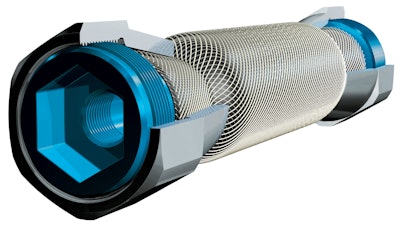
A leading maker of ultrasonic welding and cutting technologies, Rinco Ultrasonics recently developed an unusual sealing tool for the flexible pouch segment of the packaging market.
“Typically some type of air cylinder is used to actuate the ultrasonic sealing jaws,” says Gordon Hull, managing director at Rinco. “But to get the forces required to seal flexible materials at the speeds that today’s applications call for, you need a pretty wide gripper, which in turn requires a very large pneumatic cylinder. That kind of pneumatic cylinder takes up too much real estate on the horizontal or rotary form/fill/seal machines for which this tool is designed. And if you are running duplex or triplex—where two or three pouches are sealed per stroke—it gets even more complicated. That’s what led us to search for a high-force, high-speed solution in a small footprint.”
Eventually the search led to Gibson Engineering, a distributor and automation solutions provider specializing in vision, motion control equipment, machine and process controls, sensors, fluid power, and machine safeguarding equipment. Gibson recommended a device from Festo called a “fluidic muscle.” This completely new breed of pneumatic actuator is a “bionic” muscle—i.e., based on a design taken from nature. It consists mainly of a hollow elastomer cylinder embedded with aramid fibers, which are manufactured fibers in which the fiberforming substance is a long-chain synthetic polyamide. Aramid is spun as a multifilament by a proprietary process developed by DuPont Co..