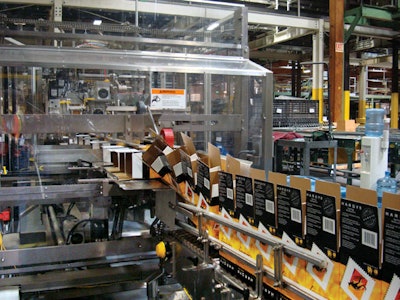
If imitation is the sincerest form of flattery, then Mission Bell Winery’s packaging equipment suppliers should consider themselves complimented. Last October, the Madera, CA, winery, which produces such well-known brands as Robert Mondavi, Paul Masson, Black Box, and Hardys, began running a new 3-L automated bag-in-box packaging line that was modeled after its existing 5-L BIB line.
“We tried to design the layout utilizing technology and manufacturers that we already had in-house,” relates Mission Bell director of bottling Dennis Hartman. “If technology had been upgraded, then we upgraded to that, trying to keep the same manufacturers. This allows us to share repair parts and hopefully minimize new training requirements.”
The result, he says, is a packaging line that, while standard for this type of package, includes a number of notable features designed to maximize line productivity, protect operators’ health and safety, and preserve product sterility.
The systems integrator for the line was Hartness Intl. (www.hartness.com), which Mission Bell selected to supply the line with two Dynac Model 6400 accumulators. “To ensure we maximized the Hartness Dynac accumulation centers, we chose Hartness to not only have control over their respective machine centers, but also over the entire line. They did a marvelous job, and our startup went rather well,” says Hartman.
Every machine on the line was equipped with Ethernet capability, which Hartman says “drastically” minimized installation costs. “Hartness was able to take this approach with ease and achieved outstanding results,” he says.
Other highlights of the line that Hartman cites are two Rapak (www.rapak.com) Autokap™ 1200E single-head, fully automatic fillers that ensure “near-zero” oxygen pickup, for a longer product shelf life; two Axiom® servo-driven carton erectors/sealers from Douglas Machine (www.douglas-machine.com) that Hartman says are virtually maintenance-free; a case packer and shrink wrapper from Packaging Machines Intl. (PMI, www.pmi-intl.com); and a top-loading HL4000 palletizer from Columbia Machine (www.palletizing.com).
An environment of change
Mission Bell is a monolith wine producer that in recent years has made major investments to increase the agility and productivity of its operations. The 110-year-old winery is a part of Constellation Wines U.S., the premium and fine wine division of Constellation Wines, the world’s largest wine business.
Mission Bell’s Madera winery covers 500 acres, employs 450 people, and operates eight packaging lines that output between 14 million and 15 million cases of wine each year. In 2005, the winery began either replacing or consolidating its then 13 bottling lines, spending many millions of dollars to upgrade to more automated and efficient equipment. “We realized that in order to be competitive, we had to bottle more wine in less time,” says Hartman.
When the project was finished, Mission Bell had four glass-bottling lines that together provide more than twice the capacity of its previous eight, one keg line, and two BIB lines for 5- and 18-L capacities.
Two years ago, the company brought in a 3-L BIB line that had automatic bag filling but little else. Operators were required to manually form and seal boxes, set up and pack cases, and hand-stack pallets. The process required 22 people, routinely performing repetitive physical tasks that “could lead to problems in the future,” recalls Hartman.
“As the product increased in volume, we realized that there was just too much manual labor. It was costing us too much,” Hartman says. “So we designed the new, 3-L line with an ergonomic layout that would allow us to man it with as few operators as possible, and with technology that would manufacture the product with little or no human involvement.”
The new line, which currently runs two 3-L carton configurations and a 5-L size, has reduced manpower requirements by 80 percent, Hartman says, and has increased productivity from 2,400 cases/day to 4,400/day. “And,” he adds, “we designed the line so that it is ergonomically friendly, so that the operators’ safety is top of mind.”
Gentle, yet speedy, packaging
On the day of Packaging World’s visit to Mission Bell, the new line was filling a 3-L BIB of Hardys Chardonnay. The richly colored, gold-and-black B-flute corrugated box is converted by Pacific Southwest Container (PSC, www.teampsc.com), which offset-prints the box in four colors plus an aqueous, UV coating. Because of the delicate finish used on the wine boxes, Hartman says that PSC met with the line’s main equipment suppliers to ensure “that through all the manipulation of the box on the line, it would remain in a pristine condition.”
At the head of the 3-L BIB line is a Douglas Axiom case erector equipped with a Nordson (www.nordson.com) hot-melt glue applicator. The case erector, an earlier generation of which is used on the 5-L line, uses a servo-driven, intermittent-motion process to form the wine box, seal the top, and then turn the box from its side to an upright position, with the open, bottom end facing up. Hartman says the equipment was chosen because of its familiar technology and its reputation as a solid machine.
