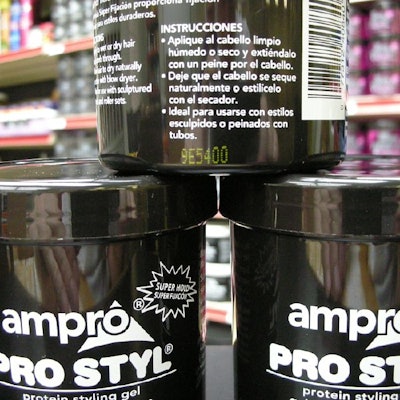
Ampro Industries, Inc., Memphis, TN, specialists in the manufacture of Afro-American hair-care products, needed a reliable, high-performance printing system to date- and batch-code its black plastic packaging. The company chose the PXR Ink Jet printing system from Hitachi (www.hitachi-america.us), distributed by Pak-Tec (www.pak-tec.com).
Ampro Plant Manager Roger Foster says, "We like to use yellow ink coding because it shows up well on our black containers. And we wanted a system that would minimize ink waste and clean-up requirements. We had looked at many coders that claimed we could use a yellow pigmented ink with the printers to code our black jars. None of them worked without high maintenance requirements."
After Ampro's extensive evaluations, reports Foster, "The Hitachi proved to be a perfect fit for our coding needs. And Hitachi technicians were prompt, professional, and one hundred percent involved in the installation, training, and start-up of the system. The ease of start-up was amazing.
"The coding system is so easy that any of my operators can learn how to do it in five minutes or less. We are achieving high-clarity codes at printing speeds up to 200 jars per minute without missing any jars. And we spend much less time and money on maintenance and clean-up. This is a huge improvement over the previous coding equipment."
Ampro Plant Manager Roger Foster says, "We like to use yellow ink coding because it shows up well on our black containers. And we wanted a system that would minimize ink waste and clean-up requirements. We had looked at many coders that claimed we could use a yellow pigmented ink with the printers to code our black jars. None of them worked without high maintenance requirements."
After Ampro's extensive evaluations, reports Foster, "The Hitachi proved to be a perfect fit for our coding needs. And Hitachi technicians were prompt, professional, and one hundred percent involved in the installation, training, and start-up of the system. The ease of start-up was amazing.
"The coding system is so easy that any of my operators can learn how to do it in five minutes or less. We are achieving high-clarity codes at printing speeds up to 200 jars per minute without missing any jars. And we spend much less time and money on maintenance and clean-up. This is a huge improvement over the previous coding equipment."
Companies in this article