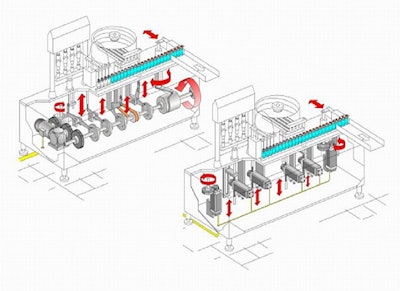
Abstract
In recent years the introduction of servo technology and PC-based control engineering has led to revolutionary changes in the construction of packaging machinery. Nowadays control and motive power engineering represent key technologies that yield significant competitive advantage in the packaging industry. However, the technology used varies widely and is influenced by the different standards of the various manufacturers. This causes extra development work and customized adaptations by both the manufacturers of packaging machinery and the users. This trend conflicts with the market demand for greater flexibility and performance at lower cost. The use of open and global control architecture resolves this conflict. The success of servo technology has brought its own problems; those problems, the solution concept developed by Bosch and the practical implementation of that solution will all be discussed in this article. The technology is available and was presented to the public for the first time at Interpack 2002 in Duesseldorf.
1. Introduction
In recent years the introduction of servo and intelligent control technology based on industrial PCs has led to fundamental changes in the construction of packaging machinery [1]. It has become possible to adapt rapidly to changes in packaging material, product, size and output without any manual adjustment. This is also true for the detection and correction of problems that occur during production. This has decisively improved the flexibility and efficiency of packaging machinery.
Fig. 1 shows a comparison between the old and new technology in a filling machine. In the conventional machine shown on the left, individual machine movements are actuated by a main drive and a mechanical vertical shaft. The control work required is minor.
In contrast, on the modern version shown on the right, nothing but servomotors have been used for the main movements. Synchronization of the individual movements is quite sophisticated and is performed via a central control unit. By analogy to the traditional drive solution, we can speak of an "electronic vertical shaft" on such a system.
As you can see, the enhanced functionality of packaging machines is being borne more and more by the control and drive technology. This increases the degree of complexity for the packaging technology provider and for its customers. This trend is gathering momentum and will continue in the future.
2. The problem
Packaging machinery users rightfully complain about the lack of uniformity and interchangeability in the control systems and operator interfaces currently on the market. Sometimes the solutions vary dramatically from machine to machine, even within the same manufacturer's product line. This, of course, inhibits easy and reliable communication between individual machines and with their environment, as well as requiring extra work for data storage. In some cases, it makes it almost impossible to train the operating personnel, who must face different operator controls on every machine.
This confusion can be traced to the explosive development of control and drive technology over the past few years. Individual solutions have been created independently of one another and are based on different standards. Therefore, they're often simply not compatible. We find that the high degree of flexibility has been acquired at the expense of additional and undesired complexity.
The packaging machinery market, however, now depends on innovation, flexibility and variety for growth. Further development and adaptation to customer requirements are essential prerequisites for this growth.
The task, then, is to find ways of reducing and controlling the complexity while retaining or creating value and competitiveness under the new conditions. This is true for both the packaging machinery manufacturer and the end user.
3. The solution
The ability to reuse functional units is of particular economic importance. This means strict modularization of machines – not only their mechanisms, but also their control and drive technology. The definition of control architecture with clear classifications and the assignment of component groups to these areas of architecture is crucial.
In order to react quickly and inexpensively to the needs for expanded functionality and modifications to standard or existing solutions, this control architecture must be open and global. These two terms are frequently used, but their features require unique definitions.
The features of open control architecture are:
• Availability of functions and components from several manufacturers
• Internationally standardized communication interfaces and protocols, supported by independent interest groups
• Interchangability of components within one area of the architecture without affecting adjacent areas
• Protection of intellectual property for the packaging machinery manufacturer
The features of a global control architecture are:
• Ability to scale systems using components from pre-existing groups
• Availability of consistent engineering tools for all areas of the architecture
• Standardized communication mechanisms for the areas of the architecture, independent of manufacturer and compatible with each other
There is no doubt that the future of the packaging industry belongs to open and global architectures [2ƻ].
