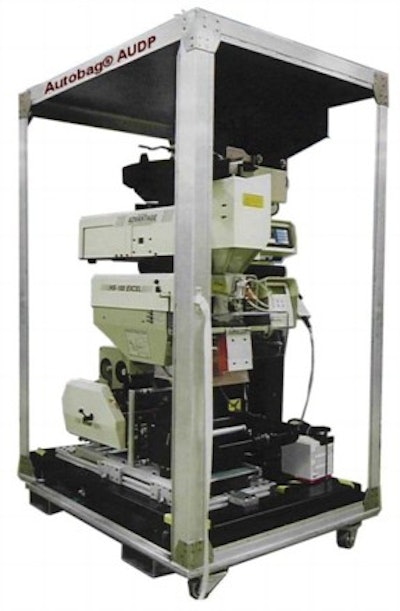
Flexibility. Speed. Total Accountability. These are the criteria mandated by the Centers for Disease Control and Prevention (CDC) in the administration of the Public Health Emergency Preparedness and Response program. From a field of the nation’s top packaging companies, Automated Packaging was chosen by the CDC to provide packaging technologies vital to the rapid deployment initiatives of the program. As a selected CDC program partner, Automated Packaging is now a certified federal supplier of critical product, service and support to the agency’s Bioterrorism Preparedness and Response program.
Public health emergency response and preparedness program
The CDC’s emergency preparedness and response activities are coordinated by the National Center for Environmental Health's Emergency Preparedness and Response Branch (EPRB). Responsibilities of this federal agency include emerging infectious diseases, chronic diseases, environmental hazards, and bioterrorism. Administered by the Department of Health and Human Services, the CDC has been at the center of public health emergencies for decades. Bioterrorism is not new to the agency agenda. Since 1998, well before 911 and the ensuing anthrax outbreak, the CDC through EPRB has worked toward readiness for technologic attack. Because of this pro-active preparation, CDC response to the biological assault on the U.S. was prompt. Within seven hours of the attack on the World Trade Center, fifty tons of medical supplies were delivered to New York City. During the subsequent anthrax attacks medical provisions were also promptly delivered to the various health departments.
Bioterrorism objectives of the emergency preparedness and response program
The anthrax strikes that followed 911 were the first bioterrorist attack in the United States. Since then, the CDC has pushed the emergency preparedness program forward at a greatly accelerated pace. As has been the case since 1998, the primary program initiatives are rapid identification and prompt response. It is the goal of this agency to guarantee these initiatives by building and strengthening,
--regional, state and local capacities
--communication networks and systems
--treatment deployment and management vehicles.
Enormous progress has been made in expanding all of these capacities. Of particular interest to this article, the CDC has added many medical assets. These include new antibiotics, vaccine products and 12 hour push packages. Push packs are large containers full of medical resources designed for at-site of incident delivery. These inventories will be delivered within 12 hours of a bioterrorist attack. Automated Packaging has been instrumental in this effort, helping the CDC reinforce these critical program mobilization resources and capacities. Working hand in hand with the CDC, Automated Packaging developed a comprehensive packaging solution.
This included everything from custom designed packaging equipment and materials to the on-going training and service systems that support the management and rapid deployment of anthrax antibiotics, CIPRO and Doxycycline. In the event of a bioterrorist attack, preliminary supplies of these life-saving pharmaceuticals will be deployed and distributed to the infected area. The affected population will rapidly receive sufficient quantities of these and other medical supplies to meet initial treatment needs. Automated Packaging Autobag® equipment will be used to ensure that individual prescriptions are dispensed reliably and packaged on-site in accordance with FDA specification.
Performance expectations
Over the course of several months, Automated Packaging worked closely with the CDC to assess the needs and packaging technology required to accomplish this mission. The model that evolved during this time encompassed not just the packaging equipment and materials, but a total vendor-supplied packaging solution. The commitment to CDC vendor requirements included:
--single source provision and accountability
--total reliability with zero downtime
--on-call and on-going field support
--superior, comprehensive service ability
--custom design capability
It was imperative to the CDC that one supplier be the sole source provider of both the service and the system. Explicit equipment requirements were equally demanding. These included,
--high-speed counting, bagging, sealing and printing
--multiple language imprinting
--sequential and demand labeling
--system matched consumables
--database interface and records traceability
--spare parts supply and availability
--at-site power requirements
--mobility and transportability
--size and weight envelope
--ease of operation
--FDA pharmaceutical standards compliance
Automated Packaging Systems develops a partnership
From the start, Automated Packaging manufacturing representatives worked intimately with a core group from the CDC and Automated Packaging Custom Design and Integration team to coordinate the development process. However, in order to address both the equipment and vendor requirements, the entire organization quickly became involved in the project. Working initially with standard bagging equipment, a product placebo, and the preliminary specification information gathered from the CDC, Autobag Custom Design and Integration team developed a system proposal.
