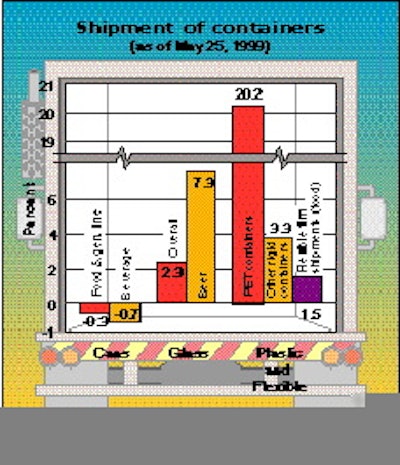
For those who haven't personally attended an interpack exposition, the physical demands are somewhat different than those experienced at Pack Expo. Last year, really for the first time in many Pack Expo iterations, McCormick Place felt cohesive and comfortable. When combined with the Intl. Exposition of Food Processors, the 1.2 million sq' seemed to be in a single location, even though five separate halls were used. Mostly, I think, this was due to the short walk from the East halls to the mammoth, commanding South hall, with the North halls serving as flankers. For the first time, there was no real need to consider walking outside. The interpack experience is as different as November in Chicago is to Dsseldorf in May. Although many of the 15 separate exhibition halls are connected via walk-ways, much of the time the walk outside is a refreshing change--unless you get caught in a shower. And if you're attempting to make appointments, the outside shuttle bus can be a time saver. Quicker shuttle buses from McCormick Place to downtown Chicago hotels, promised for next Pack Expo, will help relieve the end-of-day congestion for a site where a car is often more of a liability than a help, and waiting for a cab can be taxing. Inside, at the exhibits, there is a great deal of similarity. Although many interpack exhibits seem larger than those at Pack Expo, the trends in machinery are much the same. Like Pack Expo last year, there was a stunning array of robots operating in machines at interpack. But the most interesting trend, I felt, was a continuation of multifunction or combination machines, something that was becoming obvious at Pack Expo last fall. Certainly, many companies have made monobloc filler/capper systems in the past, often incorporating labeling or cottoning systems, as well. But most recently, we're beginning to see other combinations, like palletizer/stretch-wrap systems, case printing and sealing combos, product feeders and wrappers together, and case erectors and packers in a machine run by a single drive. In this issue (see p. 22), a produce packer is using an unusual combination machine that produces a net bag with a header, decorative wrap and a variable-information label. At interpack, we began to see for the first time integrated container manufacturing with filling and sealing equipment, thanks to Sidel (Norcross, GA). This brings to mind the heated debate some years ago when some companies were offering in-line plastic sheet extrusion with thermoforming machines, while others felt more efficiency could be gained by keeping the two operations separate. The same issue was debated by soft drink companies that molded and filled their own bottles: in-line or individual functions. Usually the deciding factor was scale or the number of units required. If the slowest part of an in-line system was more than adequate for production needs, in-line molding and filling could be considered. Today, it's not uncommon to find operations with three-shift molding and two-shift operation of the packaging line, with some accumulation or a storage device in between. At exactly the same time as more functional machine combinations are being offered (ergo, fewer vendors to deal with), the options in machine components are often broader than ever. To use an automotive metaphor, you can now buy a pick-up truck with the seating capacity and the same number of doors as a sedan. And you have a wider choice of engines, transmissions, interiors, etc. I think North American buyers have led the way in seeking more options on packaging equipment, whether it's the mechanics, electrical systems, electronics or even software. In the past, some U.S. manufacturers loudly complained that some European machinery builders lacked the flexibility in providing components that would be compatible with other equipment in their plants. Based on conversations with many European machinery makers at interpack 99, that difference between North America and Europe is being eliminated. c