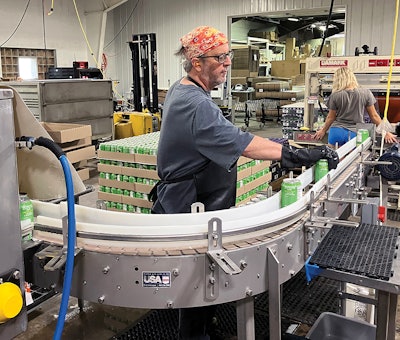
This content was written and submitted by the supplier. It has only been modified to comply with this publication’s space and style.
Multi-Conveyor recently installed two custom designed project conveyors laid out to optimize production space for a popular RTD (ready-to-drink) beverage co-packer, Arty’s Premium Beverages. Arty’s started 14 years ago with their own brand of Arty’s Premium Beverages RTD premixed cocktails.
At that time, there wasn’t much call for RTD products. Arty’s originally came in a 7 oz. glass bottle, doing most of the packaging by hand, even capping the bottles. Their line grew to aluminum cans for their popular Supper Club line, which birthed their RTD beverage co-packing business. The canned beverage market has grown exponentially within the last 5 years.
In the video, Ryan Mijal, VP and Co-Owner explains, “There’s a lot of new products getting launched. You see it in stores. We specialize in small volume product runs. So, when we started there wasn’t really any co-packing out there for small volume. If you wanted to do something it was all high volume. “Through our process of blending into carbonating, then carbonating hooks up to canning. So we blend everything to customer specs, do all of our quality checks that go into these tanks where we chill and carbonate off the customer’s specs in terms of carbonation and then they transfer to the canning line.”
That growth led to expansion and automation, with the help of Multi-Conveyor’s project manager, Chris Jeszke. Chris was able to identify ways to accomplish their objectives, reduce labor through custom conveyance and help with ergonomics. He redesigned the plant layout, taking exact measurements that lined up with existing equipment, saving money and optimizing production space.
Ryan explains, ‘When we designed the building layout, Chris came in and helped us decide what conveyor layout would work best to cut cost. The way we were dividing (the line) to get into the tunnel pasteurizer, they helped us come up with a better way to cut costs in terms of the actual conveyor process by just helping us with the layout.
Arty’s rework included the addition of a second filling line configured to get through an existing wall to their Jenry Tunnel of Love pasteurizer. With Multi-Conveyor’s recommendations, both fillers can now feed the pasteurizer by merging to a common conveyor, or they can off-load to a rotary table prior to the pasteurizer.
Multi-Conveyor provided stainless steel constructed 3.25” table-top conveyor sections from our pre-engineered Success Line catalog, commonly used in beverage applications. The automated lines consisted of one 18” long idle end that feeds a Palmer Beverage filler.
Post-filler, standard Success Line sections, included guide rails, chains and supports to make up a 10’ long intermediate section with 90˚ curve and 30” drive end (with motor and reducer).
At this section the new filling line can merge onto an existing Cask filler to feed the pasteurizer or divert directly to the hand-pack when pasteurization is not required.
The 90˚ conveyor was designed to transport cans from the discharge of the pasteurizer to the main hand-pack area. Product is then warehoused where they can be flow-wrapped in multi-packs or bulk shipped in pallets. Arty’s currently serves over 1,000 locations.
Ryan added because the conveyors were plug and play, Arty’s didn’t have to modify anything during the delivery or installation making it a very smooth transition. With the automated line configuration assistance from Multi-Conveyor, Arty’s has realized a 20% increase in production output.
Regarding future expansion, Arty’s VP told us they are looking at a new facility which would include some major expansion with conveyors. Ryan added, “We will continue to work with Chris on all future quotes due to the speed in quoting, ease to work with and great communication throughout the process."