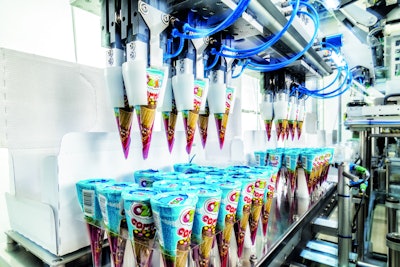
Turkish confectioner Şölen manufactures more than 200 different product varieties, including its popular Vital and Octavia chocolate brands, Luppo milk chocolate-coated cocoa cakes with marshmallow, and Criss Cross chocolate and hazelnut cream wafers. Since it was formed in 1989, the family-owned company has grown at an average rate of 20% per year, and now exports its chocolate and chocolate-based products to more than 100 countries worldwide. In 2013, the Şölen brand reached $200 million in sales.
Most of Şölen’s products are packaged using equipment from Gerhard Schubert GmbH. Over the past five years, Şölen has ordered 24 new packaging machines from Schubert. Says Erdogan Coban, member of the Şölen Executive Committee, “The greatest advantage of Schubert machines is that all packaging processes can be centrally controlled—this also applies to the new Flowmodul [Schubert’s new flow-wrapper module]. This is seamlessly integrated mechanically and at control level into the Schubert machine.”
Given its trust in Schubert, when Şölen prepared to roll out its newest confection—the Ozmo Cornet chocolate-filled miniature ice cream cone—at the end of 2016, it added two new modular TLM lines: one pick-and-place line integrated with a Flowmodul to create flow-wrapped trays of cornets or trays packed in cartons, and one line to fill trays and load them into 24-pack display cartons. The first system was installed at Şölen’s facility in December 2016, the second in spring 2017.
Each TLM line incorporates 15 robots, including:
- One TLM-F2 two-axis robot for transferring cornet products from production to the Transmodul transport robot
- One TLM-F4 four-axis pick-and-place robot for filling the gaps with product on the Transmodul format plate, if a product is missing
- Two TLM-F3 three-axis robots to unstack the thermoformed trays or boxes
- One TLM-F2 robot for erecting cartons
- Two TLM-F2 robots for inserting products into trays
- One TLM-F2 for closing the boxes or transferring filled trays into the Flowmodul chain
- Eight Transmodul single-axis, rail-based transport robots
The Flowmodul line can handle five packaging formats: 4- and 6-ct trays in flow-wrap bags or in two variants of 12-pack cartons, and 24-ct cartons. The second line only processes 24 packs for the moment, but can be extended at any time with a Flowmodul to accommodate the rest of the formats. Says Coban, “Since the product line can be automatically adjusted, format changes are quickly and easily implemented.”
During operation of the Flowmodul line, the Ozmo Cornet products are conveyed upright in two rows of 10 by means of a conveyor to the first station in the TLM machine. Here, the two rows are picked by the first TLM-F2 robot and are placed into the Transmodul’s transport plate, which holds 10 rows of 12 products each. From time to time, a product formation is placed on a side table. If a product is missing in a row in production, the TLM-F4 robots takes a cornet from the side table and fills the gap on the Transmodul.
Meanwhile, carton blanks are stored in an easily accessible magazine. The flat blanks are taken from the magazine by a TLM-F3 transfer unit and are horizontally presented for takeover by the TLM-F2 case-erecting robot, which performs carton erecting and glue application. The cartons are then placed on the Transmodul’s suction plate, which safely and accurately transports the cartons through the single stations of the machine.
As for the plastic trays that hold the individual cornets, they are stored in magazine plates. Denesting of the tray and its transfer to the Transmodul or into cartons is handled by the TLM-F2 transfer robot with the help of a dedicated suction tool. Next, the TLM-F2 loading robot takes groups of products from the grouping chain and inserts them into the plastic tray, either lying down (for four- and six-count flow wraps) or standing (for cartons).
As the products are taken from the moving chain conveyor, a sensor system on the TLM-F2 checks for the presence of lids on the cornets. This ensures that only products with undamaged wrapping are placed in the four- or six-count trays.
After carton loading, the TLM-F2 carton closing/transfer robot folds the lid and lifts it up in order to place closed cartons on the discharge conveyor. For the 4- and 6-ct trays, they are transferred to the infeed conveyor of the flow wrapper where they are packed in flow packs, after which they exit the line on the discharge conveyor.
To change the line over for different packaging formats, the magazine plates and upright folding frames are exchanged, as are the tools for the TLM-F3 that is unstacking the trays/boxes, the TLM-F2 tools on the erecting and closing robot, and the Transmodul plates.
For the second TLM line packing 24-ct cartons, operation of the line is the same, with the exception of the flow-wrapping function and the 4- and 6-ct thermoformed trays.
Each machine can produce 250 products/min, with two operators per machine. This results in 62.5 4-ct trays/min, 41.7 6-ct trays/min, 20.8 12-ct cartons/min, and 10.4 24-ct cartons/min.
“We rely on our business relationship with Shubert; above all, we appreciate their exceptional reliability,” Coban concludes. “Our partner, Schubert, always provides us with the best possible solution on time and to our exact requirements.”
See four other case histories in Part 1 of Packaging World's Robotics & Automation Special Report.