For security interest, communication by the CDC was necessarily kept to the task at hand. Understandably, this made product development more difficult. Despite this obstacle, a product concept emerged that would accurately count, bag, seal and label at the required bags per minute.
The design utilized field-proven Autobag equipment. The HS-100™ Excel® is a high-speed bagger with an outstanding reliability performance record. Similarly, the Autobag Accu-Count® Advantage counter has consistently delivered accuracy and product accountability throughout its placement history. Finally, the system included an AutoLabel™ Precision™ Thermal printer, which has been highly effective in a wide range of applications.
Based on this system proposal, Automated Packaging conducted a regional demonstration of the concept. The CDC core team attended the presentation, witnessing the system in operation. The model, which was well received by the CDC, helped both groups identify what modifications were still needed. Armed with this information, the Autobag team held numerous engineering reviews re-designing and improving the original concept. Through innovative engineering and companywide teamwork, Automated Packaging resolved the design challenges and addressed the CDC critical vendor requirements.
The system had to be transportable, mobile and run ready within minutes of placement. To accommodate this, the Precision™ thermal printer was customized to slide under the bagger so the unit would fit the transport envelope and still provide for quick setup. In addition, Autobag Custom Design and Integration team tailored additional supporting components to meet these requirements. These included a compact compressor, specialized air dryer system for compressed air, separate drying units and an electric line conditioner to “clean” the power supply. Parts that might come in contact with the pharmaceuticals had to be specially coated to meet FDA standards.
The need for traceability turned out to be a particularly difficult obstacle. But again, the team effort at Automated Packaging resolved the issue by designing a prototype bag with a detachable header. Identical information could now be printed on both the bag and the header. The header could be torn off without damaging the bag’s integrity and then maintained for tracking purposes.
The custom designed packaging equipment guaranteed that the system would deliver total reliability and zero downtime. However, the other issue vital to the CDC was that the selected vendor be capable of providing a complete supplier and service solution. The existing infrastructure at Automated Packaging permitted the company to support all of these CDC needs. Automated Packaging specializes in customized packaging solutions. This means in-house design and manufacturing of equipment, options and consumables. It also means providing all of the technical and field support service products that make for a turnkey operation. As a result, Automated Packaging was able to offer sole source and accountability for all equipment, materials, spare parts, technicians, training and servicing related to the packaging system. This included on-call availability of personnel for unscheduled practice sessions, and of course, emergency deployment.
Automated Packaging Systems is an ISO 9002 certified facility. This quality sanction carries weight in the business-to-business arena. However, in order to conduct a business-to-government supplier relationship, the vendor must be on the approved Federal Supply Schedule (FSS). The Federal Supply Schedule is administered by the General Services Administration. This agency and the FSS procedure guarantee the integrity and pricing of products and services purchased by the government. It includes a range of acceptance assessments that support federal law. Since Automated Packaging had not previously sold to the government, the company was not listed on the FSS. Automated Packaging dedicated the necessary resources to complete the FSS application and approval process.
With all design details and service requirements worked out, Automated Packaging invited the CDC to their headquarters in Streetsboro, Ohio to present the final proposal. Though this would culminate the entire series of events that had occurred, ultimately the CDC decision would be based on speed, flexibility, and total accountability. Automated Packaging had clearly and continually demonstrated these criteria capabilities. Shortly after this presentation, the company learned of the CDC’s decision. The celebration was brief. An enormous amount of work still lay ahead.
Automated Packaging delivers
A massive manufacturing ramp-up began immediately, which included gearing up the service and support systems. The production schedule was very aggressive, requiring over 20 units to be manufactured and ready to ship in a very short time.
Automated Packaging enlisted the help of sub-tier suppliers so materials were procured almost instantly. Partial shipments began within 30 days of purchase order receipt. The production team continued to work on a constant rotation to meet the final delivery requirements.
Simultaneously, other departments worked toward the service and support objectives. Rapidly, the training program for the packaging system was developed. One month into manufacturing, the first fast-track training session was held for CDC personnel. The incredible pace of these activities continued for three months.
Within that time, Automated Packaging manufactured and deployed the entire order including all the system-matched supplies, spare parts, and peripheral equipment. Within that time, the service and support requirements were also met in full.
Conclusion
In the aftermath of 911, there have been many quiet heroes across the nation working behind the scenes to rebuild and strengthen America. Automated Packaging Manufacturing Representative, Dave Thoman worked very closely with his teammates and the CDC, coordinating much of the development phase. When asked how the company accomplished this seemingly impossible mission, Dave replied, “People and partnerships. Automated Packaging Systems has an outstanding product, but we didn’t do this alone. Collectively, from our vendors, our people and the Centers for Disease Control and Prevention, this was 100%, a team achievement.
Today, CDC transport has moved all the packaging units to undisclosed, strategic locations. Spontaneous practice sessions have been conducted to prove out the Autobag program and equipment. It is fully operational.