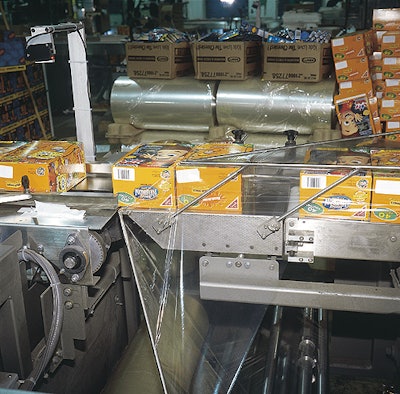
When contract packager Advertising Resources, Inc., opened its doors in September 2000, its three principal owners looked at their 40ꯠ sq’ of open warehouse space “and thought we’d died and gone to heaven,” recalls ARI president Richard Ehrie. He, Michael Banks, vice president of sales, and Warren Lawson, vice president of operations, are each owners of the minority business. “We were so proud to call that space our own, and we were good to go with three conveyors, a semi-automatic L-bar sealer, a heat tunnel, and a forklift truck,” Ehrie says.
At its inception, the company’s focus was assembling point-of-purchase displays, hence the name Advertising Resources, Inc. But its contract packaging business flourished. “We kind of fell into contract packaging, with Tootsie Roll giving us our start,” Ehrie says. Last December, ARI moved into a 266ꯠ sq’ facility in Alsip, IL. The plant now houses seven horizontal shrink wrappers with heat tunnels, two cartoners, and “a plethora of conveyors for hand-packing jobs,” says Ehrie. The equipment runs two shifts per day, five to seven days a week.
As many as 1귔 pallets are picked up every day from 24 bays at the Alsip facility, usually by customers’ trucks. Ehrie says prepackaged foods represent about 80% of the product packaged at ARI. All products are sold at retail. The company employs 20 full-time professionals and 115 to 120 temporary employees.
Ehrie credits “strategic alliances” with customers and suppliers for helping to build its business. Three of the key vendors are
• The Arpac Group (www.thearpacgroup. com), suppliers of five of the wrappers;
• Xpedx (www.xpedex.com), the International Paper packaging distributor that procures machinery and materials; and
• Alcoa Flexible Packaging (www.alcoa.com/ flexiblepackaging), whose primary role is to provide the polyvinyl chloride film used on the wrappers.
Local representation important
Since starting its business, ARI has purchased four Model TS37 Great Lakes side-seal horizontal wrappers from Arpac. “We looked at all kinds of equipment at Pack Expo in Chicago,” Ehrie recalls. “We had ‘loaner’ equipment in our plant from other vendors, and we compared machinery. In the end, we liked a lot of the features of the Arpac equipment.
“For one,” he says, “it lets us reposition the reciprocating cross-seal system from a vertical to horizontal position to accommodate different pack heights.” That can be done in 15 minutes by unscrewing four bolts and two quick-connect handles, turning the system, then putting it back together. The cross-seal system is used in a vertical position for packages that are taller than they are wide. “It’s a clear advantage that the TS37 offers,” says Ehrie.
“We also liked the way the equipment transitions packs from the infeed area into the machine,” he adds. “The equipment is high-speed and efficient. We also knew that if we needed parts, Arpac was just 10 miles away. We liked the local representation they offered, as did Xpedx and Alcoa.”
When Packaging World visited the plant in late February, ARI was within days of adding its fifth TS37.
How it works
ARI receives stretch-wrapped pallets of packaged products from many recognized food manufacturers, though Ehrie preferred not to divulge their names. Pallet loads of incoming goods are placed on one side of an area in the facility where packaging is done. Outbound pallet loads are on the other side, with the packaging lines in between. ARI typically unitizes several packages together, per customer instructions.
Many of these packs are sold at wholesale club stores and mass merchandisers, “where 60 percent of our growth is coming from,” says Ehrie.
Workers unpack incoming loads and place cartons, jars, or pouches onto the flighted infeed conveyor of the continuous-motion TS37. Photoeyes detect the incoming packs as they convey into a film tube. A slidable film rack makes it easy to load film rolls. The single-wound, flat film ascends from an unwind mounted on the rack just above floor level through dancer bar rollers to the TS37’s patented film former. The former folds the film over to create a tube. Film edges are sealed at the side by radiant heat, so there’s no mechanism contacting the film.
