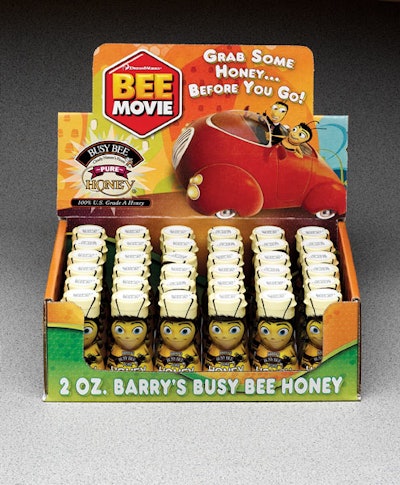
When Hillsboro, KS-based Golden Heritage Foods LLC, the second largest producer of retail branded honey in the U.S., heard the buzz about DreamWorks Animation’s fall 2007 feature film, Bee Movie, it jumped at the chance to create a bee-themed promotional product. The movie, a comedy featuring the voice of Jerry Seinfeld, follows the quest of animated bee Barry B. Benson as he ventures outside the hive.
Golden Heritage’s re-creation of Barry takes the form of a delightfully illustrated, 2-oz contoured honey bottle bearing Barry’s likeness on a colorful shrink-sleeve label (see sidebar). The petite, sleeved bottle was a departure for Golden Heritage, however, whose typical bottle sizes range from 8 to 40 oz for retail all the way up to 1-gal jugs for foodservice and 60-lb pails for the industrial ingredient market.
To accommodate the dainty bottles at the 200-cpm production speed required to meet movie-launch deadlines, Golden Heritage installed a new bottling line at its Latty, OH, facility in summer 2007. The line is specially equipped with machines agile enough to handle the tiny bottles, but flexible enough to accommodate sizes up to 1 gal for future bottling needs. Highlights of the line include a Model 75-ER shrink-sleeve label applicator and steam tunnel from PDC Intl. (www.pdc-corp.com); a Gen4 Pro/Fill 3000 volumetric liquid filler from Oden Corp. (www.odencorp.com); and an HP20 Motoman (www.motoman.com) robot equipped with custom end-of-arm tooling from Guide Engineering (www.guideeng.com) for automated case packing.
Labeler is precise, dependable
The Barry’s Busy Bee Pure Honey package owes its movie-star likeness to the PETG shrink-sleeve label printed with Barry’s image and precisely shrunk around the 3.5-in.-high, contoured bottle. To label the bottle, Golden Heritage says it required an applicator that could reach speeds of 200 cpm, could be delivered in time to meet the company’s production schedule, and was durable and dependable, requiring little maintenance.
Says Golden Heritage marketing manager Ben Gregory, “The applicator also had to be forgiving of slight variations in sleeve and container materials for high uptime performance while maintaining the accuracy of label placement.” It also needed to be capable of high-level application to a small, uniquely shaped, potentially unstable bottle and able to perform well with a range of sleeve materials.
“Offering high quality and a good track record, PDC Intl. was able to provide service solutions tailored to our application,” says Gregory.
The Model 75-ER shrink-sleeve labeler accommodates sleeve diameters from 0.375 to 3.5 in. and sleeve heights from 0.625 to 9 in. at speeds from 100 to 300 cpm. According to PDC, the labeler uses the company’s patented Tetrahedron Wedge technology to provide consistent handling of sleeve materials through the feeding, cutting, and application process.
Positioned after the capper on Golden Heritage’s new line, the Model 75-ER uses a dual timing screw to transport filled, capped containers into the application zone. After sleeves are perforated, cut to length, and positioned on the bottles, the containers exit the labeler and convey through a PDC-supplied quality inspection station. The bottles then move through a PDC single-zone steam tunnel that shrinks the sleeves onto the containers.
Given the bottle’s petite proportions, “there was a learning curve to get all of the parameters—timing, dwell, and temperature settings—set,” says Gregory. “Our production team worked closely with PDC to quickly address and resolve these challenges, which enabled us to meet our aggressive production deadlines.”
Fast filling, case-packing
To fill the tiny bottles with its viscous, pure clover honey, Golden Heritage installed an Oden Gen4 Pro/Fill 3000 10-spout automatic in-line volumetric filler. The machine is capable of fill volumes from 0.017 oz to 1.3 gal, at speeds to 250 cpm.
Each fill position on the Gen4 Pro/Fill 3000 has its own pump, a Waukesha (www.gowcb.com) Universal Series sanitary lobe-type pump, which delivers product to an Oden Gen2 316L stainless-steel positive shutoff nozzle. Each pump is servo-motor-driven, to allow for quick fill-volume changeover.
At the end of the line and unique to Golden Heritage is a high-speed Motoman HP20 robot custom-fitted with end-of-arm tooling from Guide Engineering. The vertical, jointed-arm HP20 robot, with six controlled axes of motion, employs vacuum cups to lift up 36 of the 2-oz honey bottles simultaneously and transport them to a corrugated display tray. The filled tray is then inspected by operators, and the tray’s lid is manually closed.
“The unique shape and size of the Barry Bee container is easily handled with robotic case packing,” says Gregory. “This robotic technology solved our high-speed packing challenges and provides for multiple future packaging options.”
Quick changeover is key
To complement the line’s major pieces of equipment, Golden Heritage installed machines from Kaps-All Packaging Systems (www.capsall.com) chosen for their ease of changeover. “To go from one container to another can be accomplished very quickly,” relates Gregory, using as an example the capper, which takes less than 10 minutes to change over. The entire line, he estimates, can be changed over in under an hour, with two to three operators.
At the front of the line, a Kaps-All Model AU-6C bottle unscrambler automatically inverts, ionizes, vacuums, and cleans empty bottles, fed from a stainless-steel hopper. The bottles are then placed upright onto a takeaway conveyor leading to the volumetric filler.
After filling, caps are applied using a Kaps-All Model C8 in-line eight-spindle capper. Induction seals are accomplished with an Auto-Mate (www.automatetech.com) AM-20 induction sealer. Bottles are then labeled and move to a six-lane, low-gravity accumulator from Shuttleworth (www.shuttleworth.com), where they await roboticcase packing.{mosimage
Future opportunities}
While the new line masterfully met Golden Heritage’s October 2007 production deadline for the Barry’s Busy Bee honey product, its job has only just begun. “We believe that the Barry’s Busy Bee bottle design has the potential to remain a part of our product line,” says Gregory. “However, this particular bottle design was not the only consideration when purchasing the equipment. This production line gives us greater flexibility in meeting the needs of our customers.”