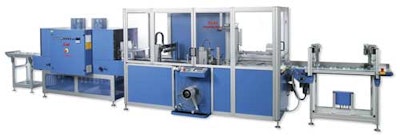
BVM Brunner GmbH & Co. KG is a manufacturer of film wrapping machines in Germany. Having decided to comply with EN ISO 13849-1, which provides safety requirements and guidance on the principles for the design and integration of safety-related parts of control systems, Brunner carried out renewed machine-risk assessments in order to update the safety concepts in its machines. Following this, the company decided to implement a new safety design for one of its machines. This initiative incorporated new and notable safety solutions from Pilz.
The machine in question is the Compacta Genius Servo. A fully automatic system with a continuous-motion cross-sealing jaw, it runs at speeds of 130 packs/min, depending on machine configuration and product type. The constantly heated sealing system seals all types of film, including PE, PVC, and OPP. The use of a vacuum conveyor ensures that at all times rectangular bags are produced and the product remains central to the machine.
The safety solution required for this machine needed to not only safeguard the operator but also to complement the flexibility and ease of handling required for processing a variety of products for different customers. The Pilz Safety Calculator, PAScal, was used to determine the required Performance Level (PL) and Safety Integrity Level (SIL) of the safety functions according to EN ISO 13849-1. The PL and SIL requirements, together with the handling requirements, were then matched with the PILZ product range within the PAScal Calculator library.
Brunner selected the new, compact, configurable safety relay, PNOZmulti Mini, to monitor safety functions. Despite its compact 45-mm width, the multi Mini with its 20 safe inputs and 4 safe semiconductor outputs (to SIL 3, PL e) covered all safety functions of the machine, including E-Stop, Light Barriers, and safety gates. The PC-based drag-and-drop PNOZmulti Configurator also minimized initial setup and enabled individual configuration for different customers and products.
The mechanical safety gate switches were replaced with low-maintenance, non-contact magnetic safety switches, PSENmag, which offered high tolerances for set up and switching distance, a clearly visible status indicator, and reduced engineering time due to plug-in cables.