At the next station, the cross-seal system reciprocates as the product is conveyed into the film. The seal mechanism uses a hot knife to seal and cut between the packs on the conveyor. The action seals the trailing edge of the first pack simultaneously with the front of the next multipack. Meanwhile, the leading pack is conveyed into a Model MPD122260 heat-shrink tunnel.
At the discharge end of the heat tunnel, workers stack packs into display cases, trays, or shipping cases, depending on the customer order. Customers specify packaging materials used for secondary packaging at ARI. These boxes or trays are then hand-palletized before a forklift truck whisks them to an automatic stretch wrapper in the nearby shipping area. Because of the size of its new facility, ARI can store orders in its warehouse, a key advantage compared to competitive CPs who are often pressed for space.
Uptime and changeovers are critical
Ehrie says the shrink wrappers are capable of 80 individual packs/min, but the multipacks are usually wrapped at 30 to 60 bundles/min. “We put a lot of stress on the equipment, and we’ve worked hard to put together preventive maintenance programs with our partners,” he says. “We just can’t afford to be down. If we’re down, we fall farther and farther behind on our deadlines. And our customers are more and more demanding, with turnaround times becoming shorter and shorter.”
And with so many different package configurations and sizes necessary to fulfill customer orders, it’s no wonder Ehrie says, “quick changeovers are one of the most critical aspects of our business. We’re running five to ten jobs at any given time, so we’re constantly making changes, either on the hand-packing conveyors or on the equipment. We have to have flexibility and that’s why the Arpac machines are so important to us.”
The TS37 does not require multiple forming heads for different packs. It can be changed in minutes without tools.
Film switch brings advantages
Until November, ARI used a three-layer polyolefin coextrusion as its shrink film on the horizontal wrappers. When Alcoa pitched them on switching to PVC film, Ehrie had his doubts. “There was so much negative publicity about PVC that we weren’t real excited about it,” he admits. “But we evaluated it and found there are distinct advantages to using the PVC film, including its clarity.
“Using PVC also means we can use less energy to run our machinery.” Specifically, he says sealing and heat-shrinking temperatures range between 310°F and 320°F with PVC, compared to around 360°F with polyolefins. “So we’re talking about using significantly less electricity with PVC. The change also helps to lengthen the life of the equipment. Imagine the stress of tunnels working at 360 degrees for 16 to 20 hours a day, up to seven days a week.
“When we ran packs in polyolefin film through the heat tunnel,” he continues, “especially irregular package shapes or large multipacks, the polyolefin film would sometimes bunch up and create dog ears. The high temperatures also caused us to do some rewraps because the film expands before it shrinks down to the pack. When the heat expanded the polyolefin film, it sometimes overstressed the seals. With the lower temperatures of PVC, there’s less incidence of rewraps and that saves material and labor costs.” Ehrie explains that cross-sealing and heat-shrinking temperatures differ usually by 10° or less, “depending on dwell times and several other factors.”
Alcoa Flexible Packaging supplies its Reynolon® PVC shrink film to ARI in thicknesses ranging from 50 to 150 ga, though 60 ga is the most common. Web widths vary from 22” to 33”. The same gauges were used for polyolefin film.
To date, ARI has been pleased with both the PVC film and the horizontal wrappers. “Our rewraps are down two to three percent with the new film,” says Ehrie. “When you add up those material and labor costs over millions of pieces, those savings become significant.” The owner estimates that PVC and polyolefin film costs are a wash.
ARI was also able to reduce the width of the film it uses because of the side-sealing process of the TS37 as compared to two of its other wrappers. “Again, it’s only a two-inch difference, but that savings over the length of a run adds up, and it’s another reason why we went with the Arpac machines.”
The CP doesn’t have an exact timeframe for return on investment for this equipment. “It depends on the jobs and volume,” Ehrie says. “Volume is the key because the more volume you run on the machinery, the more you’re spreading your overhead costs over more pieces. That allows you to be cost competitive, and that’s critical for our business.”