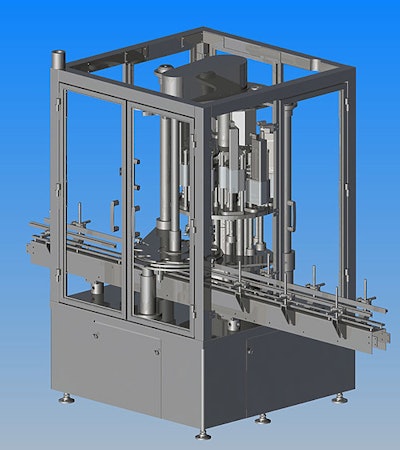
Progressive OEMs exploit the automation technology that equips the best European packaging machines
It’s no secret that Fortune 500 companies have been turning to European packaging machines since the end of the1990’s to gain flexibility throughput and maintainability. Now the same automation technology that’s supplanted PLCs and motion controllers in Europe has begun appearing in progressive North American designs.
Among the first to announce machinery designed from the ground up to take advantage of ELAU’s PaDrive automation technology are Capmatic Ltd. Pneumatic Scale and Sentry Equipment. Additional announcements are anticipated as the PACK EXPO International show approaches in early November.
Why now?
A natural question is ‘why now’ or more correctly ‘why not earlier?’
The answer is perhaps three-fold. From a purely practical perspective it has only been one year since ELAU shifted its focus in North Amercia from strictly an service and support role to pursue OEM sales. The company equips approximately $1 billion worth of machinery from Germany Italy the UK Sweden Holland and other exporting countries. Much of this equipment arrives in the U.S. Canada and Latin America.
Second until this Gen3 packaging machinery became accepted among the Fortune 500 companies the U.S. market in particular had been reluctant to move away from the familiarity of PLCs ladder logic and proprietary motion controllers. While corporate specifications helped alleviate a lack of standards for servo programming they had the unintentional consequence of stifling innovation.
Packagers have since recognized the severe performance handicap they’d imposed on themselves thanks in part to the efforts of the OMAC Packaging Workgroup. As a result machine builders are now free to pursue a best-of-breed control strategy.
Third Europeans have been more prone both to adopt international standards and to make performance-driven technology buying decisions. As a result when ELAU introduced its PacDrive system in 1998 European mechatronic machines designed around the integrated automation architecture appeared only one year later at Interpack 1999. In fact sales literature for ELAU-equipped filling machinery is believed to hold the first references to “third generation” packaging technology.
What’s new: Pneumatic Scale
Examples of the new generation of homegrown packaging machinery include the first rotary servo-driven bottle capper introduced by a U.S. company Pneumatic Scale a Barry Wehmiller Company. According to Pneumatic Scale Manager of Capping Engineering Tom McSherry the technology is revolutionary helping his company achieve “breakthroughs in capping torque control throughput and flexibility.”
The capper which is available in three frame sizes “features a cleaner cGMP design and requires virtually no maintenance” says McSherry. “In-process control and real-time process monitoring provide the ultimate in capping technology.”
Pneumatic Scale’s rapid pace of development highlights the dynamics of the global marketplace today. The PacDrive SCL servo technology was introduced in the U.S. just one year ago at PACK EXPO Las Vegas and already a North American builder is introducing it into its designs. Contrast this to the original PacDrive technology which took a few years to catch on here.
Canadian innovators: Capmatic Ltd.
It could be argued that Pneumatic Scale selected ELAU because there simply is no other source for technology comparable to the PacDrive SCL which is an integral servo motor/drive configuration that radically simplifies implementation of servos on rotating carousels.
Demonstrating that the trend is no fluke Capmatic Ltd.’s first ELAU-equipped machine uses conventional PacDrive servo motors and drives. A new 12-head in-line piston filler from Capmatic employs the technology to achieve unprecedented +/- 0.2% accuracy at speeds up to 150 bpm.
Capmatic Director of US Sales Michel Mosseau explains that “the servo-controlled filling nozzles and pistons are suited for full profile filling of non-symmetrical containers across a wide range of applications with no change parts required. The dockable configuration allows fast changeovers between standard high viscosity piston and mass flow meter filling heads.”
Shining through in the Capmatic application are the fundamental performance attributes of a centralized control strategy best practices for utilizing the IEC 61131-3 languages to best advantage a software object library containing 6 years’ of accumulated experience a truly integrated architecture that performs motion and logic in the same software program on the same processor and a hardware architecture that eliminates performance-robbing backplane connections and distributed motion tasks.
A sea change: Sentry Equipment
As Steven Prance explains Sentry’s new packing and overwrapping machine family “We felt there was an opportunity for an American supplier to provide equipment that meets the needs of the marketplace without going overseas.” Sentry best known for palletizing processing and conveying solutions primarily serves beverage and canned food manufacturers.
It was apparently time also for an American company to tackle all the challenges set forth by the OMAC Packaging Guidelines. These are the same guidelines that Procter & Gamble recently announced could save the company $15 million annually.
And so Sentry consciously set out to design a generation of packaging machines that fulfill OMAC’s visions. The result is a range of modular machines that can pack in trays trays and film pads and film or film only. These are believed to be the first US single-chassis machines capable of all four configurations. Traditionally separate packing and overwrapping machines were required.
“Our intent was to make the machine completely OMAC from the beginning” said Prance Sentry Director of Packer Engineering. “These are the first American machines we’re aware of coming standard with PackML™ across the product family. So they conform with the methods of reporting efficiency and are ideally suited for OEE.
“The goal is to be extremely repeatable to minimize the time required to climb out of changeover and up to operating efficiency. The performance will also be inherently measurable through the OMAC Guidelines.”
For more on ELAU and PacDrive visit www.elau.com PACK EXPO booth E-7523 or call 847 490 4270.
For more on Pneumatic Scale visit www.pneumaticscale.com PACK EXPO booth S-400 or call 330 923 0491.
For more on Capmatic Ltd. visit www.capmatic.com PACK EXPO Booth S-2872 or call 514 322 0062.
For more on Sentry Equipment email [email protected] or call 434 525 0769.