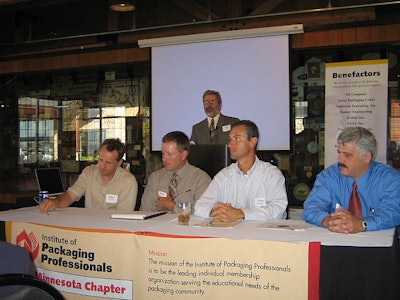
IoPP education panel addresses packaging machinery technicians’ skill sets
At the September meeting of the IoPP Minnesota Chapter Packaging World Editor Pat Reynolds laid out the results of a survey conducted by his publication to a room filled with packagers educators and a strong turnout of students interested in learning what skills prospective employers value. And the survey said? New technologies are calling for a new set of mechatronic skills.
Director of Packaging Engineering for General Mills Gregg Stedronsky agreed that “more and more of our equipment is coming in with sophisticated servo control.” To keep up Stedronsky said “Plants look for entry level people open to new technology and ready to overcome barriers to progress. We look for aptitude and a willingness to learn because the half life of technology is so short.”
At Douglas Machine Electrical Engineering Manager Joe Faust finds that “the electrical people with software backgrounds are leading the way now.” He notes that on the design team “Electrical engineers have the math background drives networking and programming backgrounds that mechanical engineers typically don’t have.”
That’s why says Todd Zarbok Mechatronics Curriculum Coordinator for Alexandria Technical College’s Center for Automation and Motion Control “we’re integrating all those skill sets into an overall mechatronic curriculum for 2-year students. Previously these have been 4-year engineers’ sole responsibility. Whether it’s ELAU equipment or cams and gears students need to learn these skills.”
An audience member noted that these are not new skills to which Zarbok replied that the difference is “integrating them into a single curriculum which the Europeans have been doing for twenty years.”
Faust noted that Douglas hires people with 2-year degrees who then “spend one year learning about our machinery. That rounds them out. Hopefully they bring the fundamental technical skills to jump right in.”
Tom Jensen ELAU’s Senior Technology Evangelist noted that “with the right information and skills I can answer 5-6 questions and be within 90% of identifying a problem. What we need to do is empower the guys at the plant level to make those educated guesses.”
Stedronsky added that “as machines get more complex diagnosis must get simpler. We need gap analysis and tools that help us understand the health of the system.
“The technology is there that one cable can diagnose a machine” answered Jensen. “Diagnosis should be quick and simple. Then let the team in the factory see who has the most appropriate skills to fix a particular problem.”
Stedronsky also sees the network cable as causing a fundamental “shift toward information. As product flows through the factory information has to flow with it. In the future you will see more focus on the system rather than stand alone packaging unit operations. Lot tracking trace and recall are big issues in our industry. You have to be able to maintain a machine and also extract information from a machine without creating too much of an overhead burden.
“More and more” Stedronsky continued “the technicians’ ability to interface with our plant IT organization is becoming important. Wires go through the walls today. It’s less about the physical geometry of a plant and more about the networks. Our IT friends are very concerned about virus protection patch management and network care – things you don’t always think about when you are troubleshooting machines.”
Asked whether General Mills was moving away from PLCs to more sophisticated controls Stedronsky countered that “when you’re doing straightforward machine control the PLC is right tool for the job. With complex servo motion – many axis machines and robots – we see the developers choosing controls more suited for those applications. We believe packaging technology will continue to be split between the two.
A member of the audience asked how the vocational-technical colleges are expected to keep up with cutting edge technology.
“The individual vo-techs can’t afford it” Zarbok answered. “We partner with automation suppliers who donate equipment and see that as a “storefront.” Tom (Jensen of ELAU) has been to our center to give seminars. That’s why we’ve also gone to the National Science Foundation and Society of Manufacturing Engineers for grants to develop new curriculum.”
This led to the question of which skills are most important to learn – servos robotics or basics of software?
“We need a balance” Faust answered. “Now we’re transferring basic cam motion to servo motion. The required skill is more basic motion than robotics although that may change in the next 5-10 years.”
Jensen offered that “there are certain standards that are well worth learning. We’re seeing standardized fieldbuses and when it comes to PLC programming IEC 61131 is the standard. CAMC (Zarbok’s institution) is teaching these. With the proper use of the IEC languages you can have a single Function Block (a software object) for doing a robot or a servo infeed. The IEC 61131 languages a programmer chooses to use are also important. In Ladder Diagram it may take 4 to 5 Function Blocks to perform robotics. In Structured Text I can just write the equation into a single Function Block.”
With that Sher Van Cleve of Flaire Print Communications the tireless IoPP Minnesota Chapter Event Chair summarized. “Many years ago on the graphics side we saw a huge move away from proprietary equipment and software that were intended to lock out competitors. These proprietary limitations sometimes made it difficult for clients to engage production options. Today we have open architectures that permit multi-vendor communications enhancing flexibility and work flows. Now it’s your turn in the engineering world. Change is good. We should embrace it.”
And hopefully teach it in both 2- and 4-year mechatronics curricula.