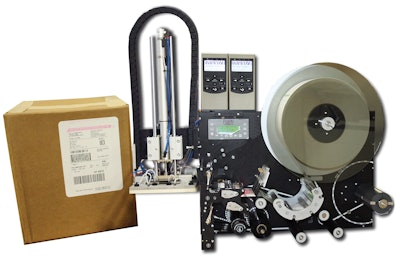
When the engineers at FOX IV Technologies realized that it was time to redesign their TwinPrint™ thermal-transfer labeling system, they saw it as an opportunity to overhaul their approach to pneumatics, too. So they established a stronger relationship with Asco and relied on Asco for a solution that was leaner and simpler. The result? Where twelve components were needed in the past, only five are needed now. In what might be the engineering understatement of the year, Director of Engineering Services Rick Fox III says, “That makes it a lot nicer.”
The TwinPrint thermal-transfer print-and-apply labeling system is aimed squarely at the e-commerce sector. In the past, the Amazons and Zappos of the world had to print out an 8x11-inch sheet of paper with confidential packing slip information and stuff it inside the corrugated shipper containing the product being shipped to a consumer. Or sometimes the packing slip information would be in a little plastic envelope applied to the outside of the case. With TwinPrint, which utilizes two thermal-transfer print heads, the shipping information is printed on the top label while the packing slip information is printed on the label release liner. The liner is die-cut such that it remains with the top label and provides a protective and secure adhesive perimeter around the label. Once applied to a case, the packing slip information on the printed liner remains confidential and provides tamper evidence protection during shipping. This packing slip is accessed by simply tearing a zipper strip.
“This is one of our more complex machines,” says Fox. “As we found ourselves adding additional pneumatic valves, we wanted to simplify things where the pneumatic assembly was concerned. What Asco has done is take all the individual valves we had and condensed them all down into a manifold. Five valves are now combined into one nice condensed unit.”