In summary, these are the drivers for the use of open and global control architecture:
• Flexibility through interchangeability of the key components from different manufacturers
• The fulfilment of customer requirements at acceptable cost
• Independence from specific component manufacturers and their specialized know-how
• Protection of packaging machinery manufacturers’ own know-how
The product portfolios of the major automation manufacturers often bear the attribute “global." To date, though, this openness is hardly a reality. The introduction of truly open architecture will have an invigorating effect on competition among manufacturers of components and systems.
4. Implementing an open architecture
4.1 Analogy between open architecture and a house
Here's an analogy that describes an open control architecture. Imagine the appliances in the various rooms of a house. The house owner has every conceivable option. He can change the appliances in the various rooms from time to time without affecting the other rooms. He only needs to take the design of the house itself into consideration.
With control technology the interfaces and functions are different, but otherwise the analogy holds (Fig. 2). The new Bosch Packaging Control (BPC) platform, developed by Bosch’s Packaging Technology Division, defines the architecture, components and communication principles for these four areas:
• HMI (Human Machine Interface) / operator control interface
• Motion / drive technology
• Control / control unit
• Teleservice / remote servicing
Tested components released for use are available for each of the four areas and each category (e.g. large, medium and small control panels) in the form of modular kits. The list of currently approved modular elements can of course be enlarged as new components appear on the market, as long as they meet the specifications of the architecture.
4.2 Communication
The communication architecture is a multi-level structure that can easily be adapted to the different requirements of various packaging machines. The selected bus systems comply with standards that are recognized worldwide. Access to the individual components in the architecture is straightforward, as is the increasingly important communication between interlinked machines in a line. This is even more critical when the machines of a number of manufacturers have to be integrated within the framework of a larger-scale system. An industrial PC is used as the central communication platform, serving as an interface between the various bus systems.
The new BPC platform opens the door to a common and uniform operator control and communication concept with a wide variety of options; for example, access from a random terminal to all the individual machines in a packaging line.
Furthermore, it is now possible to link up with the user's factory data infrastructure. In this way, data can be interchanged for control parameters and settings, package markings or the desired throughput.
Communication is therefore ensured on several levels:
• within an individual machine
• between the different machines in a line and
• through to the overall factory control system
The conditions of open and global architecture are met by using Ethernet, PROFI bus and ASI bus systems and the SERCOS interface (Fig. 3).
Bus systems were originally introduced for the simple purpose of transferring drive and sensor signals to the central control unit. The main reason for doing this was to reduce wiring work and cost. Nowadays, bus systems represent an important component of the overall automation system and make possible the scope of information processing, globalization and modularization that is required in complete prefabricated and tested subassemblies.
4.3 Operator control interface
The operator controls the machine through a graphic operating interface which uses a touchscreen. A style guide for the graphic interface was written in collaboration with Prof. Pritschow of Stuttgart University and Prof. Zuehlke of Kaiserslautern University [4, 5]. This defines the menu structure, mask structure and basic dialogues and is intended to support the developer in designing the ergonomic layout of the operator interface.
This creates a uniform operator control system that extends beyond the Bosch product line. Operator control has an object-oriented structure related to the relevant subassemblies of the machine. Using the main menu, the operator can click on the subassembly that directly interests him; the system then displays the information and operator control facilities that pertain to that subassembly. This makes operator control very clear and simple. A multi-level password hierarchy controls which parameters and functions a specific operator is allowed to change.
Fig. 4 shows the structure of the operator interface, using a rotary filling machine as an example.
4.4 Control technology
Bosch has eliminated the current dependence on the manufacturer-specific hardware PLC (with its unique variations) in order to meet the conditions of an open and global system and to create products that can truly be used world-wide. Industrial PCs with the MS Windows NT® or MS Windows CE® operating systems are used as the hardware platform. These offer an improved cost/benefit ratio. In addition, the technical reliability of industrial PCs has been proven and is no longer subject to doubt.
