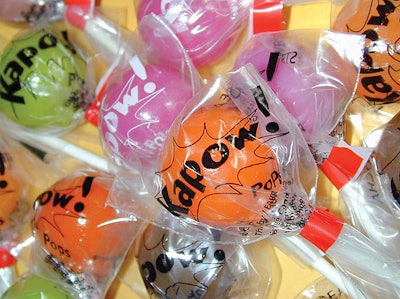
The cool-down takes place on a relatively short 14’ conveyor run that serves as the infeed to the packaging operation. The lollipops are in molds and can’t be properly removed from their molds until they’ve been cooled. Cooling now takes 10 minutes instead of the 20 to 25 minutes it took when product rode to the packaging line on a conveyor belt.
“We thought about purchasing a cooling tunnel for our existing conveyor,” says Bob Edgecombe, Carriage Candy principal and plant manager. “But they’re expensive and not adaptable enough for future needs.”
Edgecombe says that when he looked at the DynaCon system, he was impressed with the solidness of the high-impact plastic conveyor sections and their availability in a variety of widths. Even more important, the DynaCon system offered a wide array of accessories, including the cooling fans. He selected 32 of these fans to cool the Kapow! Pops, which ride in trays on a link belt. A variable-speed drive enables the conveyor operator to adjust the speed of the belt as required to ensure that the candy is sufficiently cool.
Edgecombe is pleased that when, in the near future, he needs to integrate a 90° radius turn and lengthen the conveyor run, the modularity of the DynaCon system will make it easy.