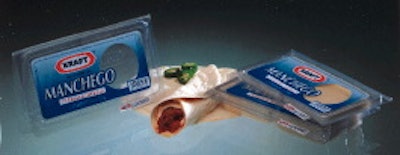
Last May, Kraft Foods de Mexico introduced its Manchego-style sliced pro-cessed cheeses in two hinged clamshells that stand out from the flexible film packs that dominate cheese packaging in Mexico. The unique Barex® CAM resin used to make the clamshell is supplied by BP Chemicals (Cleveland, OH). BP makes the resin exclusively for American Mirrex (New Castle, DE). AM uses calendering equipment to produce its Mirran(TM) sheet stock. Blistertec (Anahuac, Mexico) thermoforms that sheet into individual clamshells. Jorge Saucedo Varela, Kraft's packaging engineer for the Manchego cheese project, says Mexican consumers typically use the processed cheese for dishes such as quesadillas, or melt it over tortillas. Saucedo admits that clamshells are a costlier alternative than flexible film packs. In this instance, however, package differentiation was more important than economics. The decision has proven to be a smart one. "We are now packaging up to 12 tons of the product per week, compared to 10 tons in the first month of production," he says. "It's proving to be very successful." Mexico City-based Kraft Foods de Mexico manually packs the clamshells with slices that are individually wrapped in a polyethylene/ polypropylene film lamination. For the 10-slice version, five slices are placed into each of the clamshell's two compartments. The larger package holds 10 slices per side. Economics weren't completely forgotten. For example, both clamshell sizes are thermoformed using a single mold. The difference is the draw; the larger size is about 1/2" deeper than the 10-slice version. For the smaller clamshell, Blistertec adds an insert to the mold to reduce the depth. The resin's rigidity and thermoforming characteristics allow production of a 20-g clamshell for the larger version. It performs comparably to 35-g clamshells made from alternate resins, Saucedo says. One competitor in Mexico markets sliced cheese in a polyvinyl chloride blister. However, Saucedo believes that clamshell has weaknesses. "That package, we feel, doesn't have as good an appearance as ours, and there's some damage to those clamshells. It has structural problems because it is made from a thin layer of PVC so it gets compressed in transport, and the borders and bottoms get bent. "We selected the Mirran sheet," he continues, "because we wanted a higher oxygen barrier for ensuring product freshness and [to give] us a longer shelf than other resins could provide. The clamshell for the cheese provides excellent oxygen and aroma barriers that prevent the cheese from picking up the scent of other products in the refrigerator. "Its ergonomic shape makes it easy to handle and its snap closing top makes it easy for the consumer to open," he adds. Corrugated shippers containing the clamshell-packed cheeses have been distributed as far as 3ꯠ km (1꽀 miles) without damage. Product testing indicates that the product is good for one year, although Kraft codes it for five months. That makes it comparable to the company's sliced cheeses packed in flexible film.