Control of the machine functions is performed by a real-time-capable soft-PLC that is programmed in accordance with the IEC 61131-3 international standard. All programming languages of the IEC standard are available for use. The features provided originally by the industrial PC, such as integrated operator control (HMI), versatile communication facilities and a wide range of possible expansions by means of plug-in racks, all contribute to the openness and global nature of the system.
The constant demands for higher machine performance are covered at no additional cost by industrial PC technology, because the entire system is able to grow with the ongoing performance enhancements typical of the PC sector.
4.5 Software development tools
In developing the new BPC platform we have succeeded in covering the entire architecture spectrum with just two software development tools (Fig. 5). The software developers can now concentrate exclusively on these two tools with a corresponding increase in efficiency and quality.
4.6 Teleservice
The basis of teleservice, or remote servicing, is the transfer of data via the public telephone network between the machine supplier and a machine located at the customer’s site. This includes uploading and downloading of control software and machine data and can be expanded to remote programming and complete operator control of the customer’s machine by a service engineer based at Bosch. Audio and video transmissions with wireless video cameras are also possible for further support of the service personnel on site. The global communication principle inherent in the new BPC platform enables the optimum implementation of teleservice because remote access to all significant machine components is possible.
Teleservice is used for installation and commissioning, fault correction and repairs and also improves conventional maintenance. Several variations are available, as shown in Fig. 6.
The benefit to the end user is rapid access to help and minimized machine downtime. The user profits from the high level of technical expertise and experience of Bosch’s engineers, with a virtual presence at his own plant.
The benefits for the supplier are the improvement in service quality, increased customer satisfaction and reduced travel by service personnel.
5. Collaboration with international and national committees
Bosch puts its international orientation into practice by actively collaborating in the American OMAC (Open Modular Architecture Controls) group. There, guidelines for the design of control equipment for packaging machines are drawn up by drive and control technology suppliers, packaging machinery manufacturers and users. The new Bosch Packaging Control concept presented in this article meets or exceeds these guidelines.
Similar efforts are in progress at the German VDMA (Verband Deutscher Maschinen- und Anlagenbau e.V.; the Association of German Machine and Plant Construction). Bosch is also deeply involved in collaboration with this group.
6. Summary and outlook
Packaging technology is going through fundamental changes propelled by control and drive technology. The rapidly increasing complexity is controllable by the use of an open and global control architecture. An architecture-based control platform enables the designer to adapt existing development results to changed market requirements with the minimum possible effort and risk for both manufacturers and users. This includes being able to use components from different manufacturers for the same functions with a minimum of conversion work.
The prerequisites for this are:
• A breakaway from proprietary solutions and systems
• Compliance with the features of open and global architecture
• Utilization of, and compliance with, international standards
• Intercommunication between the component suppliers and agreement on standards for compatibility
And the best news of all: The technology described in this article is available now, and was presented to the public for the first time at Interpack 2002 in Duesseldorf.
6. References:
[1] Franz Thoren: Steuerungs- und Bedienkonzepte in Verpackungsmaschinen (Control and Operator Control Concepts in Packaging Machines), Technical Conference VVD2000, Dresden, 30./31.3.2000, Conference Records pp. 93-103
[2] Anton Ettenhofer: Workshop “Technik im Dialog” (Technology in Dialogue), VDMA News 04.02
[3] OMAC Pac Connect http://www.arcweb.com/omac
[4] Zuehlke, D.; Krauss, L.: Menschengerechte Gestaltung von Maschinen und Prozessbediensystemen (User-Friendly Design of Machines and Process Operator-Control Systems). Publishing house Shaker, Aachen.
[5] Eissler, R.; Charwat, H.-J.: Das Regelwerk – Normen und Richtlinien für nutzer-gerechte Mensch-Maschine-Systeme (The Rulebook – Standards and Guidelines for User-Friendly Man/Machine Systems). Computer&Automation 5/2000.
The authors:
Anton Ettenhofer grad.eng. is the department manager of Controls and Software Engineering at the Packaging Technology Division of Robert Bosch GmbH in Waiblingen, Germany.
Franz Thoren d.eng. is the technical general manager of the Packaging Technology Division of Robert Bosch GmbH in Waiblingen, Germany.