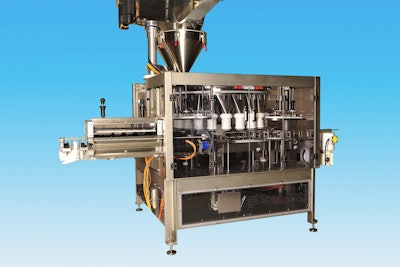
The Rotary Filler’s servo-driven design facilitates easy phasing of timing screws, turret stars, and auger filler electronically, which eliminates the time and expense associated with mechanical adjustments. The system stores turret/timing screw position when it is shut down and automatically re-homes after an e-stop condition when the system is restarted. Servo technology also promotes enhanced performance of the unit’s No Container/No Fill feature because it enables the auger to stop more quickly.
Continuous check weigh feedback allows automatic adjustments to improve fill accuracy rates.
A unique turret configuration enables the Rotary Filler to be quickly and easily disassembled into separate components without the use of tools. Because of the system’s unique design, users cost-effectively address changes in packaging height, diameter, or shape through the use of interchangeable plastic container adapters. Only one set of funnels is required. Funnels, adapters and other change parts are all no-tool quick disconnect, which dramatically improves the speed and efficiency of product changeover and cleaning operations.
A clear system base allows operators to visually inspect the unit during operation, while all programming and diagnostic functions are efficiently managed through the use of an Allen Bradley control system. A 10-ft. stainless steel conveyor is incorporated into the system.