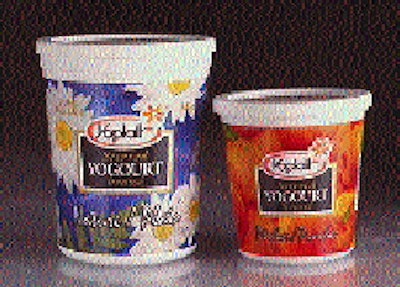
Dry offset printing on rotary presses has long been the mainstay of decoration in the plastic cup and tub business. Until recently though, designers were limited by the fact that no press manufacturer had ever designed and built one with more than six color stations. Polytainers Inc. (Toronto, Ontario, Canada) changed that in response to requests from its customers. The company urged Van Dam Machine (West Paterson, NJ) to build what is believed to be the first eight-color dry offset press in the world. Installed in late 1992, it now runs around the clock seven days a week. "Customers needed more colors than six heads could provide," says Polytainers president Robert Barrett. "If a company wants its logo on a container and the colors in the logo take up three print heads, there are only three colors left in a six-head press. If the customer also wants a process-printed fruit cocktail on that container, we need more than six print heads to get it done." Among Polytainers' customers that take advantage of the eight-color press is Ultima Foods, the Montreal firm licensed to produce and market the Yoplait brand of yogurt in Canada. "When the press was available and we saw the improved fruit renditions it could produce, we moved a few flavors of our regular stirred yogurt into it," says Ultima's Sylvie Bourget. "We were so pleased with the results that we're now moving all our 500-gram and 1-kilogram regular stirred yogurt into cups printed on the eight-color press. That will represent about 20% of our total yogurt volume." For Polytainers, it's a nice new chunk of business that might not have materialized had it not been for the new printer. What makes these Yoplait cups so suitable for decorating on an eight-color press is that their graphics include photography. Achieving true reproduction of a photographic image on a cup is not easy, and though it can be accomplished on a press having six color heads, it can be done better with eight heads because there's more latitude. A good example is a cup carrying a picture of a peach. In printing the peach, black ink is used to give the fruit shading and to increase contrast. This is what makes the image life-like and appealing. But the black ink must be delivered with a fine dot pattern or the effect becomes anything but life-like. That can become a problem when, on another part of the same cup, a bar code is required. This requires a good, solid laydown of black ink or else the code may prove unscannable. On a six-color press, it might be necessary to compromise on the quality of the peach and the bar code because there aren't enough stations to dedicate one to the black that's in the peach and another to the bar code black When eight color heads are available, one can be used to deliver just the right flow of black ink to produce the subtle shadings of the peach while another can be used for the heavier flow required by the bar code. It's the same color ink in both color heads, but the added control over how it's laid down makes it possible to get all the definition a bar code needs without overwhelming the subtle shading required in the peach.