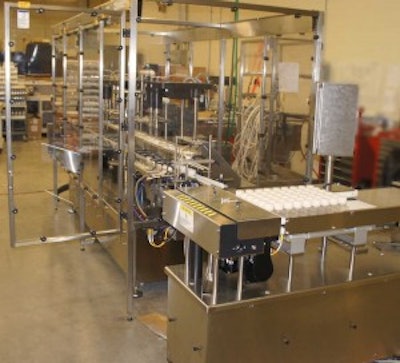
The bottles are kept sterile since the caps remain on the bottle until it enters the controlled HEPA-filtered environment or clean room. The pre-capped, sterile containers are brought to the filling suite and fed into the filling and capping machine. Filamatic’s linear and turret based Monobloc index the containers to an uncapping station where they are filled. The caps are then replaced and secured onto the containers.
The sterile liquid filling process accommodates a size range from 1mL to 1 liter, and a variety of container shapes including round, square, and rectangular. Containers can be delivered to the filler through a bulk unscrambling system or trays. Once the container enters the Monobloc, it is controlled in a set of lugs and indexed through uncapping, filling, and recapping functions.
The system automatically detects any containers that do not receive the proper amount of product or if a cap does not receive the proper amount of application torque prior to discharge. The uncapping and capping of the containers are accomplished with servo control chucks. Product metering options include piston pumps, peristaltic pumps, flow meter pumps, and lobe/gear pumps.