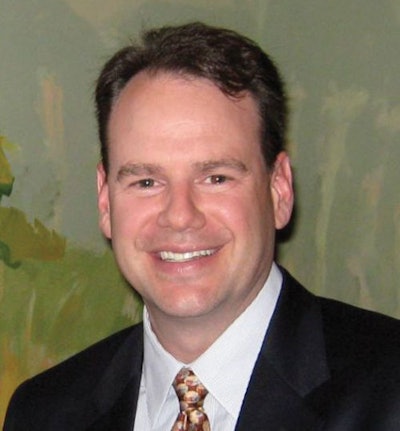
Packaging World:
What is the current status of FSAP, and the development of Hazard Analysis Critical Control Points (HACCP) models for packaging materials?
Wynn Wiksell:
At Pack Expo, members of the FSAP presented three courses on Packaging and Food Safety, which were all well attended by the industry. The topics were on Management Awareness to Food Safety Issues, Prerequisite Programs, and on the HACCP models themselves. In December, FSAP launched its first monthly periodical e-letter that brings pertinent news to its members. Interested parties can go to www.iopp.org and join and register under the FSAP technical committee to get on the distribution list. We received much positive feedback on the initial communication.
What has been learned about the improper labeling that was said to have caused 55% of food industry recalls, and what's been done to reduce those labeling problems?
Education and awareness represent the biggest first steps that we took. Those fundamental steps are important in getting everyone aligned. Other initiatives and groups such as the GFSI and PAC have helped bring a recurring message to the industry that this is essential. One of our big educational points around HACCP implementation and labeling is that there is not just one critical control point as most HACCP models suggest. We have encountered processes where up to three critical control points on one line are essential to the success of packaging processes.