After being set upright, boxes travel along a conveyor. If line interruptions downstream cause boxes to mass together, they are conveyed into a Hartness Dynac Model 6400 accumulator. The multilevel conveyor uses first-in/first-out pressureless product handling and accumulation and provides four to five minutes of accumulation time. Hartman says that Hartness was chosen as a supplier because of Mission Bell’s positive experiences with its equipment in the past and because of the company’s level of dedication. “They are committed to making us a success,” he says.
Next on the line are two Rapak Autokap 1200E single-head gravity fillers, selected to address Mission Bell’s sterility, shelf-life, and speed requirements. Hartman says the “overwhelming decision-maker” in choosing Rapak’s equipment was its new in-place cleaning solution, which uses steam to keep the filling valve sterile, even during short-term downtime. At least as important is the machine’s low level of oxygen pickup during filling—from zero to 0.3 parts/million.
“One of the biggest concerns we’ve had in the past with BIB was the oxygen introduced into the wine during the filling process. That’s really what impacts our shelf life,” says Hartman. “With our filler, we have realized a near-zero oxygen pickup. That’s a big plus, because it gives the product added shelf life during transportation and delivery and on the shelf. So when the customer buys the product, we are giving it to them in as pure a condition as possible.”
Premade bags with the fitment attached, from Scholle (www.scholle.com), are fed to the machines from rolls and are filled at a rate of 15 to 20 bags/min. According to Hartman, the filling accuracy for Mission Bell’s 3-L wine bags is required to stay within ±12 g. With the Autokap machines, it is achieving a ±3-g accuracy.
Once a bag is filled and its spout fitment sealed, it drops below into a waiting box, which has been conveyed from the accumulator. To ensure that the bag has been placed into the box in the proper orientation so that the consumer can easily locate the bag spout when the box is opened, the package is conveyed through two Cognex (www.cognex.com) In-Sight 5100 vision systems. After that, a Xymark 7S dot-matrix laser printer from Videojet Technologies (www.videojet.com) adds the manufacturing date to the box.
Next on the line is a second Hartness Dynac 6400 that provides another four to five minutes of accumulation time—“long enough for the operator to detect an interruption, clear the problem, and reset the machine,” says Hartman.
Mission makes its case downstream
To seal the box, Mission Bell installed a second Douglas Axiom machine equipped with a Nordson hot-melt adhesive system. After sealing the bottom flaps of the box, the machine gently turns the box right-side up using a curving belt conveyor. Of the performance of the machine, Hartman says that very little operator intervention is required. “Once you get it started in the morning, it will pretty much run all day,” he adds.
The sealed box then conveys into an SLM-25-C end-load case packer from PMI, which is designed for easy changeover to handle a range of case configurations. Mission Bell packs its 3-L BIB products in 3-, 4-, and 6-pack cases and in 6-pack trays; its 5-L BIB goes into a 4-pack case. Directly following the case packer is an SIC-30 automatic shrink wrapper, also from PMI. Mission Bell shrink-wraps its cases with film to minimize the damage resulting from “leakers.” “Secondary damage is the worst problem in the warehouse,” explains Hartman. “Without shrink-wrapping, one leaky bag could affect up to 15 other cases.”
After wrapping, the case is conveyed past a Diagraph (www.diagraph.com) PA/5000LT™ label printer/applicator that applies a label to its end. It then it travels up a spiral conveyor from Ryson Intl. (www.ryson.com) that brings it to a horizontal conveyor at near-ceiling level that carries it about 150 ft to a Model HL4000 high-level palletizer from Columbia. “Because our case speeds are not that demanding, we chose a reliable, top-feed machine,” says Hartman. “Columbia is extremely price-competitive, and the value for the dollar has proven to be very significant in that, once again, we have a machine center that is virtually maintenance-free and is very operator-friendly.”
The final piece of equipment on the line is an in-line WCRT-200 stretch wrapper from Wulftec (www.wulftec.com) that wraps the pallets and conveys them out of the stretch-wrap area, to await forklift transport to the warehouse.
Requirements met, surpassed
Using tried-and-true technologies and packaging equipment vendors, Mission Bell achieved an efficient and clean-running BIB line that is meeting its requirements for minimal labor and high uptime. Concludes Hartman: “While the line is a typical BIB line, with the addition of Ethernet and an ergonomic layout, as well as the fillers’ ability to maintain a sterile condition, we believe we have pushed available technology to achieve outstanding results.”