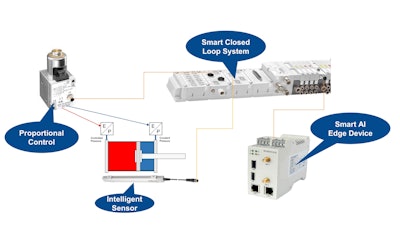
Some of the packaging machinery used in the agricultural industry is built to last a mighty long time. But that doesn’t make it immune to upgrades, especially when it comes to controls. One such upgrade was the subject of a presentation delivered at the Innovation Stage at PACK EXPO Las Vegas last September by Chris Noble, Business Development Manager F&B | Packaging at Emerson Automation Solutions.
The specific packaging equipment involved was a 15-year-old bagger used to produce, for example, 75-lb bags of corn kernels or soy beans. The machine takes flat, empty sewn-open-mouth bags from a magazine feed, positions them beneath a funnel, and discharges soy beans, let’s say, through the funnel and into the bag before sewing the bags shut and discharging them.
The pneumatic actuator responsible for opening and closing a gate valve releasing beans into the funnel was originally capable of just two positions: full open or closed. When the bagger called for product, the gate valve would open and release product into the funnel, but it would do so in what might be called a “dumb” fashion. Product would rush through the funnel and then suddenly stop, so there was no consistency in the flow. This resulted in too many bags being inaccurately filled, which in turn led to rework, wasted bags, and overtime. Upon examining the situation, Noble figured that there had to be a better way.
“First it was a matter of adding intelligence to the pneumatic actuator responsible for product flow,” says Noble. “From there it evolved into an IOT opportunity where we now take a look at upstream and downstream sensors so that there’s a way to make each actuator/gate valve ‘know’ what percentage of its full stroke it needs to execute in order to produce a smooth and consistent flow of product into a bag.”