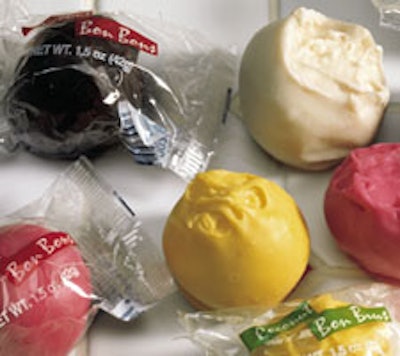
Consumers had spoken, and the message to Macon, GA-based Crown Candy Corp. was clear: “Bigger sugar buzz for our bon bon buck!” As a result, the candy manufacturer added a larger coconut-filled bon bon to its line of Southern-style specialty candies and subsequently voted its old wrapping equipment off of the island.
After looking at several machines on the market, the firm selected the Delta Wrapper from Delta Systems (Rogers, AR) as a replacement. Installed on the line in December, 1999, the wrapper uses a PC control and touchscreen display to help simplify a previously labor-intensive process, while increasing speeds from 65/min to 125/min. A total of four employees can supply product and film to the wrapper and box the outfeeding wrapped bon bons, also at 125/min. The wrapper’s minimal changeover time allows Crown to assign additional line workers to other jobs in the plant.
“The old equipment had a one-up head with a maximum speed of 65 a minute,” says vice president of production Roger Brooking. “I needed a two-up head with speeds of 125 or more,” Moreover, Brooking wanted to speed up the wrapping process without extending downtime during product changeovers, he says. It was also important that the candies be individually wrapped with the overwrap’s seam on the bottom of the bon bon. The forming box on the old equipment was not correctly angled for Crown’s bon bon line needs.
The new unit’s control system, which Delta refers to as a “one-box solution,” combines Human Machine Interface (HMI), logic and motion control into one physical control. Traditional PLC-controlled wrappers typically require three separate physical controls. Bottom line: On the Delta Wrapper, only one control needs to be programmed and maintained, instead of three.
Smooth operation
Due partly to the Delta Wrapper’s use of PC-controlled motion control technology, the packaging process on the horizontal flow wrapper is very efficient, according to Brooking. Two line workers hand-feed bon bons onto the machine’s cantilevered infeed conveyor, where each candy is lugged separately. The cantilever design means that all rollers and drives are mounted only from the back of the machine. Because the front of the machine is unobstructed, belts are easily accessible and can be slipped off quickly for cleaning.
An overhead dispenser feeds cellophane downward to a conveyor-level forming box that forms the single web of cellophane into a tube shape and awaits the candies. As bon bons reach the wrapping station, a pusher arm advances the candies into the tube-shaped cellophane. Once a piece of candy is in the tube, it is oriented to assure proper film cutoff points. A series of three rotary heat-seal bars fin-seal the film edges under the candy’s flat bottom as candies and tube continue through the machine. After fin-sealing, a single-head crimper simultaneously crimp-seals and cuts the ends of each bon bon’s wrapper.
The continuous wrapping/sealing process delivers individually wrapped candies to the outfeed conveyor. From there, the candy is manually counted and sorted by color before being packed into either a 32-count polyvinyl chloride tub or an 82-count corrugated counter display.
The precision of the process greatly pleases Brooking. “The old machine tended to fold the material too tightly when it wrapped, and it would pick a piece of candy up and turn it every which way,” he explains. “But the Delta Wrapper has belts on its infeed system that hold each piece of candy in place. That ensures that the fold of the wrapper gets on the bottom.” Brooking declines to specify the cellophane’s mil thickness, adding that Crown will soon switch to a laminated film.
Simplified changeover
In addition to not being able to accommodate the larger bon bons, Crown’s previous wrapper required laborious and time-consuming changeovers between products. Brooking says that adjusting the lugs on the old wrapper’s infeed conveyor to accommodate a different candy size had to be done by hand. But the Delta Wrapper handles changeover via touchscreen software. All timing functions can be programmed by pushing a few buttons and selecting the appropriate preprogrammed selection, while sizing adjustments may need to be made manually on the forming box, says the company.
Brooking wanted his new machine to be equipped with servo motors, pointing out, “They completely control the whole unit.
“I could put 40 different items through the machine if I wanted, and with the touchscreen, I can make the necessary wrapper changes in a few minutes,” Brooking says. The difference in sizes can be significant, from Crown’s smaller bon bons to its 6” pecan logs.
With servo motors and drives, adjustments can be made by changing the instructions the PC controller sends to the drive. Such changes can even be done from the HMI screen. That saves a lot of time compared to non-servo-controlled equipment, which requires manual adjustment.
Additionally, the machine’s compact footprint allows Crown to run an extra–long infeed conveyor into the wrapper, without using more floor space than before. This permits the bon bons to be fed manually by as many as three workers, saving Crown the expense of an automatic feeder. Brooking also appreciates the wrapper’s no-product/no-wrap feature, which he says saves a lot of film.
The coconut bon bons are available in club, specialty and discount stores nationwide, retailing from 33¢ to 50¢ each, with a one-year shelf life. Brooking says sales have met expectations, and he’s thankful for the smooth launch of the new product.
“It’s a wrapper that thinks,” sums up Brooking. “It’s the key machine for us right now.”