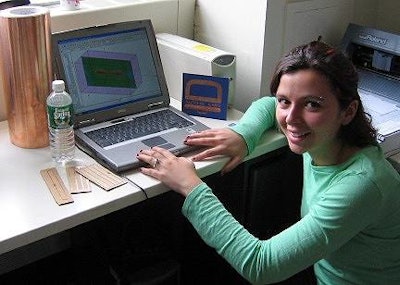
It seems logical that the smartest minds should tackle the toughest challenges. That’s the mindset at the Auto-ID Labs of the Massachusetts Institute of Technology, Cambridge, MA. RFID Antenna’s May visit here uncovers the group’s latest research and developments in RFID.
The group is led by research director Daniel Engels and project director Rich Fletcher, who guide the minds and hands of the graduate student researchers to increase their understanding of RFID. The graduate students working on various projects are Alki Delichatsios, Uttara Marti, Rich Redemske, and Jonathan Wolk.
Tagging bottled water
One of the toughest applications for RFID in packaging is said to be high-moisture products. MIT is pushing the envelope in one of its latest research projects by developing a UHF RFID tag for bottles of water. The project will yield an item-level RFID tag design whose performance is maximized for single-serve PET bottles of water. The goal is a tag that can be read at the item level at least two layers deep when cased in a 4X6 arrangement inside a corrugated box. Researcher Alki Delichatsios will be working on this project through summer 2006.
“Our sponsors have liquid-filled bottles,” says Engels, “yet this research has great application to a broad range of products. Besides, everyone says it can’t be done, so it’s the perfect challenge for us to accept. We will succeed and change people’s perception of UHF around liquids, just as we have done for metals.”
The project is starting from scratch—Ms. Delichatsios will not be using off-the-shelf tags; instead, she will design her own tags using HFFS antenna design software from Ansoft. The project will involve Class 1 Gen 1 technology straps (a chip and connector that’s attached to the antenna) from Alien Technology and inlays (chip and antenna) from Philips Electronics. The antenna will be wrapped around the bottle like a label. The researcher will develop five to six possible designs and test them.
Air gaps and helpful metal
Another project hopes to provide evidence that the words helpful and metal can be used together in conjunction with RFID.
Researcher Uttara Marti is studying the effect of air gaps in RF performance. In summary, air gaps are good.
“In this case, metal is good,” observes Engels of research involving aluminum-foil-lined materials. Properly placed, these materials can direct the RF energy deeper within a pallet load to read tags on packages.
Marti is also looking at air gaps between palletized layers, such as layers of cased product. Even air gaps within cases improve performance as does increased headspace within each of the cased bottles, Marti has found. Findings presented in her thesis, which will be divulged in more detail in next month’s issue, indicate that RF energy can, for example, be directed through pallets using innovative designs and configurations of packaging materials and configurations.
World’s first graphical simulation
The project, Implementation of graphical simulator, by graduate student Jonathan Wolk, provides the world’s first real-time visual 3-D modeling of reader-antenna and tags. Rather than using a graphical platform such as AutoCAD, Wolk started from scratch. As challenging as that sounds, such an undertaking comes naturally to Wolk, whose expertise includes computer graphics and electromagnetics.
With the software simulation program, users can place a tagged box into a field and see how well it performs within the variables of antenna type (patch or isotropic); polarization (linear or circular); field strength; tag placement on the box. Box contents can be air (empty), liquid, or aluminum. The view can be reoriented—rotated, raised or lowered, or zoomed in or out. The user can “fly” around the 3-D scene to view the field from all angles, internally as well as externally. The program can look at the interaction between two boxes in the field.
The tag’s color—shades of red, green or yellow—indicates the strength of the RF signal. Based on research, researchers know that 10 milliwatts is the average threshold level, the lowest power level that the tag can be read.
Wolk’s latest efforts includes creating little boxes within a larger box, in effect creating unit-level items inside a master case.
Wolk says the simulation program provides a “quick and dirty” method to home in preferred positioning and orientation of a tag and case. “The program has a lot of flexibility,” he sums.
Field probe update
We also wanted to get a first-hand look and an update on MIT’s economical RFID field probe, which we covered in an article published in January. The development was handled by Rich Redemske, who has a background in firmware and electrical engineering. The 9’’x3’’field probe integrates an Electronic Product Code RFID tag emulator and a sensor probe. The device is capable of reporting various sensor values continuously. Those numbers are converted by a software program Redemske developed into a graphical representation. Graphics color (red, green, yellow) provide an indication of the RF signal’s power level in relative values. By distributing multiple probes around a particular pallet configuration, the user can obtain instantaneous feedback as to the RFID field strength and signal quality. The tool can be used to pinpoint and troubleshoot tag read problems.
Redemske has been working on increasing the probe’s read distance range. Initially it was 2 meters, currently it’s 3 to 4 meters, and the next goal is a range of 4-5 meters, or about 15 ft. The field probe also features an LED readout, which Redemske says is mandatory for any type of field probe and permits anyone to “have rough, but instant feedback on results.” The added performance “ups” the unit’s parts costs to around $25.
“Rich Fletcher and myself take a great deal of pride in the students for jobs very well done,” says Engels. “They have all done fantastic work.”
For further information on these MIT RFID projects, contact Dr. Daniel Engels at the Auto-ID Labs.