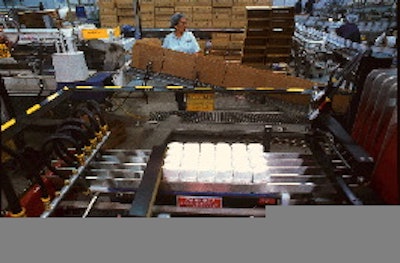
When Chesebrough-Pond's upgraded its body wash line, it decided to automate manual case packing. However, the tapered design of several of the containers made them susceptible to shingling that can create feeding problems for automatic case packers. C-P chose a casepacker from Hartness Intl. (Greenville, SC) that's specifically designed to prevent shingling of such containers. At the packer's infeed, a servo-driven diverter directs a single-lane container infeed into four parallel lanes. The diverter, which Hartness refers to as a high-speed laner, uses servo drives to intermittently shift containers into the four lanes. In the four-lane infeed, bottles travel shoulder to shoulder. They are prevented from shingling due to narrowly spaced lane dividers that restrict the bottles from turning, binding or stopping. Bottles accumulate against a backstop until the pack pattern of eight, 12 or 24 bottles is ready. Next, an air transport system grabs the bottles via inflatable air bladders and moves them forward over a grid section. Bottles are dropped about three inches into the grid. The grid lowers until it's positioned over a previously erected case. (Cases are erected and sealed separately.) Once in position, stainless steel fingers on the grid open up and guide the bottles into a tight pattern into the case. In keeping with Chesebrough-Pond's fast-changeover philosophy, the machine requires no tools for changeover, relying instead on handwheels. Changeover takes about 30 minutes for an operator, 15 for a mechanic, and consists of swapping change parts in the diverter, packer bed and laner. An Allen-Bradley (Milwaukee, WI) Model 504 handles many of the changeover settings automatically. "The PLC stores the settings for each particular case that we pack," explains Charles Miller, packaging technology leader. "For each job, there are 36 total parameters that control all pneumatic and timing functions of the machine."