectionery, Valentine hearts, and Easter eggs, at its two plants in Italy.
Says Amerigo Pallanti, factory manager for Zaini, “We sell to supermarkets and retail outlets such as [coffee] bars, and both are highly competitive markets.” In competitive markets, even a small cost or efficiency advantage can determine holding or winning share.
At Zaini’s Senago plant, a FlexPicker IRB 340 robot has been working since September to organize and case-pack a wide range of bagged confectionery and chocolates. The FlexPicker installation is equipped with an advanced machine-vision system. The system uses ABB’s PickMaster 5 software, which the company says allows the robot to “see” up to 130 different product variations and adjust its activity accordingly, with minimal supervision.
The FlexPicker came to Zaini at the recommendation of PRB Packaging Systems (www.prbpack.com), a supplier of end-of-line machinery and solutions. “Zaini’s engineers asked us to develop a system to handle a vast range of their products for packaging,” recalls Agostino Biagini, a partner at PRB. “The system had to be flexible, easy to operate, and easy to modify, since the products and boxes for shipping change very frequently. This made the assignment especially difficult.”
The system also had to be capable of dealing with products that, when they arrive at the case packer, are not always aligned on the production line but follow each other at a determined distance.
PRB’s solution was a combination of the FlexPicker and its own F-30 vertical case-packing machine. The biggest challenge of the project was to ensure that the robot could handle up to 40 formats and 130 different iterations. Zaini’s range of bags holds from 1.8 oz to 2.2 lb of chocolates or sweets, the bags’ contents have different sizes and shapes (for example small squares, round eggs, hard sweets), and there are different-sized packages for shipping and display, depending on the content and weight of the bags. In addition, the formats change every day.
As the prebagged items roll down the production line, a vision camera sees the format, and that data is used by the robot controller so the robot can pick and place items in the appropriate shipping cases.
The FlexPicker currently handles 1.8-oz packages at a rate of 90/min and 2.2-lb packages at 35/min, working two shifts (16 hr) a day, five days a week. “We expected a lot from this machine, and we got everything we expected,” concludes Pallanti.
Tray packing gets revved up at Energizer
Energizer Battery Manufacturing Co. needed to update a 15-year-old SCARA robot on an automated tray-packing system at its Asheboro, NC, facility. The system loads D-cell batteries into a variety of trays with several pack patterns. To update the system, Energizer required a single solution that would handle all of the required tray sizes. To minimize costs, they also requested that the existing components on their 95 Super Pack line, including equipment for battery delivery, orientation, and accumulation, be utilized in the design.
To address this challenge, engineers from ESS Technologies (www.esstechnologies.com) designed a complete system that robotically loads a variety of tray configurations with either eight or 12 D-cell batteries. The final TaskMate™ robotic solution devised by ESS integrates an M-6iB™ Series multiaxis robot from FANUC (www.fanucrobotics.com) and a custom end effector. ESS also reconfigured existing equipment to integrate with the new robotic system. “The system handles multiple stockkeeping units, increases production speeds, and maintains fast, tool-free changeovers,” says Energizer project engineer Joel Harden.
During tray packing, batteries are conveyed from an accumulation table to a single infeed lane. The upgraded system includes a servo-driven tray-indexing system, which divides the single lane into two lanes before entering the robotic cell. Preformed trays enter via the existing tray infeed conveyor. The batteries are reoriented for loading, and a vacuum-style end effector picks multiple batteries and places them in the tray in the correct number and orientation. Full trays require two or three picks for full loading; in some configurations, the new pick and place first picks and places a sensor card in the tray before loading batteries. Loaded trays exit on a conveyor to be shrink-wrapped downstream.
The program options for tray loading include:
• An eight-pack diamond pattern (two rows of three and one row of two);
• A 12-pack or eight-pack family pack (two rows of six or four batteries); or
• An eight-pack single row (one row of eight batteries).
Tool-free size changeover consists of moving a single rail on the infeed and selecting the new size on a Human-Machine Interface, which uses Ethernet connections between the HMI and the programmable logic controller. Discrete I/O allows the system to communicate with equipment downstream, and the HMI displays system faults.
Companies in this article